Order your custom plastic parts.
Online Insert Molding service
Get high-quality plastic prototypes and durable production parts—request your free insert molding quote today!
- Substrate Wall Thickness: From 0.5 to 3mm
- Maximum Size: 800×1000×400mm
- Tolerance: +/- 0.025 mm
What is Insert Molding ?
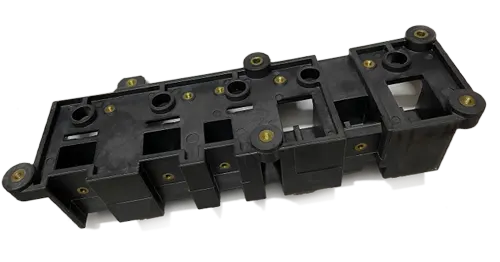
Insert molding is a powerful and efficient manufacturing process that combines the strength and functionality of metal or other components with the flexibility and cost-effectiveness of plastic. By embedding inserts directly into plastic parts during the injection molding cycle, manufacturers achieve strong mechanical bonds, improved part performance, and streamlined assembly—all in a single step.
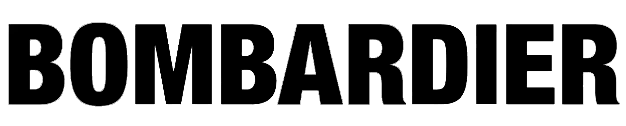
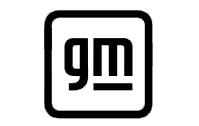
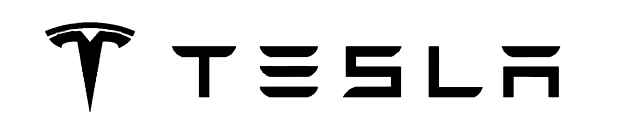
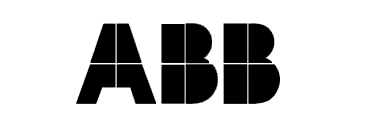
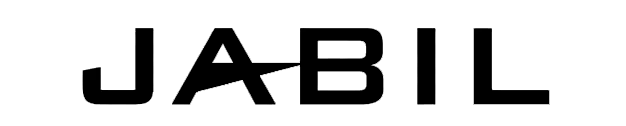
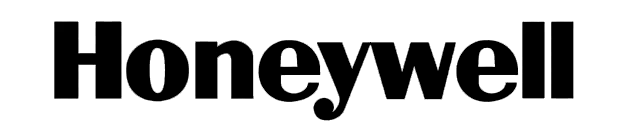
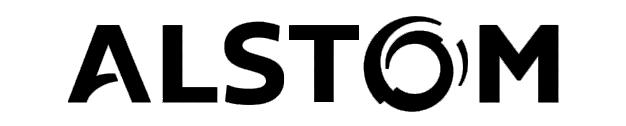
Why Choose Ours Insert Molding Service?
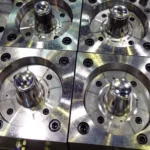
We specialize in precision insert injection molding, delivering high-quality, tightly-toleranced parts.
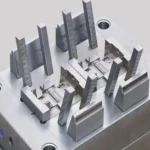
Receive expert wall thickness optimization and design recommendations within 48 hours.

Ensure precision alignment under 0.02mm between base and mold for structural integration.
Capabilities of insert molding Services
We provide top-quality plastic injection molding services, delivering high-precision, finely finished parts at competitive prices.
Maximum Part:800×1000×400mm
Manimum Part: 5×5×5 mm
From 0.5 to 3mm
+/- 0.025 mm
Provide T0, T1, T2 samples
Inserts can be designed as either male or female,
each enhancing both the functionality and appearance of a product
Most orders can be completed within 15-45 working days
Design Guidelines
Optimize your designs for manufacturability with our expert guidelines and feedback, ensuring the best results in injection molding service
Wall Thickness
Draft Angles
Insert Placement
Material Compatibility
Insert Tolerances
Overmold Flow
Thermal Considerations
Mechanical Locking Features
Materials for Insert Molding
Overmolding technology represents a breakthrough in multi-material integrated manufacturing, offering a wide range of material pairing possibilities to meet diverse industrial needs.
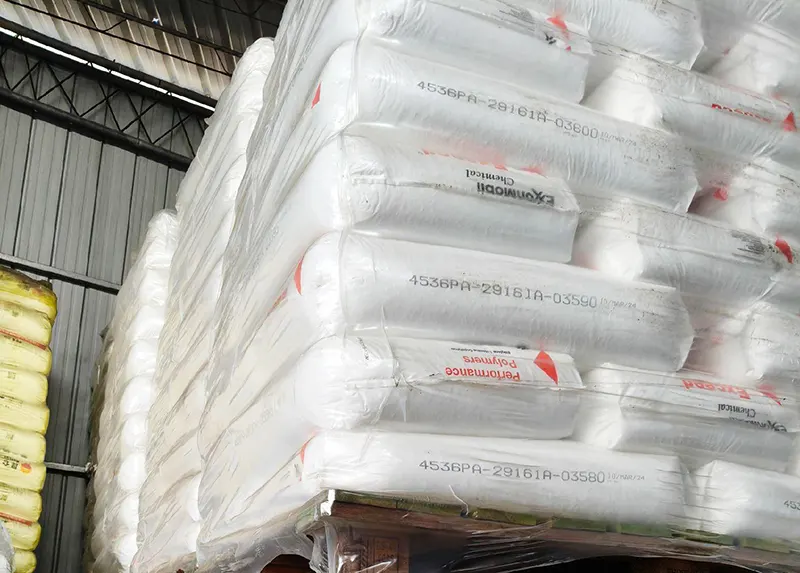
We have extensive expertise in working with hundreds of materials for injection molding, including standard plastics, custom blends, modified resins, rubbers, and more. Our deep knowledge covers their physical and chemical properties, as well as all relevant processing parameters.
Thanks to our strong and reliable supply chain, we can source these materials quickly and consistently—ensuring your production schedule stays on track without delays.
Insert materials
Insert injection molding is most commonly used to embed components such as screws or studs. Brass is the most frequently used material due to its corrosion resistance, affordability, and ease of machining—it does not rust and performs well in molded applications.
Other materials such as copper, aluminum, steel, hard plastics, ceramics, glass, and even other plastics can also be used as inserts.
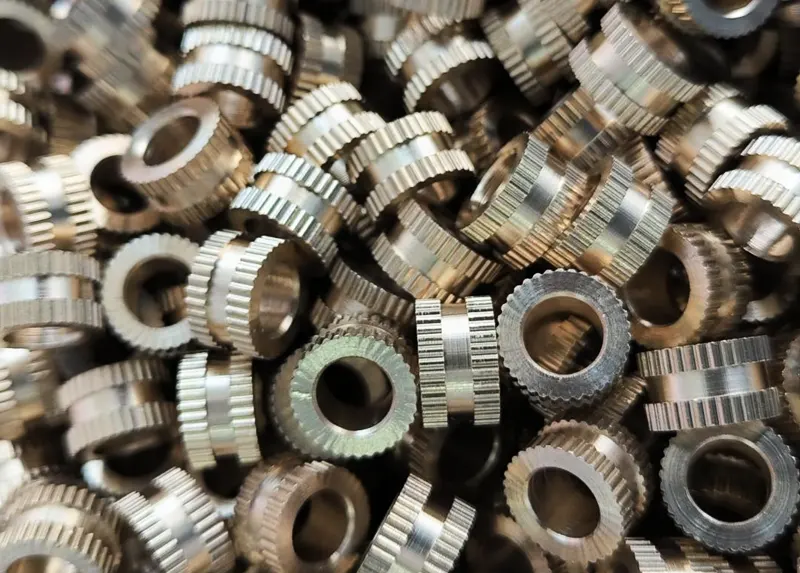
Overmolding vs. Insert Molding vs. Two-color Molding
Overmolding, Insert Molding, and Two-color Molding—are often used for multi-material or multi-functional parts, but they differ significantly in process, application, and tooling.
Overmolding | Insert Molding | Two-color Molding (2K Molding) | |
---|---|---|---|
Definition | Molding a soft or secondary material over a rigid substrate | Placing pre-made components (e.g., metal) into mold, then molding plastic around them | Simultaneously molding two different materials/colors using a dual-injection machine |
Materials Involved | Typically two different thermoplastics (e.g., TPE on PC) | Metal + plastic, or plastic + plastic | Two thermoplastics with good bonding compatibility |
Process Type | Sequential — substrate molded first, then overmolded | Inserts manually or robotically placed before injection | Simultaneous injection via dual-barrel machine |
Tooling | Two molds or one mold with multiple stages | Standard mold with insert-holding capability | Specialized dual-shot mold with rotary or sliding mechanism |
Adhesion Method | Thermal, chemical, or mechanical bonding | Mechanical interlocking or bonding | Strong chemical and thermal bond during co-injection |
Strength | Moderate to strong, depends on material compatibility | Strong mechanical bond | Excellent due to simultaneous fusion |
Applications | Soft grips, seals, medical tools, electronic enclosures | Metal-plastic assemblies, threaded inserts, connectors | Dual-color buttons, toothbrush handles, aesthetic housings |
Cycle Time | Medium — two-shot process with cooling time | Slower — manual or robotic insert placement | Fast — done in a single cycle with specialized machine |
Cost | Moderate — requires secondary molding step | Lower tooling cost, but longer cycle times | Higher initial tooling and machine cost, lower unit cost |
Bonding Risk | Depends on material compatibility and process control | High bonding strength due to mechanical fit | Very low — materials fuse in molten state |
FAQ
We provide high-precision plastic overmolding services that ensure seamless bonding, enhanced durability, and a perfect fit for complex multi-material parts.
Insert molding is a manufacturing process where metal or other components (called inserts) are placed into a mold and then encapsulated with plastic, creating a single integrated part.
Common insert materials include brass, copper, aluminum, stainless steel, ceramics, and even hard plastics or glass, depending on the application.
Insert molding improves part strength, reduces assembly time, enhances reliability, and allows for compact, integrated designs.
Insert molding is widely used in automotive, medical, electronics, consumer goods, aerospace, and telecommunications industries.
Brass is corrosion-resistant, easy to machine, cost-effective, and does not rust, making it ideal for many molded applications.
Yes! TonZA provides design support, including material selection and structural optimization, to ensure the best performance for your product.
We use insert features like knurls, grooves, or holes, along with proper molding parameters and material selection to ensure high-strength bonding.
While there are some limitations based on part complexity and mold design, our engineers will evaluate your design to ensure it is feasible for production.
Thanks to our strong supply chain and in-house mold making capabilities, TonZA can provide fast lead times—often within days for prototypes and short runs.