We provided best services to all customers.
Online High Pressure Die Casting service
We provide top-tier high-pressure die-casting services, delivering high-quality, finely finished, and precisely crafted parts at competitive prices.
- Tolerances: as fine as ±0.2 mm.
- Casting lead time: 5~7 days
- Tooling lead time: 35 days
Types of Die Casting
We offer comprehensive die-casting services, utilizing both Hot Chamber and Cold Chamber methods to meet various material requirements and project specifications.
Hot Chamber Die Casting
Hot Chamber Die Casting is a high-pressure die-casting process used for metals with low melting points, such as zinc, magnesium, and some lead-based alloys. Unlike Cold Chamber Die Casting, the injection system is submerged in the molten metal, allowing for a faster and more efficient casting process.
Cold Chamber Die Casting
Cold Chamber Die Casting is a high-pressure die-casting process used for metals with high melting points, such as aluminum, brass, and copper alloys. Unlike Hot Chamber Die Casting, where the injection mechanism is submerged in molten metal, the Cold Chamber method keeps the molten metal separate from the injection system.
Why Choose ours High Pressure Die Casting Service?
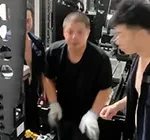
delivering exceptional results through experience, dedication, and strategic thinking.
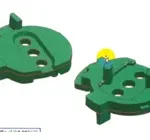
working closely with clients to understand their unique needs and goals
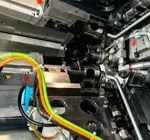
featuring the latest technology and advanced machinery to ensure precision, efficiency.
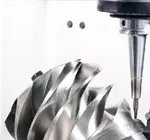
leveraging cutting-edge technology to manufacture intricate components
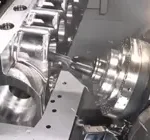
delivering exceptional value without compromising on quality or precision.
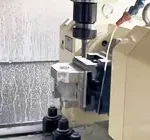
ensuring fast, efficient, and reliable production without compromising quality.
Capabilities of High Pressure Die Casting Services
Our High Pressure Die Casting services provide precise tolerances that adhere to industry standards, ensuring consistent accuracy and a perfect component fit.
Minimum Part Weight: 0.017 kg
Maximum Part Weight: 12 kg
Minimum Wall Thickness: 0.8 mm Maximum Wall Thickness: 12.7 mm
Minimum Part Size: ∅17 mm × 4 mm Maximum Part Size: 300 mm × 650 mm
1000 pcs
Design Guidelines
Optimize your designs for manufacturability with our expert guidance and feedback, ensuring superior results in high-pressure die casting.
Wall Thickness
2. Recommended wall thickness: 1.5mm – 4.5mm, depending on alloy and part size.
3. Avoid abrupt thickness variations to ensure proper material flow and solidification.
Draft Angles
2. Recommended draft:
Internal walls: 1°–2°
External walls: 0.5°–1°
3. Increase draft for deeper cavities to prevent sticking and reduce die wear.
Ribs & Gussets
2. Rib thickness should be 50-75% of the adjacent wall thickness.
3. Avoid deep bosses; use fillets and radii to prevent stress buildup.
Fillets & Radii
2. Minimum recommended fillet radius: 0.5mm – 1.5mm.
3. Avoid sharp edges to prolong die life and prevent cracking.
Undercuts and Cores
2. Use slides and cores only when necessary to avoid complexity and increase tool longevity.
Gating and Venting
2. Use overflow wells and venting channels to eliminate trapped air and gas.
Surface Finish
2. Avoid deep textures or intricate details that require additional finishing.
3. Specify post-processing requirements such as polishing, plating, or painting if necessary.
Tolerance Considerations
2. Minimize post-machining needs by designing near-net-shape components.
3. Include additional stock allowance for critical dimensions requiring machining.
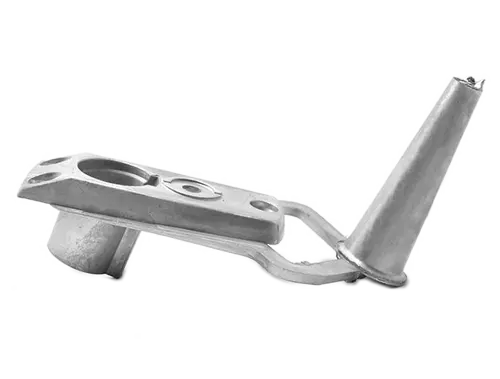
Materials for High Pressure Die Casting
We offer a wide range of materials for high-pressure die casting, ensuring the perfect fit for your specific application needs.
Customers can confidently select the right materials and focus on product manufacturing.
Aluminum alloys
Tipical: ADC7,ADC10, ADC12,ADC14 A380 and etc
Magnesium alloys
Tipical: AZ91D, AZ80M, AZ31B, AM60B, M2M.
Zinc alloys
Tipical:AZ91D, AZ80M, AZ31B, AM60B, M2M, etc.
Copper alloys
Tipical: ZQA19-2, ZQA19-4, ZQA19-7, ZQA19-10.
Surface Finishes
We are offering over 20 options of surface finishes to fulfill both your functional and aesthetic requirements.
As Cast
Brushing
Sand Blast
Polishing
Anodizing
Powder Coating
Applications
High Pressure Die Casting produces a wide range of parts and components, each customized to meet specific functional and aesthetic needs.
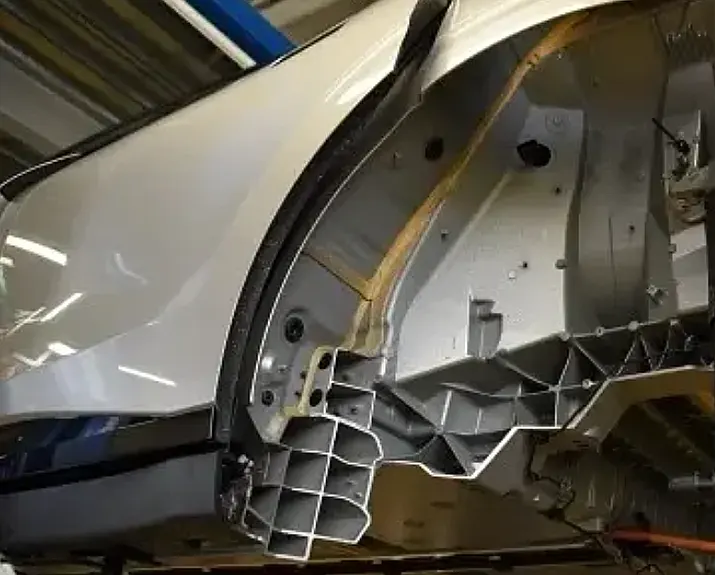
Automotive
- Cylinder heads, oil pans, engine brackets
- Manifolds, turbocharger housings
- Steering columns, calipers, master cylinders
- Gearbox cases, clutch housings
- Suspension parts, cross members, subframes

Aerospace
- turbine casings
- Wing brackets, fuselage fittings
- Compressor housings
- Seat frames, Seat frames
- Lightweight, high-strength structural element
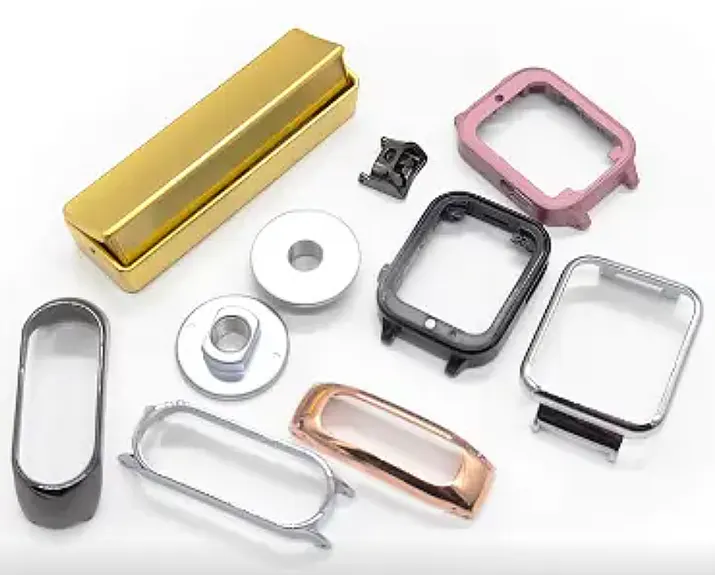
Electronic
- Heat Sinks: For power electronics, LEDs, CPUs
- Enclosures: Electrical housings, switchgear casings
- High-performance connectors for power transmission
- Used in electric motors, fans, and generators
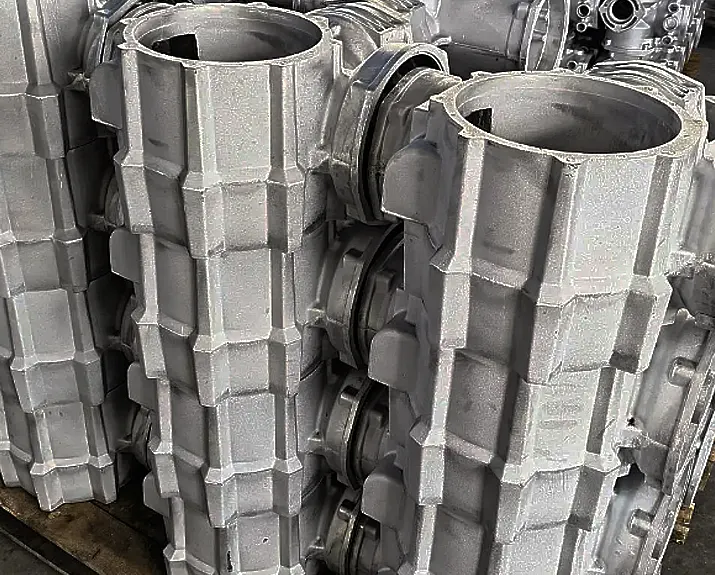
Industrial Machinery
- High-pressure casings, impellers
- Cylinder bodies, control valves
- Structural frames, joints
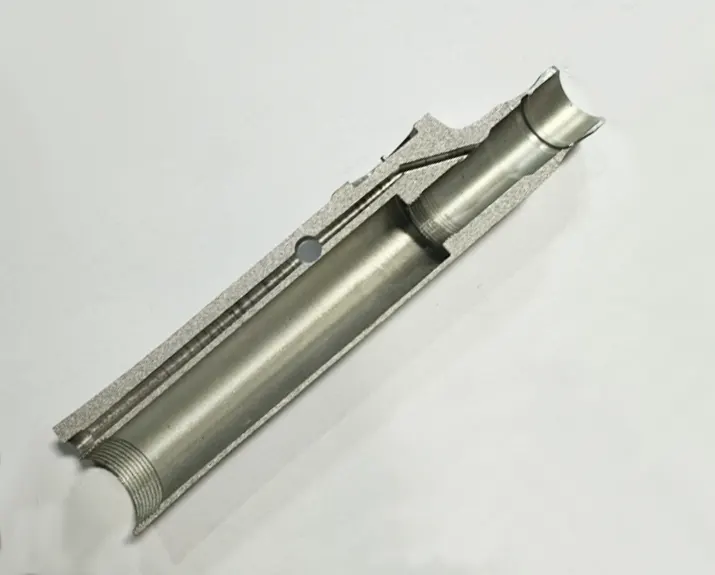
Medical
- MRI, CT scan machine frames
- Surgical Instruments: High-precision metal parts
- Lightweight and durable orthopedic parts
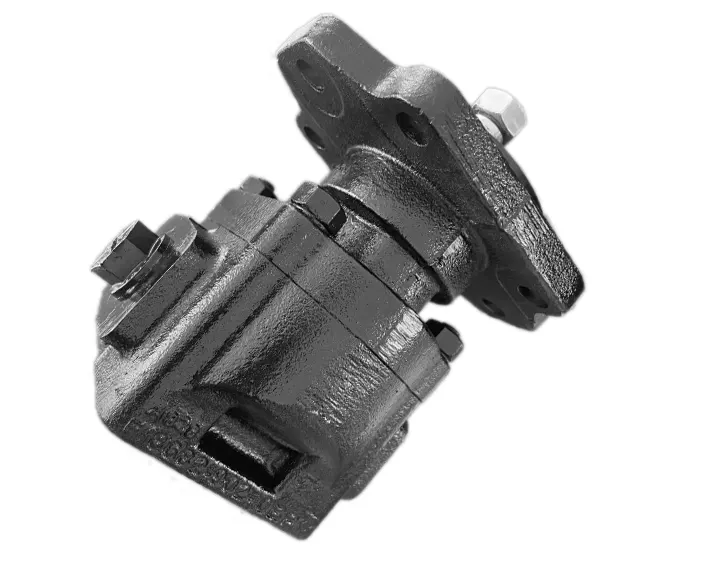
Military and Defense
- Armored vehicle panels
- Weapon casings
- Tactical equipment enclosures
FAQ
High Pressure Die Casting manufactures a variety of parts and components, each designed to fulfill specific functional and aesthetic requirements.
We work with aluminum alloys (A380, A360, ADC12), zinc alloys (Zamak 3, Zamak 5), and magnesium alloys, cooper alloys based on project requirements.
We provide die casting solutions for industries such as automotive, aerospace, electronics, medical devices, industrial equipment, and consumer goods.
Standard lead times range from 15 to 45 days, depending on the complexity and order volume.
We can produce die-cast parts ranging from a few grams up to 20kg, with sizes up to 600mm in length.
Yes, we provide CNC machining, deburring, polishing, anodizing, powder coating, painting, plating, and other finishing options.
Yes, we design and manufacture custom die casting molds based on your specifications. We also offer mold maintenance and modification services.
High-pressure die casting ensures high precision, excellent surface finish, tight tolerances, and cost-effective mass production.
We conduct strict quality checks, including material inspection, dimensional measurement, X-ray testing, leak testing, and surface defect analysis.
While die casting is best suited for high-volume production, we also support low-volume orders with cost-effective solutions.
We offer global shipping via sea, air, and express services. We handle all export documentation, including customs clearance and packaging.
Blog
Welcome to our blog, where we share insights into various manufacturing processes.