With the advancement of time and the development of science and technology, micro-holes with diameters of less than 1 mm have become increasingly common in our daily lives.
These micro-holes are now widely visible in various areas, ranging from cutting-edge components in aviation, aerospace, and the military to everyday items.
You can find them in circuit boards, spinnerets, models, injector nozzles, molds, medical and health devices, clocks, and many other civilian parts.
Micro-holes play a vital role in modern technology and manufacturing, and they exist almost everywhere.
On the other hand, micro-hole machining is one of the most difficult machining processes in hole machining.
First of all, because the hole diameter is minimal, micro-hole machining is almost entirely for deep holes with a large length-to-diameter ratio.
Secondly, the need to process small holes in the parts material is generally more pronounced for high-strength and high-hardness, difficult-to-machine materials, such as heat-resistant steel, stainless steel, cemented carbide, ceramics, and diamond, among others.
To address the technical challenges of micro-small hole machining, researchers are continually refining traditional machining methods while also exploring new machining techniques.
Currently, there are approximately 50 types of small-hole processing methods.
According to the different principles of processing methods, micro-hole processing methods can be divided into two categories:
That is, mechanical processing methods and special processing methods. Mechanical machining methods include drilling, punching, and grinding, while special machining methods encompass EDM, ultrasonic machining, laser machining, electrolysis, and electron beam machining, among others.
This paper presents the current status and future trends of these two types of processing methods.
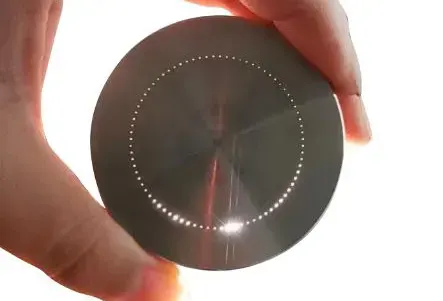
Mechanical machining of small holes
Machining methods, which use tools to remove material and achieve the desired size and shape of a part, have a long history of traditional processing methods and are widely used in various industrial areas.
In the field of microscopic hole machining, the commonly used machining method is drilling.
Drilling has high productivity, not subject to the material conductivity limitations.
The processing of micro-holes with a large aspect ratio, surface quality, and high machining accuracy is a means of economy, precision, and efficiency, resulting in superior processing.
In the electronics, precision machinery, instrumentation, and other industries, there is still much attention.
However, the following problems still exist in the drilling of small holes:
Manufacturing and Performance Challenges of Small-Diameter Drills
Due to the tiny diameter of the drill, its manufacture becomes more and more difficult.
Due to the reduction in drill diameter, its stiffness and strength are significantly reduced, making it prone to break under the action of cutting forces or machine vibrations.
Challenges in Deep Hole Drilling: Chip Removal and Heat Dissipation Issues
Small chip space, especially when processing deep holes, chips are difficult to discharge, which leads to damage to the drill.
At the same time, due to the difficulty of heat dissipation in the machining area, the drill bit’s temperature is high, and its service life is consequently reduced.
High-Speed Requirements and Precision Demands in Deep Small Hole Drilling
In deep small hole drilling, to obtain a certain cutting speed, it is necessary to use a very high speed, generally required to be in the 10,000r/min, more than, and require the spindle rotary error is very small.
Processing higher-hardness materials is more challenging.
To address the technical challenges of drilling small holes, improvements can be made in the processing machinery, process methods, tools, and other aspects.
In terms of processing machinery, the development of high-speed motors and electric spindles has significantly improved micro-hole drilling performance.
These advancements have continuously increased the spindle speed of micro-hole drilling machines.
For example, companies such as the Swiss-based Fischer and France’s Forest-Liné have developed electric spindles that reach speeds of up to 180,000 rpm.
With the use of new commercialized electric spindle components and more advanced feed mechanisms, you can manufacture smaller, more efficient micro-hole drilling and machining equipment.
Additionally, with the emergence of air-floating bearings, magnetic floating bearings, and other technologies, spindle rotary accuracy has been further enhanced.
For example, the precision spindle produced by NSK in Japan can achieve a rotary accuracy of 2μm.
To prevent the drill bit from breaking and to improve its lifespan and drilling accuracy, operators often use drill bushings or guide holes. They also perform step-by-step drilling during the process.
The optimization of cutting parameters such as cutting speed, feed, and cooling conditions is also an essential direction of current research.
In terms of tooling, advances in tool geometry, new materials, and coating technologies have significantly improved both the lifespan and performance of drills used in micro-hole machining. Manufacturers have also continued to reduce the diameter of commercialized drills.
For example, Japan’s Sumitomo Electric introduced MDSS-type cemented carbide drills with a minimum diameter of just Φ30 μm and a maximum machining depth of 2D = 60 μm.
In addition, the company produces Φ0.2 mm carbide drills for even more demanding applications.
The company also produces a Φ0.2mm, carbide drill, the maximum machining depth of 10D = 2mm.
In addition to drilling methods for processing small holes, other micro-hole machining methods, such as punching and grinding, also play a significant role in specific areas.
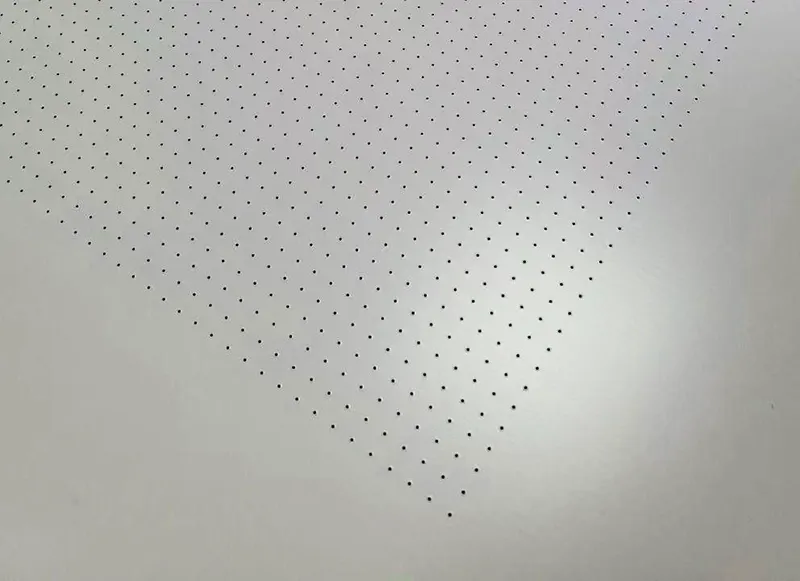
Special machining methods for processing small holes
Special processing technology uses various forms of energy to achieve material removal.
These forms include electrical energy, thermal energy, acoustic energy, light energy, electrochemical energy, chemical energy, and special mechanical energy.
Engineers also combine these energies in different ways to enhance the effectiveness of the processing methods.
Engineers commonly use several special processing methods for micro-hole machining.
These methods include laser processing, electrical discharge machining (EDM), ultrasonic processing, and electrolytic processing.
They also apply techniques such as electron beam processing, photo-porous technology, and plasma etching to achieve precise results.
Laser processing
Laser perforation mainly by photothermal ablation and photochemical ablation.
Photothermal ablation occurs when the material absorbs high-energy laser energy. The material quickly heats to its melting point and then evaporates, forming a hole.
Photochemical ablation uses laser wavelengths below 400nm. These high-energy photons break the long molecular chains of organic materials into smaller particles.
Since these particles carry more energy than the original molecules, they can escape easily. Strong suction from the external environment helps pull these particles away from the substrate.
The process quickly removes the material, forming small holes on the surface.
Compared to drilling, laser drilling offers higher resolution. Laser processing is characterized by:
- High-Speed, Efficient Hole Punching for All Materials
Independent of the material’s hardness, it can punch holes in almost all materials with high speed, efficiency, and a small heat-affected zone.
- Advantages and Key Factors of Laser Hole Processing
Laser processing does not cause tool loss or related issues. The size of the processed hole mainly depends on several factors:
the laser’s wavelength, energy density, laser type, and the thickness of the workpiece.
Since the workpiece experiences almost no macroscopic force, it remains unaffected by deformation during processing. This makes it easy to create holes in the workpiece.
Manufacturers can also easily achieve automated and continuous operation with this method.
- Precision Deep Micro-Hole Processing with High Aspect Ratio
Can process fine and deep small holes, with a small hole diameter as small as Φ4~Φ5μm and a length-to-diameter ratio of 20:1 or more.
- Common Issues in Hole Processing: Roughness, Roundness, and Precision
The roughness of the processed hole is large, the roundness is not good, it is easy to form a flare, and the precision of the hole is generally low.
- Limitations of Laser Punching for Small Holes
Affected by the output power and focusing, generally only suitable for processing small holes in a thin plate. In addition, due to the more expensive equipment for laser punching small holes, limiting its application.
To address the technical challenges of laser processing, numerous companies specializing in research have developed specialized laser processing centers that are more practical.
For example, Germany’s Demagi (DMG) DML, series of laser processing centers, the peak output power of the laser beam up to 10 ~ 20kW, the surface roughness of the parts up to Ra = 1μm, the additional control axis to solve the laser processing of similar to the pulling mold inclination tilt problem.
With this laser processing center, the most minor diameter of Φ5μm can be processed, and the depth of 20mm, micro-miniature holes.
Laser micro-hole processing technology is maturing and is considered the most promising technology for micro-hole processing.
Currently, in the United States, Japan, Germany, and other countries with more advanced electronic technology, laser micro-hole processing has become increasingly prevalent.
EDM
Electrical discharge machining is a method that directly utilizes electrical energy for processing.
During machining, the tool and workpiece generate a constant pulse spark discharge. The local high temperature of the metal causes this discharge, which removes corrosion.
There are two methods of EDM small hole machining, namely, EDM perforation and high-speed EDM small hole machining.
EDM can produce a variety of hole shapes, which are difficult to compare with drilling, laser, and other processing methods.
Moreover, there is almost no cutting force during machining, and the requirements for tool strength and rigidity are low; therefore, tiny holes (≤ Φ10 μm) can be machined.
However, there are serious drawbacks to EDM micro-hole machining.
Firstly, the accuracy and surface quality of the holes machined by this method are poor.
Secondly, only conductive materials can be processed; non-conductive, insulating materials (e.g., PCB boards) cannot be used.
Additionally, the preparation of the electrode is challenging, and its processing efficiency is low, which is a significant problem hindering its widespread application.
Given these problems, the current EDM micro-hole machining has three main research directions.
Development of new electrode preparation methods.
For example, Yamazaki et al. from Japan proposed a method of processing electrodes through microscopic holes formed by the electrode itself, which can improve the processing efficiency of the electrode and enable the creation of electrodes with shaped holes.
Takahata et al. of Japan combined microfabrication EDM technology with LIGA (lithography) technology, making it possible to mass-produce microfabricated EDM. With this technology, it is possible to process Φ20 μm copper electrode arrays and Φ30-Φ32 Μm micro-hole arrays.
Enhancing Efficiency and Quality in Hole Machining
Research and other processing methods combined to form a more efficient processing method.
Such as ultrasonic EDM technology, which combines ultrasonic energy, and EDM grinding technology, which combines mechanical grinding methods.
Among them, ultrasonic EDM technology can play a good role in improving the efficiency and quality of shaped hole processing.
Research on specialized EDM machinery.
Currently, the micro-fine EDM technology of developed countries has progressed to the stage of industrial application and even commercial sales.
For example, Japan’s Matsushita Seiki, Switzerland’s Charmilles, the United States’ McWilliams, and other companies have more mature products.
Among them, the equipment produced by Japan’s Panasonic Seiki can stably process microfine holes of Φ5μm.
Ultrasonic processing
Ultrasonic machining utilizes ultrasonic vibration tools in a liquid medium, combined with abrasive or dry abrasive materials, to produce abrasive impact, abrasive polishing, hydraulic impact, and cavitation, resulting in the removal of materials.
Or use the workpiece to generate ultrasonic vibration to make the abrasive processing method.
Through the abrasive grinding workpiece for ultrasonic machining, the cutting force and cutting heat are minimal, ensuring that the workpiece is not damaged, while maintaining high machining accuracy and surface quality.
Applications and Advantages
This ultrasonic machining method is suitable for a variety of complex and brittle materials, especially non-conductive, non-metallic, insulating materials, which can be processed.
This includes the precision machining of small holes in glass plates, as well as the processing of diamond molds with variable cross-section holes and shaped holes.
Researchers have already processed micro-holes in borosilicate glass with a diameter of about Φ180μm.
Limitations and Challenges
The disadvantages of ultrasonic machining by abrasive grinding include the complexity of tool preparation and installation, as well as the tools’ tendency to wear out, which affects the accuracy of hole machining.
The processing speed is low due to the small amplitude and low power when performing microfabrication.
Ultrasonic machining is increasingly used in conjunction with other processing methods to form a new, integrated approach.
For example, the ultrasonic EDM technology was introduced earlier.
The use of ultrasonic vibration and micro-hole drilling technology, combined with the formation of ultrasonic vibration drilling technology, is also a promising research direction.
Additionally, research on efficient and practical ultrasonic machining equipment is another major direction of development.
Recent Advances in Equipment and Research
The University of Tokyo’s Institute of Production Technology has successfully produced a micro tool, solving problems such as micro tool clamping and tool rotation accuracy, using the workpiece plus vibration working method in engineering ceramics materials.
They process these materials to create micro-holes with a smallest diameter of 5 μm.
Germany’s Demagi company (DMG) exhibited the DMS35 Ultrasonic, an ultrasonic vibration processing machine tool, featuring a spindle speed of 3000-40,000 rpm, which is especially suitable for processing ceramics, glass, silicon, and other hard and brittle materials.
Compared with traditional processing methods, productivity increased by 5 times, processing surface roughness Ra <0.2μm, and can process 0.3mm precision holes.
Beijing University of Aeronautics and Astronautics has also developed a micro-hole ultrasonic vibration drilling machine that can be used for actual production.
Other processing methods
In addition to the methods described above, there are many other micro-hole processing methods.
For example, the electrolytic machining method utilizes the electrochemical principle of anodic dissolution of metals in an electrolytic solution.
This processing method utilizes the workpiece as the anode, and the cathode is a tubular or rod-shaped cathode.
The external cross-section shape of the cathode and the cross-section shape of the processing hole are similar.
Electrolytic machining of micro-holes can process any conductive material, not subject to material strength, hardness, toughness, melting point, thermal conductivity, and other restrictions.
Production efficiency is high compared to EDM, with good surface roughness, no residual stress or deformation on the processed surface, and no burrs or flying edges on the hole.
The disadvantage is that the cathode for machining micro-small holes is more complicated to manufacture, resulting in low machining accuracy and corrosion on the fixture, machine tool, and other components, which limits the broad application of electrolytic machining for micro-small holes.
Under vacuum conditions, engineers use a focused high-energy electron beam to bombard the surface of the workpiece.
This causes the material to melt and vaporize instantly, removing it through the electron beam machining method.
This method can process holes with diameters as small as ≤ Φ3 μm. It plays a vital role in the processing of microscopic holes.
Its processing characteristics are:
They can process metal or non-metallic materials with high strength, high hardness, high toughness, and high melting points.
Engineers can focus the electron beam to an excellent point. The beam’s high power density allows it to evaporate material instantaneously.
This process does not produce macro-stress or deformation.
Strong processing capacity and high productivity;
Can process shaped holes, tapered holes, and curved holes of various curvatures, etc..
Conducted in a vacuum, especially suitable for processing easily oxidized materials and semiconductor materials with extremely high purity requirements.
The disadvantage is the need for a complete set of specialized equipment and vacuum systems, which results in a higher price and certain limitations in current production applications.
Engineers use specially formulated photosensitive dielectric materials in micro-hole processing.
They first perform preprocessing steps such as etching and spray plating.
Then, they apply laser exposure technology to create holes using photo-porous technology.
Additionally, they use plasma etching technology, which leverages the plasma discharge effect to process batches of specific material workpieces.
Both methods are essential technologies for micro-hole processing.
Researchers are exploring several special processing methods. They aim to develop more practical and efficient professional equipment and processes.
These advancements will improve processing efficiency and enhance the quality of results. They will also broaden the range of applications for these technologies.
Conclusion
This paper introduces the current status of several standard micro-hole machining technologies and their future development trends.
Various technical principles and methods have unique characteristics and specific scopes of application.
Manufacturers widely utilize micro-hole drilling technology in micro-hole machining because it offers high efficiency, accuracy, and low cost.
Special processing methods, such as laser, EDM, and ultrasonic processing, rely little on the tool itself.
These methods can create shaped holes and process batches of micro-hole arrays. They work well on difficult-to-machine materials.
With breakthroughs in key technologies, manufacturers have gradually adopted these special machining methods as the primary means of processing.
In the future, the primary direction of development for micro-small hole processing will be to explore new technologies and processes that offer higher precision and efficiency.
In addition, improving existing methods or combining two or more existing processes and methods to form a new composite processing method is also a primary direction of research and development.
FAQ
Micro-hole machining refers to the process of creating holes with diameters less than 1 mm. It plays a vital role in industries like aerospace, electronics, medical devices, and precision instruments, where high accuracy and miniaturization are essential.
Micro-holes are widely used in aviation, aerospace, military, electronics, medical equipment, clocks, molds, circuit boards, spinnerets, injector nozzles, and various consumer products.
Challenges include poor chip evacuation, limited tool rigidity, high risk of drill breakage, difficulty in heat dissipation, and the need for extremely high spindle speeds with minimal rotary error.
Laser drilling uses photothermal or photochemical ablation to vaporize material. It’s fast, precise, works on nearly all materials, and doesn’t require physical tool contact—ideal for small, deep holes with high aspect ratios.
Electrical Discharge Machining (EDM) can process complex hole shapes in conductive materials without exerting cutting force. It's ideal for extremely small holes (≤ Φ10 μm), though its accuracy and surface quality may be lower.
Yes, non-metallic and non-conductive materials like glass, ceramics, and silicon can be machined using ultrasonic or laser methods, which do not rely on electrical conductivity.
Advances in tool materials (e.g., cemented carbide), geometry optimization, nano-coatings, and ultra-high-speed spindles (up to 180,000 rpm) have significantly enhanced drill life, accuracy, and reliability in micro-hole drilling.
Electron beam machining provides ultra-fine holes (as small as Φ3 μm) with high precision, minimal deformation, and is suitable for both metals and non-metals. However, it requires vacuum equipment and has higher operational costs.
Future developments will focus on hybrid processes (like ultrasonic-EDM), improved automation, better energy efficiency, and enhanced precision equipment for mass-producing complex micro-hole arrays with high consistency.