Geometric control accuracy of multi-axis linkage: the key to improving the quality of complex surface machining
In the field of modern precision manufacturing, especially in aerospace, mold making, medical equipment and other industries that require high precision in complex surface machining, traditional 3-axis CNC machine tools have gradually revealed their limitations in dealing with complex geometries.
Five-axis CNC machine tools have two additional degrees of freedom of rotation (usually A-axis and C-axis, or B-axis and C-axis), so that the tool can contact the surface of the workpiece from any direction, thus becoming one of the core equipment for high-end machining.
In this paper, we will discuss the advantages of 5-axis linkage in terms of geometric control accuracy, and how it can help manufacturing systems to achieve a higher level of surface quality and dimensional consistency.
5-axis linkage of geometric control accuracy advantages
5-axis CNC technology is the essence of its advantages in the machining process can be realized in the multi-axis synchronous motion and tool attitude of the flexible control, which not only enhances the machining efficiency, but also fundamentally improves the geometric accuracy of complex surface machining. The following points are its core embodiment:
Avoid the “vertex cutting” effect of the ball tool, improve cutting stability
In the use of ball tools for three-axis machining, when the center point of the tool is in contact with the workpiece, the cutting speed theoretically tends to zero, resulting in the so-called “vertex cutting” phenomenon.
The cutting force in this area is extremely unstable, leading to problems such as high surface roughness and rapid tool wear.
Five-axis linkage technology by adjusting the angle between the tool and the surface of the workpiece, so that the tool is always off-center to participate in cutting, so as to maintain a reasonable linear speed and cutting efficiency, significantly improving the machining stability and surface quality.
This attitude control strategy is especially suitable for free-form surfaces and complex mold cavities with high finish.
Shorten the tool extension length to enhance system rigidity and vibration resistance
In three-axis machining, in order to avoid interference, the tool often needs a longer extension length, which is very easy to cause a decline in system rigidity in the finishing stage, tool deflection, machining vibration is serious and other problems, which affects the dimensional accuracy of the parts and surface quality.
The five-axis linkage system can avoid the interference area by adjusting the rotational attitude of the spindle or workpiece, thus significantly reducing the tool overhang length.
This not only improves the rigidity of the machining process, but also effectively reduces cutting vibration and improves the machining stability and form accuracy of complex deep cavities and inclined surfaces.
One clamping to complete the overall machining, reduce the datum transfer error
Complex parts in the three-axis system usually need to be clamped several times, involving multiple datum conversion.
This operation is unavoidable, but it is very easy to cause cumulative errors, especially in the high-precision requirements, datum consistency and repositioning accuracy is difficult to ensure.
Five-axis machines with multi-directional contact machining capabilities can complete multi-face or full-form machining in a single setup, significantly reducing or even eliminating the need for multiple setups.
This not only improves the continuity and efficiency of the machining process, but also eliminates the source of datum transfer error, thus realizing higher positioning accuracy and geometric consistency, which is especially suitable for the overall machining of precision molds and blade parts.
Advanced Interpolation and Servo Control Technologies
Achieving high-precision machining in five-axis CNC systems is not solely dependent on mechanical design or structural rigidity—it also critically relies on the integration of advanced interpolation algorithms and high-performance servo control technologies.
These digital control technologies form the core of precision machining, enabling the machine to execute complex toolpaths with exceptional accuracy, speed, and stability.
NURBS and Multi-Segment Spline Interpolation for Smooth Trajectory Control
In five-axis machining, toolpaths often follow intricate, freeform surfaces, especially in industries like aerospace and mold manufacturing.
Traditional linear or circular interpolation methods can introduce “corner errors” at trajectory junctions, leading to geometric deviations and surface imperfections.
To address this, modern CNC systems employ NURBS (Non-Uniform Rational B-Splines) or multi-segment spline interpolation algorithms.
These mathematical models allow for continuous, smooth trajectory generation, ensuring the tool moves seamlessly along complex surfaces without sudden changes in direction or velocity.
This not only improves surface quality but also reduces mechanical shocks and extends machine tool lifespan.
High-Resolution Absolute Encoders for Nano-Scale Position Feedback
Precision in five-axis machining is tightly linked to the accuracy of position detection. High-resolution absolute encoders—such as optical or magnetic scales—are widely adopted to achieve nano-level displacement feedback.
These devices provide precise, real-time information about the actual position of each axis without needing homing procedures, which is especially vital for rotary axes where accuracy directly impacts tool orientation.
Optical encoders, for example, can offer resolutions down to the nanometer level, enabling ultra-fine control of movement and toolpath execution.
This is essential when dealing with tight tolerances and demanding surface finish requirements.
Full Closed-Loop Servo Control for Real-Time Error Compensation
In high-end five-axis systems, full closed-loop control architecture is implemented to maximize machining accuracy and consistency.
Unlike open-loop or semi-closed-loop systems, full closed-loop control continuously monitors both position and velocity using encoder feedback, enabling the CNC controller to correct deviations in real time.
This is particularly valuable for compensating mechanical backlash, axis misalignment, and thermal deformation—all of which can affect dimensional accuracy over long machining cycles.
By actively correcting for these factors, the system enhances both absolute positioning accuracy and repeatability, ensuring high-quality outcomes even in extended production runs or when working with materials sensitive to thermal expansion.
Advanced interpolation and servo control technologies are indispensable to the success of five-axis machining.
The synergy between smooth trajectory planning, high-resolution feedback, and real-time closed-loop compensation ensures that five-axis CNC machines can meet the stringent demands of modern precision manufacturing—enabling complex geometries to be produced with exceptional accuracy, reliability, and surface integrity.
Precision-Oriented Mechanical Structure Design
Achieving ultra-high machining accuracy in five-axis CNC machines requires not only sophisticated control algorithms and interpolation techniques, but also an exceptionally well-engineered mechanical structure.
Structural integrity, dynamic stiffness, and real-time error compensation are foundational pillars that ensure long-term precision, thermal stability, and responsiveness in multi-axis machining.
This section delves into the critical aspects of mechanical design that enable five-axis systems to meet the demands of modern precision manufacturing.
Dynamic and Static Stiffness Optimization
In high-precision five-axis CNC machines, structural stiffness is paramount. Any deflection under cutting loads or dynamic motion introduces geometric errors that are difficult to eliminate through control alone.
To address this, leading machine tool builders focus on integrated mechanical design strategies that enhance both static and dynamic rigidity:
High-Rigidity Columns and Beds: The core machine base and vertical columns are constructed from high-grade cast iron or polymer concrete, optimized through finite element analysis (FEA) to suppress deformation and vibration during rapid multi-axis movement and heavy-duty cutting.
Dual-Drive Structures: In rotary or linear axes with large span or mass (such as gantry-type machines), dual-synchronous drive systems are employed to eliminate torque imbalance and improve axis symmetry and response during high-speed interpolation.
Roller-Type or Hydrostatic Guideways: Instead of conventional ball-type guides, many five-axis machines use roller linear guides for higher load-bearing capacity and stiffness, or hydrostatic guideways for near-zero friction, sub-micron positioning resolution, and vibration damping.
These components contribute directly to smoother motion, higher repeatability, and improved surface integrity.
Multi-Axis Error Modeling and Compensation
Due to the kinematic complexity of five-axis machines, geometric errors are not limited to individual linear or rotary axes, but include spatial volumetric errors caused by axis misalignment, motion interpolation errors, and deflection under load.
To address these challenges, manufacturers integrate a comprehensive error identification and compensation strategy:
Laser Interferometry: Laser interferometers are used to calibrate linear positioning errors, straightness deviations, and backlash.
These high-resolution tools allow engineers to capture nano-scale positioning discrepancies over the full travel of each axis.
Ballbar Testing: The Ballbar test, based on circular interpolation, quantifies machine dynamic errors such as squareness, reversal spikes, and backlash between axes.
It provides a rapid diagnostic overview of kinematic condition.
CapBall and Volumetric Error Mapping: Advanced spatial metrology systems like the CapBall system are used to characterize and model 3D volumetric errors across the entire work envelope.
This data is used to implement volumetric compensation algorithms within the CNC controller, effectively correcting spatial errors in real time.
Through this systematic approach, five-axis machines can maintain micron-level accuracy across a broad range of tool orientations and workpiece geometries.
> Diagrammatic Explanation: Sources of Spatial Error and Compensation Principles
In a five-axis CNC machine, spatial errors mainly originate from:
- Non-orthogonality or misalignment between axes (geometric errors)
- Pitch errors, backlash (positional errors)
- Thermal deformation drift
- Assembly and kinematic linkage deviations
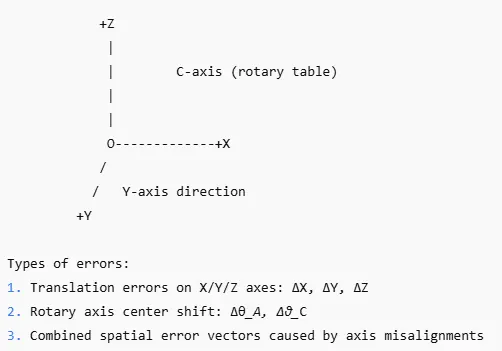
The deviation between the theoretical position and the actual position at any point P in space is expressed as a 3D vector ΔP\Delta PΔP, which results from the combined influence of these error sources.
> Mathematical Modeling of Volumetric Error
General Representation of Spatial Error:
Let the theoretical point be Pideal, actual point be Pactual, then the volumetric error vector is:

We model it as a function of several types of errors:

Linear Axis Error Model (Example: X-axis)
Each linear axis introduces six geometric errors (ISO 230-1 standard):
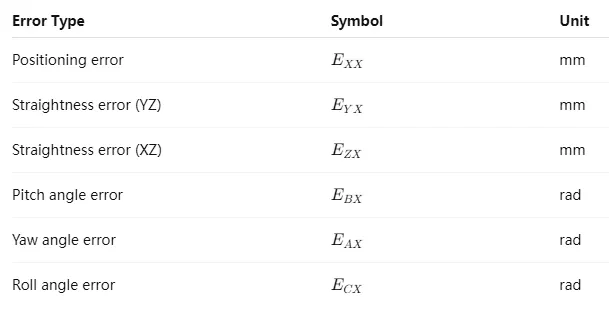
When the machine moves along X by a distance xxx, the induced error vector is:
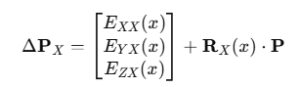
Here RX(x) represents a small-angle rotation matrix caused by angular errors (approximated to first order).
Multi-Axis Volumetric Error Accumulation Model
When multiple axes move simultaneously, the total error is a summation of transformed error vectors and angular deviations:

Where:
ΔPi: linear translation error on axis i
Ri: transformation matrix of the previous axes
Δθ: small rotation vector error for rotary axis i
ri: vector from rotary center to the tool tip or measurement point
Error Modeling Instruments and Data Acquisition
Modern 5-axis machines use high-precision equipment to measure and model these errors:
Laser Interferometers: measure axis positioning accuracy
Ballbar: assess circular interpolation error to infer geometric error
CapBall system: direct 3D measurement of volumetric error
Mapping Software (e.g., VEC mapping tools): generate compensation tables or mathematical models
Methods for Volumetric Error Compensation
There are two mainstream approaches:
Lookup Table-Based Compensation:
Create a volumetric error grid across the workspace
During machining, the CNC system interpolates compensation vectors from this grid
Model-Based Real-Time Compensation:
Use mathematical models to compute compensation dynamically based on current machine position
Better suited for high-speed multi-axis machining with high responsiveness
Thermal Compensation Mechanisms
Thermal distortion is one of the most significant—and often underestimated—sources of machining error, especially during long machining cycles or when processing materials that generate substantial heat.
Even slight temperature gradients across a spindle, ball screw, or machine frame can cause dimensional drift that undermines precision. To mitigate this:
Integrated Thermal Sensors: Temperature sensors are strategically placed throughout the machine—on spindles, drive motors, ball screws, and even within the machine frame—to monitor real-time thermal conditions.
Thermal Field Modeling: Using empirical and predictive modeling, a temperature distribution map of the machine is created, correlating thermal data to physical deformation patterns.
Real-Time Thermal Drift Compensation: Based on the thermal model, the control system continuously applies correction values to axis positions, effectively neutralizing thermally-induced errors before they affect the final part geometry.
In advanced systems, this compensation is fully automated and adaptive, allowing five-axis CNC machines to maintain stable dimensional accuracy even under fluctuating thermal loads.
Precision in five-axis machining is the result of holistic design—mechanical structure, measurement systems, and thermal management all play indispensable roles.
A machine with superior dynamic rigidity, volumetric compensation capability, and thermal stability can consistently produce complex parts with sub-micron tolerances.
As industries continue to push the boundaries of precision, the mechanical design of five-axis systems must evolve in parallel—engineered not only to move accurately, but to correct and adapt in real time.
Dynamic Response and Toolpath Optimization Algorithms in Five-Axis High-Speed Machining
In high-speed five-axis CNC machining, maintaining geometric accuracy and surface integrity while achieving high productivity is a fundamental challenge.
Unlike conventional machining, five-axis operations involve complex, continuously changing tool orientations and multi-axis kinematic coordination, which impose demanding requirements on the control system’s dynamic response.
Therefore, toolpath optimization, feedrate regulation, and adaptive control algorithms are essential to ensure machining precision under dynamic conditions.
This section explores the critical control technologies and algorithmic strategies that enable five-axis machines to deliver high precision during high-speed interpolation.
Look-Ahead Control: Predictive Feedrate Adjustment for Corner and Curvature Changes
At high speeds, abrupt changes in toolpath direction—such as sharp corners, tight curvature transitions, or complex 3D contours—can result in sudden deceleration or acceleration.
Without intelligent control, these transitions can cause tool deflection, positioning overshoot, or even part surface gouging.
To mitigate this, modern CNC controllers employ Look-Ahead (or Preview) Control algorithms, which analyze the upcoming toolpath segments in advance during the interpolation process. These algorithms:
Detect sharp path discontinuities or curvature changes.
Calculate the required deceleration and acceleration profiles before reaching critical points.
Smoothly adjust feedrates and axis synchronization to maintain stable kinematics and consistent chip load.
For five-axis machining, where tool orientation also shifts dynamically, look-ahead control ensures coordinated motion across all linear and rotary axes, reducing trajectory lag and preserving contour accuracy.
Acceleration Limiting and Vibration Suppression Algorithms
High-speed axis motion inherently introduces inertial forces, which, if not properly controlled, can lead to overshoot, oscillations, and residual vibrations—especially at trajectory junctions or during abrupt posture changes.
To address this, high-end CNC systems incorporate:
Acceleration and Jerk Limiting: By bounding the maximum allowable acceleration and its rate of change (jerk), the system smooths motion transitions, minimizes inertial shock, and avoids mechanical excitation of the machine structure.
Vibration Suppression Algorithms: These algorithms detect system resonance modes and use notch filters or model-based damping techniques to suppress excitation frequencies, especially in flexible or lightweight components such as rotary tables or long tool extensions.
The net effect is greater trajectory stability, improved dimensional consistency, and longer service life of both mechanical components and cutting tools—critical for applications such as turbine blade milling, freeform mold finishing, and high aspect-ratio feature machining.
Real-Time Monitoring and Adaptive Control Systems
To further enhance process stability and respond to real-world cutting dynamics, five-axis systems are increasingly equipped with adaptive and self-learning control frameworks.
These systems monitor machining conditions in real time and actively adjust control parameters to maintain optimal performance. Key technologies include:
Adaptive Control (AC): By monitoring spindle load, cutting forces, vibration, or torque feedback, AC systems can dynamically regulate feedrate to match the actual cutting load.
This is especially useful in heterogeneous materials or variable-thickness geometries where constant feedrate would cause tool overload or chatter.
Self-Learning Systems: Modern intelligent controllers integrate machine learning algorithms that analyze past cycle data to optimize future toolpaths.
Over time, the system develops a better understanding of machine-specific dynamic behavior, thermal drift patterns, and optimal cutting conditions, enabling predictive correction and path refinement.
Real-Time Machining Diagnostics: Integrated sensors and software modules track tool wear, spindle conditions, and servo motor performance, feeding data into the control loop for predictive maintenance and process reliability.
These adaptive systems not only protect tools and reduce cycle times but also ensure consistent part quality across extended production runs and complex geometries.
The pursuit of accuracy in high-speed five-axis machining is inseparable from sophisticated control strategies that account for the machine’s dynamic limitations.
From predictive trajectory smoothing through look-ahead algorithms to real-time adaptive control based on sensor feedback, every layer of control contributes to the overall machining quality and reliability.
As five-axis applications expand into increasingly complex and high-value components, mastery of these path optimization and dynamic response technologies becomes essential for advanced manufacturers seeking competitive precision and throughput.
Integration of Probing and In-Process Inspection Systems in Five-Axis Machining
As five-axis CNC machining continues to push the boundaries of geometric complexity and dimensional precision, the integration of on-machine probing and in-process inspection systems has become a pivotal component of intelligent manufacturing.
These systems not only enhance closed-loop control, but also support real-time quality assurance, tool wear compensation, and thermal drift correction—critical capabilities for industries such as aerospace, medical, and high-end mold manufacturing.
This section explores the role of probing systems—both trigger-type and scanning-type—in improving process stability, dimensional accuracy, and overall manufacturing efficiency within a five-axis machining environment.
High-Precision Probing for On-Machine Measurement and Automatic Coordinate Calibration
Modern five-axis machining centers are equipped with touch-trigger probes or scanning probes, typically mounted directly on the spindle or tool turret.
These probes allow for automated part referencing, feature inspection, and work coordinate system (WCS) alignment without removing the part from the machine.
Touch-Trigger Probes (e.g., Renishaw OMP series): Ideal for rapid, discrete point measurements such as hole positions, surface locations, or edge detection.
These are commonly used for initial part alignment or in-process dimensional checks during critical machining stages.
Scanning Probes (e.g., Renishaw REVO or Hexagon HP-S): Capable of collecting continuous surface data across complex contours, scanning probes are particularly useful for freeform aerospace components such as turbine blades, impellers, and aerodynamic skins.
They allow for dense point cloud acquisition and detailed surface deviation analysis directly on the machine.
By automating the establishment and verification of coordinate systems, probing systems eliminate manual setup errors, reduce machine downtime, and improve the repeatability of complex multi-face machining.
Closed-Loop Correction via Automated Feedback Control
Integrating in-machine inspection into the machining cycle transforms the process from open-loop to closed-loop manufacturing, where measurement data is used to dynamically correct machining errors.
Key capabilities include:
Real-Time Geometry Correction: If the system detects deviations from nominal geometry—such as positional drift, tilt, or undersized features—the controller can automatically trigger toolpath offsets or corrective finishing passes, reducing the need for rework or manual inspection.
Coordinate System Recalibration: After a tool change or thermal shift, probing can be used to re-establish precise part orientation, ensuring downstream operations remain within tolerance.
Machine Learning Integration: Advanced implementations integrate measurement data into adaptive control algorithms, gradually refining machining strategies based on accumulated deviation trends.
This closed-loop feedback architecture is especially critical in aerospace applications, where the cumulative error across large, freeform parts can otherwise exceed tolerance limits despite high initial accuracy.
Automated Tool Wear and Thermal Compensation
Tool degradation and thermal deformation are among the most persistent challenges in high-precision machining. On-machine probing systems enable proactive error mitigation through:
Tool Length and Diameter Monitoring: Probing routines can be used to measure the actual length, diameter, or wear of tools after key operations.
Deviations from nominal tool dimensions are automatically compensated within the CNC controller, ensuring consistent part geometry across batches.
Thermal Drift Detection: Temperature-induced errors, such as spindle elongation or axis distortion, can manifest as dimensional instability.
By probing known features or reference artifacts at regular intervals, the system can detect and correct for thermal-induced positional drift.
Zero-Touch Recalibration: During long production cycles or multi-operation machining of complex parts, automatic probing routines can periodically verify and recalibrate the tool and part coordinates—without human intervention.
This capability extends tool life, reduces scrap, and enhances unattended machining reliability, making it invaluable for high-mix, low-volume production as well as mass production environments.
The integration of advanced probing and on-machine inspection systems represents a critical step toward fully autonomous, intelligent five-axis machining.
By enabling real-time measurement, error feedback, and adaptive compensation, these technologies transform the CNC machine into a self-correcting, precision manufacturing platform.
For manufacturers aiming to deliver consistent quality in high-value, geometrically complex components, investing in such integrated metrology is no longer optional—it is essential.
Conclusion:
The exceptional precision of five-axis CNC machines is not merely the result of adding two additional rotary axes to a traditional three-axis platform.
Rather, it reflects a comprehensive, multidisciplinary advancement that integrates geometry-aware motion control, high-speed servo feedback, rigid structural design, intelligent error compensation, and real-time toolpath optimization.
Each subsystem contributes to the overall accuracy:
Geometric freedom allows the tool to maintain optimal cutting angles and minimize machining-induced errors.
Servo systems with high-resolution feedback loops ensure real-time axis synchronization and stability during complex interpolations.
Mechanically optimized structures, featuring high rigidity and thermal stability, reduce vibration, deflection, and environmental drift.
Advanced error modeling and compensation techniques—from volumetric calibration to thermal drift correction—address both static and dynamic inaccuracies at the machine level.
Adaptive and predictive control algorithms dynamically manage motion profiles, cutting forces, and tool wear to maintain process integrity.
This systemic, dynamic, and intelligent precision control architecture is what truly elevates five-axis machining to the level of advanced manufacturing.
It enables not only the fabrication of highly complex geometries but also ensures repeatable, high-quality output across demanding industries such as aerospace, precision mold and die, medical implants, and energy components.
In today’s era of digital transformation and smart manufacturing, five-axis CNC machines are no longer just tools—they are highly integrated, self-adaptive production platforms.
Their ability to harmonize precision, flexibility, and automation makes them indispensable in the pursuit of next-generation manufacturing excellence.
FAQ
What is geometric control accuracy in five-axis CNC machining?
Geometric control accuracy in five-axis CNC machining refers to the machine’s ability to maintain precise tool positioning and orientation across multiple axes while machining complex surfaces. It ensures consistent dimensional accuracy, high-quality surface finishes, and repeatable results for intricate components.
How does five-axis machining improve complex surface quality compared to three-axis machining?
Unlike three-axis machining, five-axis CNC allows the tool to approach the workpiece from any angle, avoiding the “vertex cutting” effect, shortening tool overhang, and reducing vibration. This results in smoother surface finishes, better dimensional control, and higher machining stability for freeform surfaces and deep cavities.
Why is tool overhang length important in precision machining?
Long tool extensions can cause reduced system rigidity, increased vibration, and tool deflection, which degrade part accuracy. Five-axis machines minimize overhang by adjusting tool orientation to avoid interference, enhancing stability and surface integrity.
How does single-setup machining in five-axis systems reduce errors?
Five-axis machining can perform multi-face and full-form machining in one setup, eliminating multiple clamping operations. This reduces datum transfer errors, improves positioning accuracy, and ensures better geometric consistency for complex parts.
What role do advanced interpolation algorithms play in five-axis machining?
Advanced algorithms like NURBS and multi-segment spline interpolation create smooth, continuous toolpaths for freeform surfaces. This eliminates “corner errors,” reduces mechanical shocks, and improves both surface quality and machine longevity.
How do high-resolution encoders improve five-axis machining precision?
High-resolution absolute encoders provide nano-scale position feedback without homing procedures. This ensures ultra-precise axis control, accurate tool orientation, and tight tolerance compliance, especially critical in aerospace and medical manufacturing.
What is volumetric error compensation and why is it important?
Volumetric error compensation corrects 3D spatial errors caused by axis misalignment, backlash, or thermal drift. Using tools like laser interferometers, Ballbar testing, and CapBall systems, manufacturers map and correct these errors in real time, maintaining micron-level accuracy.
How does thermal compensation enhance machining stability?
Thermal sensors monitor temperature changes in the spindle, ball screws, and machine frame. Real-time thermal modeling adjusts axis positions to counter thermal expansion, ensuring stable dimensional accuracy during long machining cycles.
What are look-ahead and vibration suppression algorithms in high-speed five-axis machining?
Look-ahead algorithms predict upcoming toolpath changes, adjusting feedrates for smooth transitions. Vibration suppression filters resonance frequencies, reducing tool chatter, improving surface finish, and extending machine and tool life.
How does in-process probing improve five-axis machining accuracy?
On-machine probing enables real-time measurement, coordinate recalibration, and tool wear detection. Integrated with closed-loop feedback, it allows the CNC to automatically correct machining deviations, ensuring consistent quality and reducing scrap rates.