With the advent of the Industry 4.0 era and the deepening implementation of the intelligent manufacturing strategy, the scheduling optimization technology of CNC machine tools is particularly critical.
Its production efficiency is not only related to the cost control of enterprises, but also a key indicator of their market competitiveness.
According to authoritative statistical data forecasts, the global CNC machine tool market size is expected to increase to $ 120 billion by 2025.
In this context, this technology is particularly critical because it can significantly improve the equipment utilization rate, increasing it between 15% and 30%.
However, the scheduling process of CNC machine tools involves many complex process constraints, dynamic perturbations, and multi-objective optimization problems.
These factors make it challenging for traditional scheduling methods to keep pace with the current demand for intelligent and high-efficiency production.
The purpose of this paper is to systematically sort out the research results in the field of CNC machine tool production scheduling optimization and provide an in-depth analysis of the limitations of the existing methods.
On this basis, it proposes a development direction for future research.
Background and Challenges
CNC Machine Tool Production Characteristics
(1) Process Complexity Analysis.
Some experts have noted that the production process of CNC machine tools typically involves a range of methods, including milling, drilling, and turning.
Each of these processes must strictly follow established process routes to ensure the accuracy and quality of the processing.
For example, in the machining process of aerospace parts, an average of 15-20 processes are required, and each method is critical, having a direct impact on the performance and reliability of the final product.
(2) Equipment heterogeneity analysis.
Some experts have also mentioned that in the field of CNC machine tools, there are significant differences in the spindle speed, tool capacity and other key performance indicators of different machine tools.
These differences lead to the diversity of machine tools in terms of machining efficiency and scope of application.
In the case of the DMGMORICTX450eco and the MAZAKVORTEXII, for example, there is a difference of up to 40% in the machining efficiency of these two machines.
This difference requires the production scheduling system to respond flexibly and fully utilize the optimal performance of each machine.
(3) Dynamic Perturbation Phenomenon.
In the actual production scheduling process for CNC machine tools, manufacturers frequently encounter unexpected conditions, such as the urgent insertion of orders, which can push the insertion rate up to 20% to 30%.
Additionally, equipment often fails, with failure rates reaching approximately 5% to 8%.
These dynamic disturbances impose higher requirements on the stability and executability of the scheduling plan.
They necessitate that the scheduling system be able to quickly respond and adjust to minimize the impact on the overall production schedule.
The Core Objective of Scheduling Optimization
Table 1 shows the specific indices of the core objectives of scheduling optimization and the standard values commonly used in the industry.
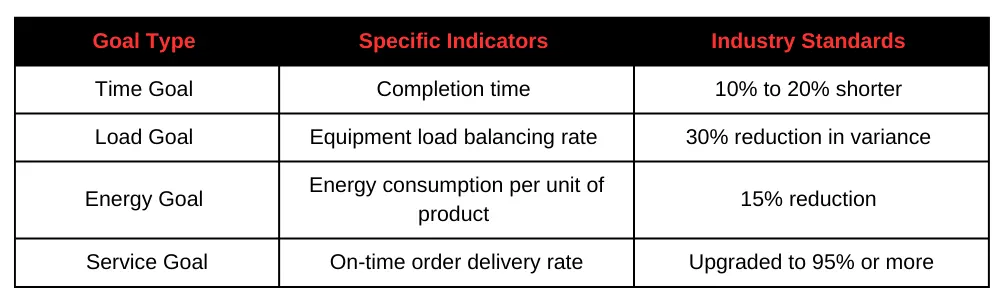
Key Challenges
Multiple conflicting objectives pose a significant challenge in contemporary manufacturing systems.
For example, the process of shortening the production cycle (MAKESPAN) may lead to an increase in energy consumption.
For example, in the SA algorithm, engineers can reduce energy consumption by 12% in single-objective optimization.
However, it increases by 8% in multi-objective optimization scenarios, suggesting that pursuing one objective may hurt other objectives.
Another major challenge is the difficulty of NP. When the number of devices exceeds 20, the time required to solve the problem using an exact algorithm can exceed 24 hours, which is unacceptable in real production.
Therefore, it is crucial to develop practical approximation algorithms or heuristics to tackle large-scale problems.
Additionally, the real-time requirement poses a significant challenge that should not be overlooked.
When facing dynamic disturbances, the system must complete rescheduling within 5-10 minutes to ensure the continuity and efficiency of production.
This requires that the scheduling system can react and adjust quickly.
Research the Status Quo
Traditional Scheduling Methods
Mathematical Planning Method
In the field of scheduling optimization, mathematical planning methods, particularly mixed-integer linear programming (MILP), play a central role.
In this study, a MILP model with the optimization objective of minimizing the total delay time is constructed, and the problem is solved by using the high-level solver CPLEX.
Intelligent Optimization Algorithms
Genetic Algorithm (GA)
Genetic Algorithm (GA) is a search and optimization algorithm that draws on the mechanisms of natural selection and genetics.
The algorithm aims to find the optimal solution to a problem by simulating the operations of selection, crossover, and mutation in the process of biological evolution.
Some experts have noted that, in practical applications, they effectively reduced the load balancing variance by introducing improvements such as adaptive crossover probability and elite retention strategy.
These improvements thus enhanced the quality of scheduling solutions.
Many practitioners widely recognize these improvements in real-world use.
For example, in the production of automobile parts, engineers applied the improved GA and successfully reduced MakeSpan from 85 hours to 75 hours, demonstrating the algorithm’s great potential in practice.
Additionally, developers can combine GA with other algorithms, such as Particle Swarm Optimization (PSO) or Deep Reinforcement Learning (DRL), to further enhance scheduling efficiency.
Optimization Using Particle Swarm Optimization (PSO)
Particle swarm optimization (PSO) is an optimization technique that draws inspiration from group intelligence.
It simulates the feeding behavior of bird flocks and utilizes the interaction and information-sharing mechanism between particles to find the optimal solution to the problem.
Some researchers have mentioned that by dynamically adjusting the weights—such as using time-varying inertia weights (linearly decreasing from 0.9 to 0.4)—PSO can significantly shorten the response time.
This also improves the stability of the scheme in dynamic order insertion scenarios.
Experimental results show that the system reduces response time by 30% and improves the stability of the scheme by 20%.
In addition, engineers can combine PSO with other intelligent algorithms, such as the Genetic Algorithm (GA) or Deep Reinforcement Learning (DRL), to further enhance the scheduling effect.
Deep Reinforcement Learning (DRL)
Deep Reinforcement Learning (DRL) combines the dual advantages of Deep Learning (DL) and Reinforcement Learning (RL), enabling it to handle complex decision-making problems.
In practice, engineers can also combine DRL with optimization algorithms, such as the Genetic Algorithm (GA) or Particle Swarm Optimization (PSO), to further improve scheduling efficiency.
Multi-objective optimization method
The improvement strategy of NSGA-II. This improvement not only enhances the algorithm’s performance but also reveals its significant advantages in practical applications.
Additionally, the introduction of fuzzy logic enhances the algorithm’s flexibility in handling uncertainty and ambiguity.
This can provide more stable and reliable optimization results in the face of complex and changing production environments.
Dynamic scheduling strategy
Based on the predictive function of the digital twin application, preventive maintenance measures can be taken 2 hours in advance, significantly reducing the frequency of unscheduled downtime.
This approach resulted in a 40% reduction in unscheduled downtime.
Additionally, the use of digital twins has enhanced the visibility of the production process.
This enables production managers to monitor the progress of production more accurately and make timely adjustments to the production plan, further optimizing the production process
Integrated Optimization Strategy
Co-optimization of processes and scheduling – This integrated optimization approach not only improves production efficiency but also reduces production costs.
Furthermore, the co-optimization strategy helps reduce material wastage and improve resource utilization efficiency.
This achieves the dual goals of enhancing production efficiency and promoting the sustainable development of the enterprise.
Limitations of existing research
Algorithm Complexity and Practicality Contradiction
Although intelligent algorithms have demonstrated excellent performance in simulation environments, they must meet real-time requirements during industrial deployment.
Taking the genetic algorithm (GA) as an example, in a scenario with 100 devices, it takes 1.2 hours for GA to converge, which significantly exceeds the 15-minute response time window allowed on the shop floor.
Therefore, striking a balance between algorithmic complexity and practicality has become a key issue in the current research field.
Researchers are exploring various approaches, including algorithm optimization, parallel computing techniques, and problem-specific heuristics.
These efforts aim to ensure algorithmic performance while reducing computation time to meet the stringent real-time requirements of industrial environments.
Insufficient Dynamic Adaptability
Currently, most existing models are constructed based on static assumptions, and the chain reaction of sudden disturbances is not sufficiently considered.
For example, equipment failures may cause delays in 3-5 subsequent processes; however, only 42% of the studies have considered dynamic compensation mechanisms.
Therefore, improving the model’s dynamic adaptability to cope with uncertainty in real production is an important direction for future research.
Researchers are also attempting to incorporate machine learning techniques to enhance the robustness and flexibility of the entire production system.
They do this by dynamically adjusting the production plan and resource allocation through real-time monitoring and prediction of various disturbances in the production process.
Tips: Robustness?
Multi-objective weight subjectivity
In the research field of multi-objective optimization, determining objective weights typically relies on the expertise of experts, which inevitably introduces a subjective factor.
For example, in the case of an automobile manufacturer, the weight assigned to the energy consumption objective is 0.3.
However, in the actual production process, due to changes in the degree of urgency of orders, the weighting was not adjusted promptly.
Therefore, the lack of an adaptive weight adjustment mechanism is a significant limitation of the existing research methodology.
To overcome this problem, experts are developing data-driven weight dynamic adjustment strategies.
These strategies aim to determine the relative importance of different objectives in various contexts using historical data, or to explore optimal weight combinations automatically through multi-objective evolutionary algorithms.
Limitations of Data-Driven Approaches
The training of deep learning models usually relies on a large amount of historical data to achieve excellent generalization performance.
However, one of the major challenges faced by SMEs is the generally small size of datasets, with the average data size usually less than 10,000 records.
This is significantly different from the 50,000+ historical work order data required for deep learning models.
This lack of data volume severely limits the scope of deep learning techniques in small and medium-sized organizations, highlighting a key limitation of data-driven approaches.
To overcome this challenge, researchers are developing lightweight deep learning models that aim to maintain high performance even under data-scarce conditions.
Meanwhile, research on advanced techniques such as migration learning and meta-learning is also underway.
The aim is to effectively transfer learning from large enterprises to small and medium-sized enterprise environments with limited data volumes.
Future Research Directions
Algorithm Fusion and Lightweighting
Algorithm fusion and lightweighting are key directions in the future research of CNC machine tool scheduling optimization.
This direction primarily explores the combination of the fast decision-making capability of Deep Reinforcement Learning (DRL) and the global search capability of Genetic Algorithms (GAs).
The aim is to develop a hierarchical optimization structure.
For example, a mechanism can be designed such that Deep Reinforcement Learning (DRL) is responsible for handling real-time perturbations of unexpected conditions in the production process.
Meanwhile, Genetic Algorithm (GA) is responsible for optimizing the global scheduling solution of the outgoing line to find the optimal solution.
This hybrid algorithmic framework not only improves scheduling efficiency but also reduces computational resource consumption while ensuring production quality.
Through algorithm fusion, complex scheduling problems can be handled more efficiently, and the demand for hardware resources can be reduced, making the scheduling system lighter and easier to deploy.
Application of Digital Twin Technology in Dynamic Scheduling
The application of digital twin technology in dynamic scheduling is an area that warrants in-depth exploration.
By constructing a digital twin model corresponding to the actual production environment, the implementation process of the scheduling plan can be simulated.
This enables the identification of potential resource conflicts and production bottlenecks in advance.
This technology is expected to reduce the cost of trial and error in real production by up to 20%.
Additionally, digital twins can be utilized to predict and optimize production processes, thereby enhancing the flexibility and responsiveness of manufacturing systems.
Through real-time data synchronization and analysis, the digital twin can provide accurate feedback on production status.
This helps decision-makers make more informed adjustments and achieve dynamic optimization of the production process.
Green Manufacturing Oriented Optimization Strategy
As global environmental awareness increases, green manufacturing-oriented optimization strategies have become a hot research topic.
In scheduling optimization, environmental impact factors such as energy consumption of machine tools and tool wear are taken into consideration to construct a low-carbon scheduling model.
In one case, carbon emissions per unit of product were reduced by 15% through optimization of energy use and material consumption in the production process.
This type of green manufacturing-oriented optimization not only helps reduce the environmental impact of the enterprise but also enhances the enterprise’s sense of social responsibility and market competitiveness.
It further promotes sustainable development and ensures compliance with increasingly stringent environmental regulations.
Research on a human-machine cooperative scheduling system
The research on human-machine cooperative scheduling systems focuses on enhancing the interpretability and efficiency of scheduling programs.
It also explores how to integrate expert experience with artificial intelligence-driven decision-making.
By constructing a knowledge graph, developers can transform the knowledge and experience of experts into computable rules, enabling the automatic generation of scheduling rules.
This method not only reduces the time experts spend on manual intervention but also improves scheduling accuracy and reliability. It is expected to reduce manual intervention time by 50%.
Additionally, the human-machine cooperative system continually optimizes the scheduling strategy through learning and adaptation, thereby achieving intelligent production management.
Edge Computing and Distributed Optimization
The application of edge computing in scheduling optimization, particularly in the design of decentralized architectures, is another direction worth exploring.
By dividing and assigning scheduling tasks to edge devices, engineers can effectively reduce the load on the central server, thereby improving the system’s response speed and reliability.
Tests show that the response time can be shortened from 30 seconds to 5 seconds, significantly improving the performance of the scheduling system.
The combination of edge computing and distributed optimization provides a novel technical approach to achieving fast and flexible scheduling.
By leveraging the proximity of edge devices, developers can reduce data transmission latency while enhancing the system’s robustness and scalability.
Conclusion
This review systematically analyzes the current research status of CNC machine tool scheduling optimization and highlights the shortcomings of existing methods in terms of dynamics, real-time capabilities, and multi-objective collaboration.
Future research should focus on breakthroughs in algorithm lightweighting, digital twin integration, and green manufacturing-oriented optimization strategies.
These efforts aim to promote the development of scheduling systems that are more adaptable and sustainable.
The research results can provide theoretical support and practical guidance for the digital transformation of intelligent manufacturing workshops.
This, in turn, helps the manufacturing industry achieve a more efficient and environmentally friendly production mode.
FAQ
Why is scheduling optimization crucial in CNC machine tool operations during Industry 4.0?
Scheduling optimization significantly improves equipment utilization (by 15–30%), controls production costs, and enhances a company's market competitiveness in the era of intelligent manufacturing.
What challenges make CNC scheduling optimization complex?
Key challenges include process complexity, equipment heterogeneity, frequent dynamic disturbances (e.g., urgent orders and equipment failure), and conflicting multi-objective requirements such as minimizing makespan while reducing energy consumption.
How does equipment heterogeneity affect scheduling decisions?
Differences in spindle speed, tool capacity, and machining efficiency across CNC machines require intelligent scheduling systems to allocate tasks based on each machine’s strengths to maximize efficiency.
What role do intelligent optimization algorithms play in CNC scheduling?
Algorithms like Genetic Algorithms (GA), Particle Swarm Optimization (PSO), and Deep Reinforcement Learning (DRL) are used to enhance scheduling efficiency, responsiveness to disturbances, and reduce production time and costs.
How can digital twin technology improve dynamic CNC scheduling?
Digital twins simulate real production environments, allowing early detection of bottlenecks, enabling predictive maintenance, and reducing unplanned downtime by up to 40%.
What limitations exist in current scheduling optimization research?
Current limitations include poor dynamic adaptability, high algorithmic complexity, subjective weight assignment in multi-objective optimization, and insufficient training data for deep learning in SMEs.
What is the benefit of combining DRL and GA in scheduling optimization?
Fusing DRL for fast response to real-time disturbances and GA for global scheduling optimization enables a balanced, efficient, and lightweight solution suitable for complex shop floor conditions.
How does green manufacturing influence scheduling optimization strategies?
Scheduling models now consider energy usage and environmental impact, helping manufacturers reduce carbon emissions and align with sustainability goals—cutting product-level carbon emissions by up to 15%.
What is the human-machine cooperative scheduling system?
This system integrates expert knowledge via knowledge graphs and AI to automate and refine scheduling decisions, reducing manual intervention time by 50% and improving decision transparency and accuracy.
Why is edge computing relevant in CNC scheduling systems?
Edge computing allows decentralized processing, reducing server load and latency. Tests show response time can be reduced from 30 seconds to 5 seconds, enabling faster and more scalable scheduling.