In the ever-evolving landscape of modern manufacturing, Design for Manufacturing (DFM) has emerged as a cornerstone principle that bridges the gap between product design and efficient, cost-effective production.
At its core, DFM refers to the engineering practice of designing products in such a way that they are easy to manufacture, assemble, and scale—without compromising functionality, performance, or quality.
In CNC machining operations, where precision, complexity, and material usage converge, DFM plays a particularly critical role.
Complex parts with intricate geometries demand a deeper understanding of manufacturing constraints and process capabilities.
By embedding DFM principles early in the design cycle, engineers can significantly reduce machining time, material waste, tool wear, and rework—ultimately accelerating time to market and lowering total production costs.
The importance of DFM is further underscored in high-mix, low-volume manufacturing environments, where the agility to adapt designs quickly and efficiently directly impacts competitiveness.
In this context, DFM is not merely a set of guidelines but a strategic methodology—one that requires holistic thinking about how every design decision influences downstream manufacturing steps.
This section sets the foundation for exploring how DFM principles, when integrated with structural optimization techniques, such as modular design and topology optimization, can elevate the performance and manufacturability of complex components produced via CNC machining centers.
We begin by examining the core concepts of DFM and its relevance to machining operations, before advancing into detailed strategies that enhance both design efficiency and production feasibility.
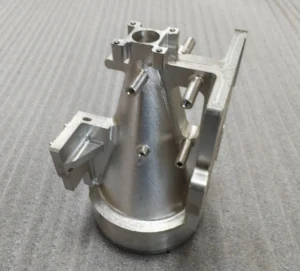
Challenging the Initial Design
The initial design concept often represents the foundational vision for a product but rarely embodies the optimal solution for efficient manufacturing.
In the context of CNC machining, particularly for complex processed components, it is imperative to critically evaluate and challenge the original design intent from the outset.
This process is fundamental to uncovering hidden inefficiencies, identifying potential manufacturing bottlenecks, and ensuring that the design aligns with practical machining constraints.
Challenging the initial design demands a rigorous and systematic approach that transcends conventional assumptions.
It involves deconstructing the design to understand every feature’s purpose, complexity, and manufacturability impact.
Such a detailed review facilitates the identification of unnecessary complexities, over-tolerancing, and features that increase machining time or risk of defects.
Key actions to undertake include:
- Comprehensive Review of Original Drawings: Analyze all dimensions, tolerances, and specifications to detect areas where precision may be unnecessarily tight or features may be overly complex relative to functional requirements. Understanding these parameters enables engineers to propose design refinements that reduce machining cycles without compromising performance.
- Product Teardown and Reverse Engineering: When applicable, physically disassembling existing products or prototypes offers invaluable insight into the real-world challenges faced during manufacturing and assembly. It reveals hidden design issues and opportunities for simplification or consolidation.
- Benchmarking Against Competitors and Lead Users: Studying competing designs and consulting end-users or production experts can provide practical perspectives on design-for-manufacturing trade-offs and industry best practices, guiding improvements that enhance both cost-effectiveness and usability.
- Collaboration with Contract Manufacturers and Machining Experts: Early and active engagement with manufacturing partners brings critical process knowledge into the design phase. Their insights on tooling limitations, machine capabilities, and optimal setups can steer the design towards greater manufacturability and reduced cycle times.
- Exploration of Alternative Solutions and Existing Technologies: Investigating available materials, manufacturing techniques, and design alternatives—such as modular components, standardized features, or hybrid manufacturing methods—can unlock innovative pathways to streamline production.
Ultimately, challenging the initial design is a disciplined exercise in balancing innovation with pragmatism.
It ensures that the final component design not only meets functional and aesthetic requirements but is also inherently optimized for efficient CNC machining, thereby driving significant cost savings and enhanced product reliability.
Five Pillars of Effective DFM in CNC Machining
CNC machining Design for Manufacturing (DFM) requires designers to strategically balance their intent with real-world manufacturing capabilities.
Successful implementation hinges on adherence to five foundational pillars—each addressing critical aspects that collectively enable the creation of high-quality, cost-efficient, and manufacturable parts.
These pillars serve as guiding principles that CNC engineers, designers, and manufacturers must integrate early and throughout the product development cycle.
Process Optimization
Selecting the appropriate manufacturing process is paramount in achieving cost efficiency and meeting quality expectations. In CNC machining, this entails matching the machining strategy to production volume, part complexity, and functional requirements.
Engineers must consider factors such as the number of axes, machine tool capabilities, tooling availability, and cycle times.
For example, low-volume production or prototypes may benefit from multi-axis machining to reduce setups, whereas high-volume parts might prioritize simpler, repeatable operations to maximize throughput.
Thoughtful process selection minimizes cycle time, reduces tool wear, and streamlines workflows, directly impacting lead time and unit cost.
Design for Manufacturability
Designers must inherently align their design considerations with machining capabilities and constraints.
This includes emphasizing geometric simplicity, minimizing undercuts or features that require special tooling, and designing for accessibility to facilitate efficient tool paths.
Incorporating appropriate tolerances is critical; overly tight tolerances increase machining complexity and cost without proportional functional benefit.
Designers should optimize part geometry to reduce the volume of material removed, favoring features that enable stable fixturing and minimal repositioning.
Employing design software with integrated DFM analysis can help identify problematic features early, enabling iterative refinements before physical production.
Material Selection and Utilization
Material choice profoundly affects machinability, cost, and part performance. Engineers favor metals like aluminum and brass for their ease of machining and cost-effectiveness, while they use exotic materials such as titanium or high-strength alloys with specialized tooling and slower cutting speeds, which elevates costs.
Selecting raw material forms—whether bar stock, plate, or forging—should reflect the most efficient path to the final geometry, minimizing waste and processing time.
Collaboration with material suppliers and machining experts ensures selection of materials that fulfill mechanical and environmental requirements while optimizing manufacturing efficiency.
Environmental and Functional Considerations
A robust DFM approach extends beyond pure manufacturability to incorporate the product’s intended operating environment and lifecycle conditions.
Designs must account for external stresses, thermal fluctuations, corrosion potential, and wear mechanisms to ensure durability and reliability.
Incorporating these considerations early can prevent costly redesigns and material substitutions downstream.
Furthermore, anticipating environmental influences enables designers to specify appropriate surface treatments or coatings compatible with machining processes, further safeguarding part performance.
Compliance, Testing, and Quality Assurance
Designs must comply with relevant industry standards, regulatory requirements, and internal quality benchmarks to ensure market acceptance and safety.
Early integration of compliance considerations within the design process—such as UL, ISO, or specific client certifications—reduces the risk of costly rework or product recalls.
Planning for inspection accessibility and incorporating design features that facilitate non-destructive testing, in-process monitoring, and quality control checkpoints enhances manufacturing robustness.
Effective DFM anticipates quality assurance needs and harmonizes them with manufacturing workflows, ultimately fostering consistent product excellence.
These five pillars collectively empower CNC machining providers and designers to minimize costs, reduce production risks, and accelerate time-to-market, all while maintaining the highest standards of product quality and functionality.
Integrating these principles into your design process is essential to unlock the full potential of CNC manufacturing capabilities and gain a competitive edge in today’s demanding markets.
DFM Challenges and Practical Considerations
Design for Manufacturing (DFM) within the context of CNC machining is a critical enabler of efficient production, yet it is fraught with complex challenges that demand both technical insight and practical foresight.
Navigating these challenges requires a holistic understanding of the interplay between design intent, material characteristics, machine capabilities, and operational constraints.
Below, we delve into the key obstacles and pragmatic factors that influence the successful implementation of DFM principles.
Balancing Design Complexity and Manufacturability
One of the foremost challenges in DFM is reconciling intricate design requirements with the inherent limitations of CNC machining processes.
Designers who incorporate highly complex geometries—often essential for functionality or aesthetics—can cause prolonged machining cycles, increased tooling costs, and a higher risk of manufacturing defects.
Designers must judiciously evaluate which features are critical to performance and which can be simplified without compromising integrity.
Achieving this balance demands iterative collaboration between design engineers and manufacturing specialists, leveraging simulation tools and rapid prototyping to validate manufacturability before full-scale production.
Tolerance Management and Quality Assurance
Specifying tolerances that are unnecessarily tight or inconsistent across features can dramatically inflate production costs and inspection complexity.
Conversely, overly loose tolerances may undermine product functionality and reliability.
The challenge lies in defining tolerance zones that reflect functional necessity while remaining within the realistic capabilities of machining equipment and processes.
Additionally, ensuring that these tolerances can be consistently met through robust quality control mechanisms—such as coordinate measuring machines (CMM), in-process probing, and statistical process control—requires early planning and integration within the design phase.
Material Machinability and Cost Implications
Material selection inherently influences machining feasibility and cost.
Materials with poor machinability, such as hardened steels or exotic alloys, impose greater tool wear, slower feed rates, and increased risk of thermal distortion.
These factors elevate both cycle time and tooling expenditure.
Designers face the practical consideration of balancing material performance criteria with machinability to optimize overall production economics.
Engaging material scientists and CNC process engineers during the design stage enables informed trade-offs that can enhance manufacturability without sacrificing product quality.
Fixturing and Workholding Constraints
Effective fixturing is a critical, yet often underappreciated, aspect of CNC manufacturing. Complex part geometries may require elaborate workholding solutions to ensure stability and accuracy during machining operations.
Designing parts that facilitate straightforward fixturing—through incorporation of locating features or uniform surfaces—can significantly reduce setup times and improve machining precision.
However, achieving such design characteristics within the constraints of product functionality presents a notable challenge requiring cross-disciplinary expertise.
Integration of DFM with Supply Chain and Lead Time
Practical implementation of DFM must consider not only the technical manufacturing challenges but also the broader supply chain dynamics and time-to-market pressures.
Selecting suppliers capable of delivering raw materials, tooling, and machining services within tight schedules is vital. Additionally, design decisions must accommodate potential variability in supplier capabilities and process repeatability.
An agile and communicative supply chain, coupled with design flexibility, can mitigate risks associated with lead time delays and production bottlenecks.
The challenges and practical considerations inherent to DFM in CNC machining demand a proactive, interdisciplinary approach that integrates design innovation with manufacturing pragmatism.
Addressing these complexities early in the product lifecycle ensures optimized manufacturability, cost efficiency, and ultimately, superior product performance.
DFM Checklist for CNC Machining
To systematically embed Design for Manufacturing (DFM) principles into CNC machining workflows, a comprehensive checklist serves as an indispensable tool for engineers and designers.
This checklist not only guides the evaluation of manufacturability but also facilitates cross-functional collaboration and continuous process improvement.
The following critical elements form the foundation of an effective DFM checklist tailored to CNC machining environments:
Design Simplification and Feature Optimization
- Have all unnecessary complex features been identified and eliminated or simplified to reduce machining time and tooling complexity?
- Are features standardized where possible to leverage existing tooling and reduce custom setups?
- Does the design minimize the need for multiple machine setups by consolidating features accessible in a single orientation?
Material Selection and Compatibility
- Is the chosen material optimized for both functional performance and machinability?
- Has the impact of material hardness, thermal properties, and chip formation on machining efficiency been thoroughly assessed?
- Are alternative materials considered that may reduce machining difficulty and cost without compromising product requirements?
Tolerance and Surface Finish Specification
- Are tolerances applied only where functionally necessary and consistent with achievable machining capabilities?
- Has a clear hierarchy of tolerance zones been established, differentiating between critical and non-critical dimensions?
- Are surface finish requirements realistic and aligned with standard CNC machining processes to avoid unnecessary finishing operations?
Fixturing and Workholding Considerations
- Does the design incorporate features that facilitate secure and repeatable fixturing during machining?
- Have potential challenges related to part stability, accessibility, and orientation been anticipated and addressed?
- Is the number of setups minimized through design decisions that favor machining from fewer orientations?
Tool Access and Machining Strategy
- Are all critical features accessible with standard CNC tooling without requiring specialized or custom tools?
- Has the design accounted for appropriate tool diameters, lengths, and cutting paths to avoid collisions or excessive tool deflection?
- Are internal corners and radii designed to accommodate tool geometry, preventing sharp edges that increase machining difficulty?
Heat Management and Machining Forces
- Has the design considered the effects of heat generation and dissipation during machining to prevent thermal distortion?
- Are features arranged and dimensioned to minimize excessive machining forces that could cause part deformation or tool wear?
Cost and Lead Time Implications
- Has the design been reviewed for opportunities to reduce cycle time and tooling costs without compromising quality?
- Are production volumes and batch sizes aligned with machining strategies to optimize tooling and setup investments?
- Has collaboration with suppliers and machine operators been established to validate manufacturability and identify cost-saving measures?
Quality Assurance and Inspection Planning
- Have you clearly identified critical dimensions and features for inspection, ensuring practical access for measurement tools?
- Has the design incorporated datums and reference points that facilitate accurate and repeatable quality control?
- Are inspection methods and frequency defined by tolerance requirements and production volumes?
This checklist serves as a strategic framework to guide designers and manufacturing engineers through a methodical review of design elements, ensuring manufacturability, cost-effectiveness, and quality excellence in CNC machining projects.
By rigorously applying this checklist early and throughout the design process, organizations can significantly reduce costly revisions, streamline production, and deliver superior products with accelerated time-to-market.
Benefits of Implementing DFM Early
The early integration of Design for Manufacturing (DFM) principles into the product development lifecycle yields transformative advantages for engineering efficiency, production performance, and organizational competitiveness.
When manufacturers apply DFM proactively—during the conceptual and preliminary design phases—they position themselves to unlock significant technical, economic, and strategic benefits.
Below are the key advantages of adopting DFM early in CNC machining projects:
Accelerated Time-to-Market
By identifying and resolving manufacturing challenges at the design stage, DFM eliminates time-consuming design revisions, rework loops, and downstream engineering changes.
This results in faster design validation, reduced prototyping iterations, and more efficient transition from concept to production—ensuring products reach the market ahead of competitors.
Cost Reduction Across the Product Lifecycle
Early DFM enables cost-conscious design decisions by aligning geometric complexity, tolerances, material selection, and tooling requirements with the capabilities of CNC machining.
This proactive alignment minimizes non-recurring engineering costs, reduces scrap and rework rates, optimizes cycle times, and prevents expensive late-stage modifications.
Improved Product Quality and Consistency
DFM promotes designs that are inherently more stable, easier to manufacture, and less prone to variation.
By incorporating features that support robust fixturing, tool access, and inspection, early DFM helps ensure dimensional accuracy, surface finish integrity, and process repeatability—leading to higher product quality and customer satisfaction.
Enhanced Cross-Functional Collaboration
Implementing DFM early fosters synergy between design engineers, manufacturing teams, quality assurance, and supply chain partners.
This collaborative mindset bridges the gap between design intent and production realities, encouraging shared ownership of manufacturability goals and ensuring a more unified approach to problem-solving and innovation.
Risk Mitigation and Fewer Production Surprises
Designs created without DFM insights are more likely to encounter unforeseen manufacturability issues during prototyping or production ramp-up.
Early DFM significantly reduces such risks by anticipating challenges related to material behavior, machining strategy, and tolerance accumulation—providing a more predictable and controlled development process.
Greater Design Freedom through Informed Constraints
Paradoxically, applying DFM constraints early can expand creative possibilities.
When designers understand the capabilities and limitations of CNC machining technologies from the start, they are empowered to innovate within realistic boundaries, achieving complex geometries and functionalities without compromising feasibility or cost.
Sustainable and Scalable Manufacturing
Early-stage DFM supports sustainability goals by reducing waste, energy consumption, and over-engineering.
It also lays the groundwork for scalable production by ensuring that designs are suitable not only for prototypes but also for high-volume, cost-efficient CNC machining.
Early DFM is not merely a set of guidelines—it is a strategic enabler of speed, quality, and profitability. It transforms product development from a reactive, correction-heavy process into a proactive, value-driven discipline.
Organizations that embed DFM from the outset position themselves to lead in innovation, agility, and long-term manufacturing excellence.
Conclusion: DFM as a CNC Success Strategy
In today’s highly competitive manufacturing landscape, Design for Manufacturing (DFM) is no longer a supplementary practice—it is a strategic imperative.
For CNC machining in particular, where precision, efficiency, and scalability define success, DFM serves as the foundational pillar that connects engineering vision with production reality.
By embedding DFM principles early and consistently throughout the product development lifecycle, manufacturers gain a decisive edge.
This approach transcends mere cost-saving; it drives intelligent design, optimizes material utilization, reduces lead times, and ensures that each part is not only functional but also manufacturable at scale.
A successful CNC machining strategy is not defined solely by the capabilities of the machine tools or the expertise of machinists—it is defined by how thoughtfully and practically a part is designed.
DFM transforms complexity into clarity, risk into resilience, and constraints into opportunities for innovation.
It fosters a culture where designers and engineers think like manufacturers, enabling proactive problem-solving, robust product development, and seamless transitions from prototype to production.
Moreover, DFM fosters collaborative engineering, encouraging ongoing dialogue between design, manufacturing, quality, and procurement teams.
This holistic mindset leads to better decision-making, fewer engineering changes, and a streamlined path to market-ready parts.
In conclusion, adopting DFM as a core CNC machining strategy empowers organizations to:
- Build better parts, faster and more affordably
- Eliminate inefficiencies before they reach the shop floor
- Maximize quality, repeatability, and customer satisfaction
- Scale production with confidence and control
DFM is not just a technical methodology—it is a philosophy of design excellence.
When embraced fully, it transforms the CNC machining process into a competitive advantage that delivers long-term value across the entire manufacturing ecosystem.
FAQ
What is Design for Manufacturing (DFM) in CNC machining?
Design for Manufacturing (DFM) in CNC machining is the practice of optimizing product designs to align with machining capabilities, reduce complexity, improve efficiency, and lower production costs—without compromising performance or quality.
Why is implementing DFM early important for CNC machining projects?
Early implementation of DFM helps eliminate design flaws, reduce prototyping iterations, accelerate time-to-market, and lower costs by resolving manufacturability issues before they impact production.
How does challenging the initial design improve manufacturability?
Challenging the initial design involves reviewing dimensions, tolerances, and features to eliminate unnecessary complexity. It enables engineers to simplify parts, reduce machining steps, and optimize production without sacrificing functionality.
What are the five pillars of effective DFM in CNC machining?
The five pillars include:
Process Optimization
Design for Manufacturability
Material Selection and Utilization
Environmental and Functional Considerations
Compliance, Testing, and Quality Assurance
Together, these ensure designs are practical, cost-effective, and production-ready.
How does material selection affect CNC machinability and cost?
Choosing machinable materials like aluminum or brass reduces tool wear and cycle time. Conversely, hard-to-machine materials like titanium increase machining difficulty and cost, making material choice a critical DFM consideration.
What role do tolerances play in CNC Design for Manufacturing?
Tight tolerances increase machining time and cost. DFM ensures tolerances are applied only where functionally necessary, balancing part performance with manufacturability and inspection ease.
How does fixturing impact the success of CNC machining design?
Designs that support stable fixturing reduce setup complexity, ensure dimensional accuracy, and improve part quality. DFM encourages incorporating features that simplify workholding and minimize repositioning.
What are the challenges of DFM in CNC machining?
Common DFM challenges include managing tight tolerances, machining complex geometries, selecting suitable materials, and ensuring supply chain agility—all while maintaining design intent and manufacturability.
How can designers optimize CNC tool paths and accessibility?
Designers should avoid deep cavities, sharp internal corners, and undercuts. Instead, DFM recommends accessible geometries, generous radii, and standard tooling paths to improve machining speed and accuracy.
What are the key benefits of applying DFM in CNC machining?
Applying DFM early leads to faster development cycles, reduced costs, better product quality, fewer design revisions, enhanced collaboration across teams, and scalable, sustainable manufacturing processes.