All kinds of Materials
Our team of highly experienced engineers ensures the perfect solution for customers before they place an order, providing the best guarantee for the quality of their products.
Material Selection
Our team of highly experienced engineers ensures optimal material selection for customers before order placement, providing the best guarantee for the quality of their products.
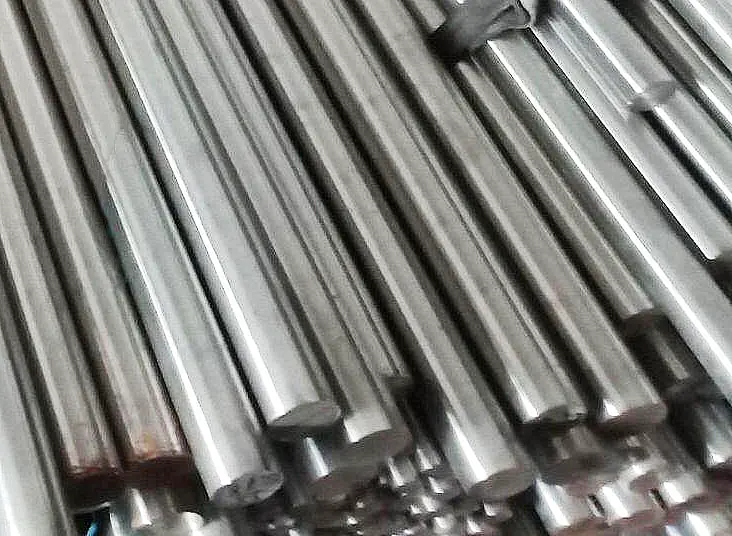
CNC Metal
Get high-quality custom aluminum CNC machined parts with fast turnaround and competitive pricing.
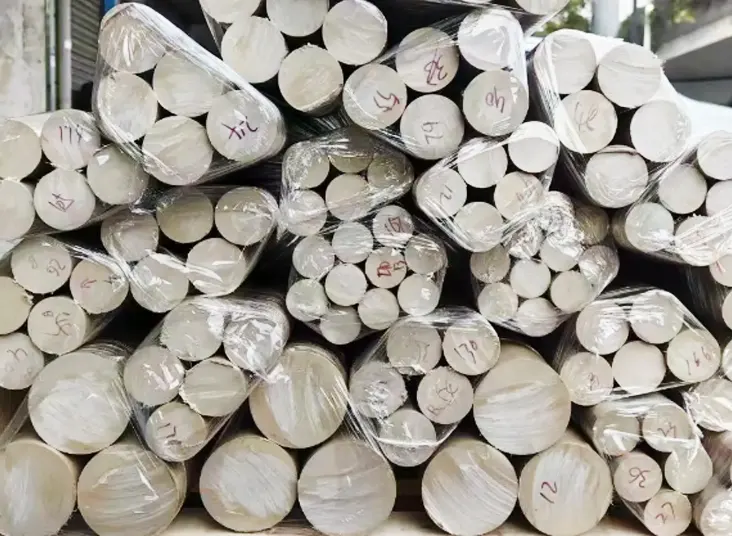
CNC Plastic
These CNC processes are traditional machining methods commonly used to shape plastic materials like plates, prototype rods, and more.
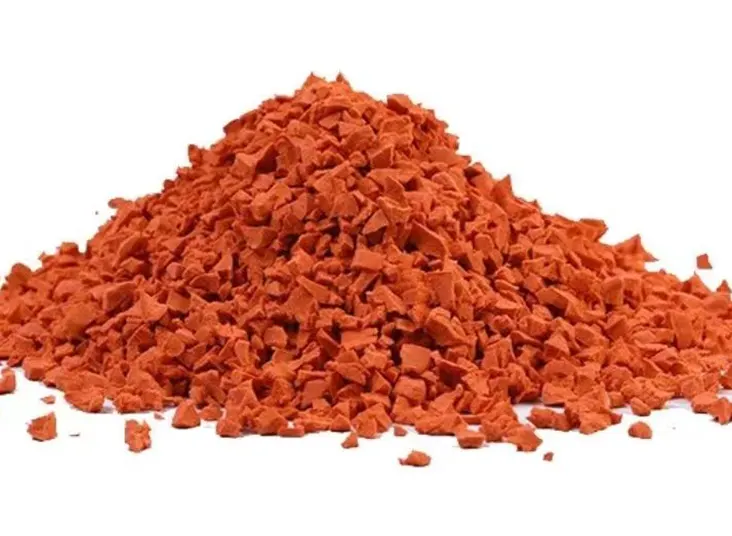
Injection Molding plastic materials
This type of processing commonly utilizes engineering plastics such as ABS, nylon, ULTEM, PC, and photopolymers.
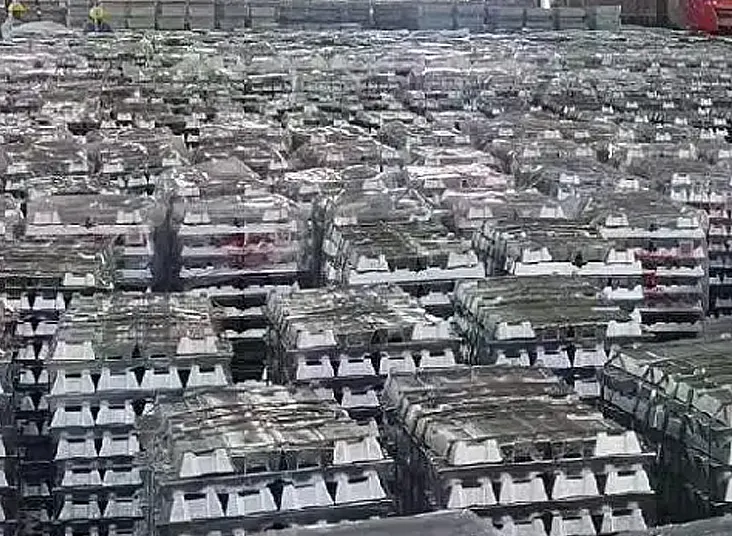
Die Casting Materials
Casting is one of the earliest hot metalworking processes developed by mankind, primarily using aluminum alloys, magnesium alloys, and zinc alloys.
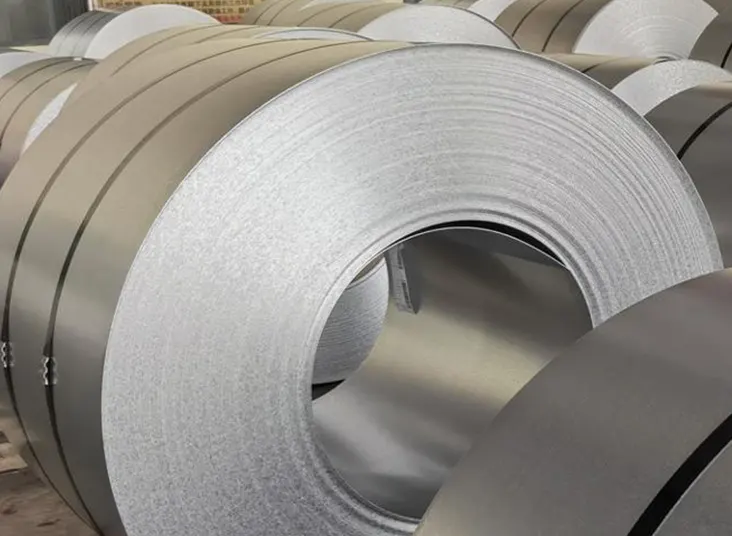
Sheet Metal Materials
Sheet metal processing requires materials with good ductility and weldability.
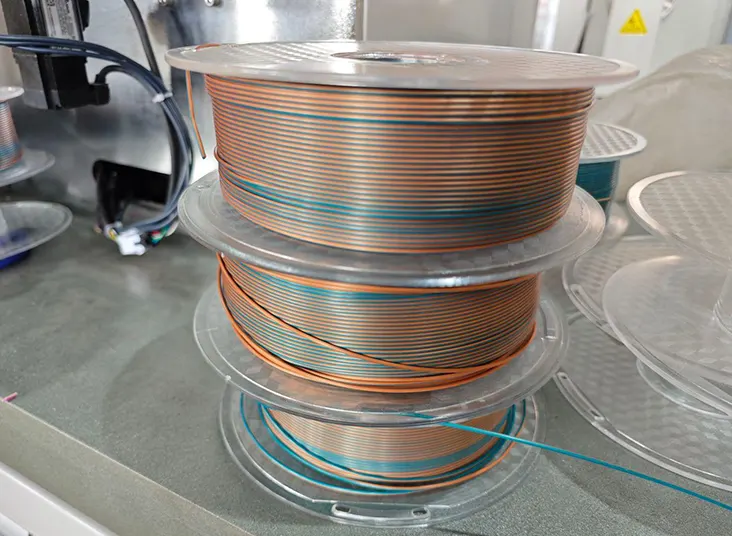
3D Printing Materials
Engineering plastics like ABS, nylon, ULTEM, PC, and photopolymers are commonly used for this type of 3D manufacturing.
why choice Material is so important in manufacturing industry?
Material selection is crucial in the manufacturing industry because it directly affects the performance, cost, and manufacturability of a product. Here are some key reasons why material choice is important:
1. Performance & Functionality
- Different materials offer varying strength, durability, heat resistance, and chemical resistance, impacting the overall functionality of the product.
- Example: Aerospace components require lightweight yet strong materials like titanium or carbon fiber, whereas automotive parts may use aluminum or steel for impact resistance.
2. Manufacturability & Process Compatibility
- The chosen material must be compatible with the selected manufacturing processes (CNC machining, injection molding, 3D printing, etc.).
- Example: CNC machining works well with metals and some plastics, whereas injection molding is best suited for thermoplastics.
3. Cost Efficiency
- Material costs can significantly impact production expenses. Selecting an optimized material balances performance with cost-effectiveness.
- Example: Using mild steel instead of stainless steel can lower costs in applications where corrosion resistance is not a priority.
4. Weight Considerations
- In industries like automotive and aerospace, lighter materials help improve fuel efficiency and performance.
- Example: Replacing steel with aluminum or composite materials in car body panels reduces vehicle weight and enhances fuel efficiency.
5. Durability & Longevity
- Choosing a material with high wear and corrosion resistance increases product lifespan and reduces maintenance.
- Example: Stainless steel for food processing equipment prevents rust and contamination, ensuring long-term use.
6. Environmental & Regulatory Compliance
- Many industries must follow strict environmental regulations regarding material use and disposal.
- Example: Using biodegradable plastics in packaging reduces environmental impact compared to traditional petroleum-based plastics.
7. Aesthetic & Surface Finish Requirements
- Some applications require specific textures, colors, or finishes to enhance appearance.
- Example: Consumer electronics often use anodized aluminum for a premium look and feel.
8. Thermal & Electrical Properties
- For applications involving high temperatures or electrical conductivity, material properties become crucial.
- Example: Copper is ideal for electrical wiring due to its excellent conductivity, while ceramics are used in high-temperature environments.
How to choice Material in manufacturing?
Choosing the right material in manufacturing is crucial for ensuring product performance, cost-effectiveness, and manufacturability.
Here’s a step-by-step guide to selecting the appropriate material:
1. Define Product Requirements
Mechanical Properties: Strength, hardness, toughness, wear resistance.
Physical Properties: Density, thermal conductivity, electrical conductivity.
Chemical Properties: Corrosion resistance, oxidation resistance.
Aesthetic and Surface Finish: Color, texture, polishability.
2. Consider Manufacturing Process
Machinability: How easy it is to cut, drill, or shape the material.
Formability: Suitability for casting, forging, stamping, or injection molding.
Weldability: If joining processes like welding or brazing are required.
3. Evaluate Environmental Factors
Operating Temperature: Can the material withstand high or low temperatures?
Chemical Exposure: Will the material be exposed to acids, moisture, or UV radiation?
Load and Stress Conditions: Will it endure impact, pressure, or continuous loading?
4. Balance Cost and Performance
Material Cost: Choose a cost-effective option without compromising quality.
Processing Cost: Some materials are cheaper but harder to machine, increasing labor costs.
Availability: Ensure the material is readily available in the required form and quantity.
5. Consider Post-Processing and Finishing
Surface Treatment: Plating, anodizing, painting, or heat treatment.
Dimensional Stability: Will the material expand or contract with temperature changes?
Wear and Tear: Will additional coatings or reinforcements be needed?
6. Comply with Industry Standards & Regulations
Follow ISO, ASTM, or DIN standards for specific applications.
Ensure compliance with safety, environmental, and recycling regulations.
7. Commonly Used Materials in Manufacturing
Metals: Steel, aluminum, titanium, brass, copper (used in structural, automotive, aerospace).
Plastics: ABS, Nylon, PEEK, Polycarbonate (used in consumer products, medical, electronics).
Composites: Carbon fiber, fiberglass (used in aerospace, sports, and automotive industries).
Ceramics: Alumina, zirconia (used in electronics, medical implants, and cutting tools).