Order custom Production Tooling for your idea.
Online Production Tooling service
Get high-quality plastic prototypes and durable production parts—request your free production tooling quote today!
- Free & Automatic DFM feedback
- Custom mold design services
- In-house mold production
- Tolerance: +/- 0.025 mm
Production Tooling Process
01
Creating the design
Creating the design
This step involves obtaining or developing the part design to be molded, including all required dimensions, features, and technical specifications.
02
DFM
DFM
Design for Manufacturability (DFM) focuses on optimizing part or product designs to improve ease and efficiency in the mold-making process.
03
Production Mold
Production Mold
Mold cavities and cores are produced using CNC machining or other methods, guided by precise design specifications.
04
Surface Treatment
Surface Treatment
Mold surfaces that contact molten material are treated to enhance material release and minimize friction.
05
Mold Assembly
Mold Assembly
All mold components—such as the cavity, core, inserts, and cooling channels—are integrated into the mold base during assembly.
06
Validation
Validation
Once assembled, the mold is tested and validated to confirm its performance and dimensional precision.
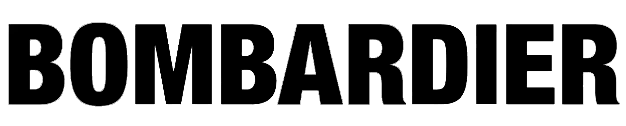
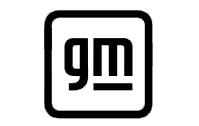
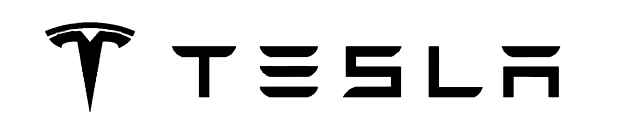
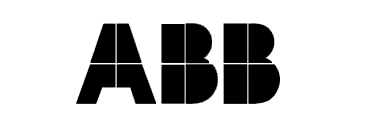
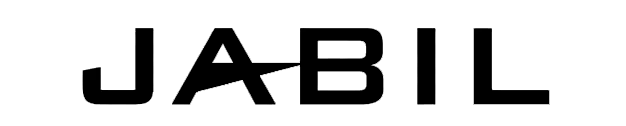
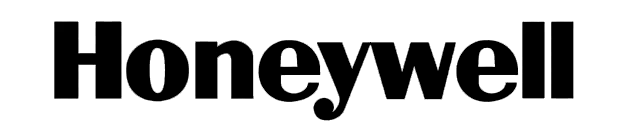
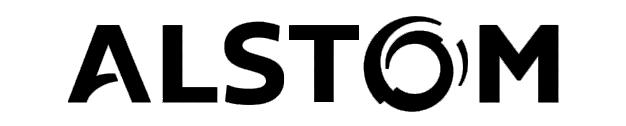
Why Choose Ours Production Tooling Service?
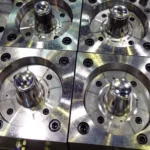
We specialize in precision insert injection molding, delivering high-quality, tightly-toleranced parts.
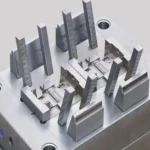
Receive expert wall thickness optimization and design recommendations within 48 hours.

Ensure precision alignment under 0.02mm between base and mold for structural integration.
Capabilities of Production Tooling Services
We provide top-quality plastic injection tooling services, delivering high-precision, finely finished parts at competitive prices.
Maximum Part:800×1000×400mm
Manimum Part: 5×5×5 mm
From 0.5 to 3mm
+/- 0.025 mm
Provide T0, T1, T2 samples
Inserts can be designed as either male or female,
each enhancing both the functionality and appearance of a product
Most orders can be completed within 15-45 working days
Design Guidelines
Optimize your designs for manufacturability with our expert guidelines and feedback, ensuring the best results in injection molding service
Wall Thickness Uniformity
Parting Line and Draft Angles
Material Selection
Tolerance and Fit
Cooling System Design
Ejection Mechanism
Surface Finish
Assembly and Maintenance
Materials for Production Tooling
Overmolding technology represents a breakthrough in multi-material integrated manufacturing, offering a wide range of material pairing possibilities to meet diverse industrial needs.
Choosing the Right Tool Steel
Requirement | Recommended Steel |
---|---|
High Volume Plastic Molds | H13, S136, NAK80 |
Corrosion Resistance | S136, 420 SS |
Cost-Effective Prototyping | P20 |
Mirror/Glossy Surface | NAK80, S136 |
High-Temperature Metal Dies | H13 |
Shock-Resistant Tooling | S7 |
Tool Steel Comparison Table for Production Tooling
Item | Hardness (HRC) | Machinability | Corrosion Resistance | Polishing Ability | Typical Applications |
---|---|---|---|---|---|
P20 | 30–32 (Pre-hardened) | ✦ Low | ✦✦✦ Good | ✦✦ Good | Plastic molds, prototype & medium runs |
H13 | 48–52 (After heat treatment) | ✦✦ Moderate | ✦✦ Moderate | ✦✦ Moderate | Die casting molds, high-temp plastic molds |
S7 | 54–56 (After heat treatment) | ✦ Low | ✦✦ Moderate | ✦ Moderate | Impact parts, cores, ejector components |
S136 / 420SS | 48–52 (After heat treatment) | ✦✦✦✦ High | ✦✦ Moderate | ✦✦✦ Excellent | Medical molds, food-grade, corrosive plastics |
NAK80 | 38–43 (Pre-hardened) | ✦✦ Moderate | ✦✦✦✦ Very Good | ✦✦✦✦ Excellent | High-gloss mold cavities, EDM finishing |
D2 | 58–60 (After heat treatment) | ✦ Low | ✦ Moderate | ✦ Moderate | Cutting dies, trimming tools, metal stamping |
Stainless Steel Comparison Table for Production Tooling
Item | Hardness (HRC) | Corrosion Resistance | Wear Resistance | Machinability | Polishing Ability | Typical Applications |
---|---|---|---|---|---|---|
S136 (AISI 420) | 48–52 (HT) | ✦✦✦✦ High | ✦✦✦ Good | ✦✦ Moderate | ✦✦✦✦ Excellent | Medical molds, optical parts, corrosive plastics (PVC, PC) |
420 SS | 48–52 (HT) | ✦✦✦✦ High | ✦✦✦ Good | ✦✦ Moderate | ✦✦✦ Excellent | Clear part molds, packaging molds, food & medical tools |
440C SS | 56–60 (HT) | ✦✦✦ Moderate | ✦✦✦✦ Excellent | ✦ Moderate | ✦✦ Moderate | Cutting tools, valve parts, bearing components |
316 SS | 20–25 (Annealed) | ✦✦✦✦✦ Very High | ✦ Moderate | ✦✦✦ Good | ✦✦ Moderate | Chemical & food equipment, non-molding components |
304 SS | ~20 (Annealed) | ✦✦✦✦ High | ✦ Moderate | ✦✦✦✦ Very Good | ✦✦ Moderate | Frames, housings, non-critical mold parts |
Choosing the Right Stainless Steel
Requirement | Recommended Stainless Steel |
---|---|
High corrosion resistance (e.g. PVC, humid environments) | S136 / 420 SS |
Mirror polish or high-gloss finish | S136 / 420 SS / NAK80 |
Medical or food-grade tooling | S136 / 316 SS |
Clear plastic parts molding | 420 SS / S136 |
Long service life & wear resistance | 440C SS |
Non-critical structural components | 304 SS / 316 SS |
High toughness and shock resistance | 420 SS (hardened) |
Non-magnetic and chemical resistance | 316 SS |
Choosing the Right Aluminum
Requirement | Recommended Stainless Steel |
---|---|
High corrosion resistance (e.g. PVC, humid environments) | S136 / 420 SS |
Mirror polish or high-gloss finish | S136 / 420 SS / NAK80 |
Medical or food-grade tooling | S136 / 316 SS |
Clear plastic parts molding | 420 SS / S136 |
Long service life & wear resistance | 440C SS |
Non-critical structural components | 304 SS / 316 SS |
High toughness and shock resistance | 420 SS (hardened) |
Non-magnetic and chemical resistance | 316 SS |
Aluminum Comparison Table for Production Tooling
Grade | Hardness (Brinell) | Thermal Conductivity | Corrosion Resistance | Machinability | Common Use in Tooling |
---|---|---|---|---|---|
7075 | 150 HB | ✦✦✦ Good | ✦ Moderate | ✦✦ Moderate | High-strength inserts, prototype mold frames |
6061 | 95 HB | ✦✦✦ Good | ✦✦✦ Good | ✦✦✦ Good | General-purpose mold bases, fixtures, jigs |
2024 | 120 HB | ✦✦✦ Good | ✦ Low | ✦✦ Moderate | Aerospace tooling, structural components |
5083 | 75 HB | ✦✦✦ Good | ✦✦✦✦ Excellent | ✦✦ Moderate | Marine molds, corrosion-prone environments |
QC-10 | 120–150 HB | ✦✦✦✦ Excellent | ✦✦✦ Good | ✦✦✦✦ Excellent | High-speed prototype molds, cavity blocks |
MIC-6 | ~65 HB | ✦✦✦✦ Excellent | ✦✦✦ Good | ✦✦✦✦ Excellent | Base plates, precision jigs, CNC fixtures |
From prototype manufacturing to mass production
We offer seamless transitions from rapid prototyping to mass production—from vacuum casting for small batches to precision production tooling for high-volume manufacturing.
Type | Purpose | Life Cycle | Material | Cost | Lead Time |
---|---|---|---|---|---|
Vaccum Casting | Prototype | 30~50 | silicon | $ | 2-3 Day |
Rapid tooling | Prototype Testing | 3,000 | Alumnuim Alloy | $$ | 7-10 Day |
Rapid tooling | Low-volume Production | 30,000 | Carbon Steel | $$ | 7-15 Day |
Production tooling | Medium-volume Production | 300,000 | Harden Tool Steel | $$$ | 30 Day |
Production tooling | Mass Production | Over 1,000,000 | Harden Tool Steel (Surface) | $$$$ | 35 Day |
Types of Production Tooling
We provide a wide range of injection mold tooling solutions tailored to your specific needs and applications. Whether you need prototype molds, production tools, or export-grade molds, TonzaMaking is your trusted manufacturing partner.
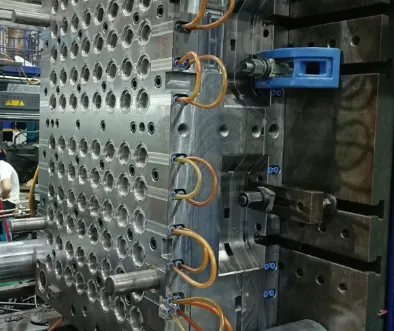
Multi Cavity Mold
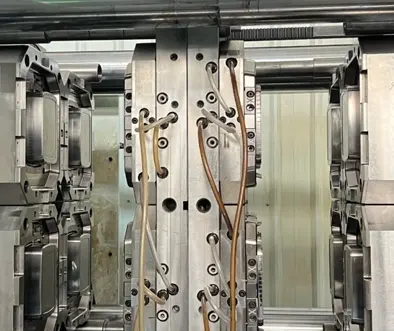
Stack Mold
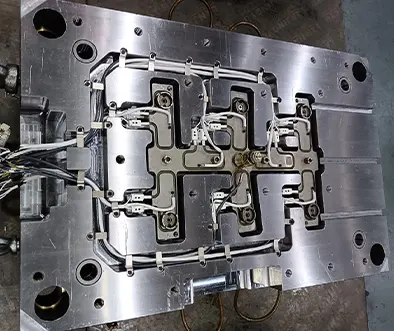
Hot Runner Tooling
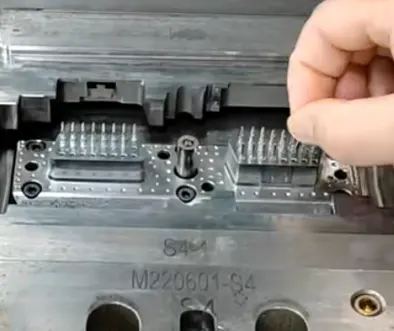
Insert Molds
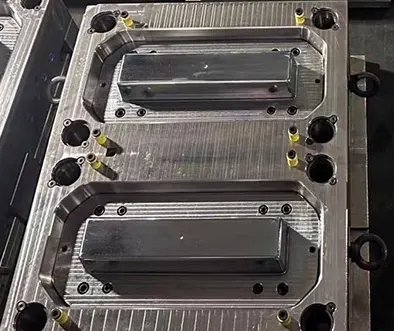
Overmolding Tooling
FAQ
We provide high-precision plastic overmolding services that ensure seamless bonding, enhanced durability, and a perfect fit for complex multi-material parts.
Production tooling refers to the custom-built tools, such as molds, dies, and fixtures, used in the mass manufacturing of parts with high precision and consistency.
We support a wide range of industries including automotive, consumer electronics, medical devices, aerospace, and industrial equipment.
Our tools are built using high-grade materials such as P20, H13, S136 tool steel, and aluminum grades like QC-10 and 7075, depending on the application and volume.
Prototype tooling is used for small batch or testing runs, usually made faster and with lower-cost materials. Production tooling is durable and designed for high-volume manufacturing.
Yes, we offer scalable solutions—from soft tools for pilot runs to hardened steel tools for millions of cycles.
Lead times vary based on complexity but typically range from 3 to 6 weeks. We also offer expedited tooling services.
Absolutely! Our engineers work closely with you to optimize designs for tooling efficiency, cost, and longevity.
Yes, we specialize in multi-cavity and family mold tooling to maximize production efficiency and reduce per-part costs.
All tooling is made in our advanced facility in Shenzhen, ensuring tight quality control and fast turnaround times.