People often refer to CNC machine tools as the “industrial mother machine” in the equipment manufacturing industry, which is the most representative of the five-axis linkage machine tools. They play a crucial role in promoting national industrial strength and accelerating the development of manufacturing power.
Representing the highest level of machine tool manufacturing, the five-axis linkage CNC machine tool system is a key measure of a country’s ability to manufacture complex and precision parts.
It also reflects the level of technology and automation in national production equipment.
An important standard of the technical level of national production equipment automation.
With the development of industry, five-axis linkage CNC machine tools have become crucial. People consider them the most important high-precision machining equipment for key components.
People use these components in aerospace, marine, military, classified instruments, high-precision medical equipment, and other areas of processing and manufacturing.
As a complex and widely used technology, five-axis linkage CNC machine tools integrate computer control, high-performance servo drive, and precision machining.
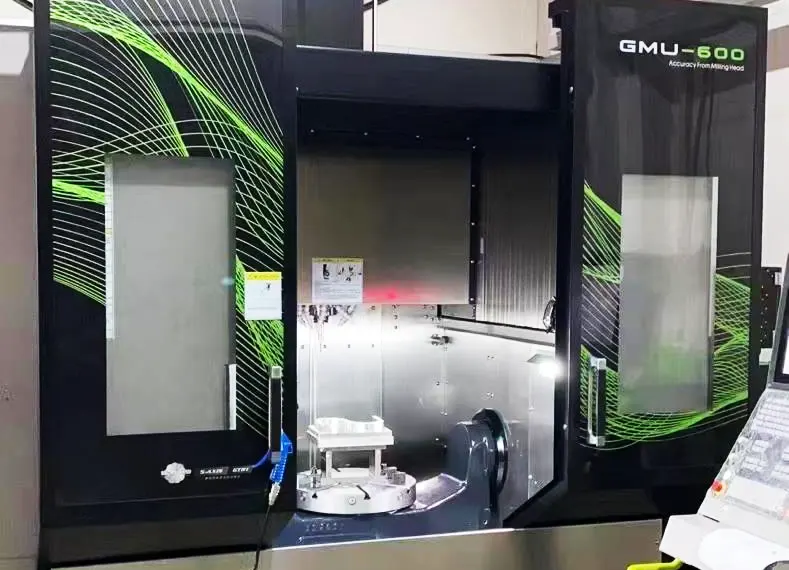
Advantages
Compared to traditional three-axis CNC machine tools, they offer irreplaceable advantages.
(1) Machines can processing complex-shaped workpieces.
Five-axis linkage CNC machine tools can process complex-shaped workpieces that three-axis CNC machine tools cannot process. The machining process can effectively avoid tool interference.
For example, in the processing of aerospace components like impellers, blades, and whole leaf disks, five-axis machine tools offer significant advantages.
They allow the use of shorter tools, which enhances the rigidity of the system. Additionally, this approach reduces the number of tools required and helps avoid the need for specialized tools.
(2) High efficiency and precision
Compared to three-axis CNC machine tools, five-axis CNC machine tools offer several advantages.
They reduce the number of clamping and datum conversions. Additionally, they minimize the number of fixtures used, significantly improving both machining efficiency and accuracy.
(3) High flexibility and integration, and complete processing capabilities
Five-axis CNC machine tools offer high flexibility, high integration, and complete processing capabilities. These features make them an excellent solution for complex part machining in fields like aerospace and automotive.
They address challenges in machining accuracy and cycle time during the new product development process. As a result, they significantly reduce the development cycle and improve the success rate of new products.
At present, five-axis linkage CNC machine tools have become the hot spot and focus of the development of high-grade CNC machine tool industry in various countries.
Five-axis linkage of the basic structure of CNC machine tools
Most of the current five-axis CNC machine tools are “3 + 2” structure, that is, X, Y, Z three linear axes of motion plus respectively around the X, Y, Z axis rotation A, B, C three rotary axes in the composition of two.
Therefore, from the general direction of classification, five-axis linkage CNC machine tools have X, Y, Z, A, B; X, Y, Z, A, C; X, Y, Z, B, C three forms.
We can divide five-axis linked CNC machine tools into three main forms based on the combination of two different rotary axes.
These forms are: the double rotary table type, the rotary table plus pendulum head type, and the double pendulum head type.
Double rotary table structure of five-axis linked CNC machine tools
The rotary table structure of this five-axis linkage machine tool is the double rotary table structure of A-axis + C-axis.
The table set on the bed rotates around the X-axis, which we define as the A-axis. The working range of the A-axis is generally 30° to 120°.
The rotary table in the center of the table can rotate around the Z-axis, defined as the C-axis, which is capable of 360° rotation.
Therefore, by combining the A-axis and C-axis, the machine can machine the workpiece fixed on the table with a vertical spindle on all five faces, except the bottom face.
Five-axis CNC machine tool with rotary table and pendulum head structure
A-axis, B-axis or C-axis can be the rotary table and pendulum head of the machine tool, so the 5-axis CNC machine tool with rotary table and pendulum head structure can realize different combinations to adapt to different machining objects.
This setup offers the advantages that the machine spindle can machine flexibly and that it can machine large and complex workpieces by enlarging the machine table.
Five-axis CNC machine with double pendulum head structure
The pendulum head structure features a loose drawknife structure for the spindle. As a result, the size of the double pendulum head itself should not be too small, typically ranging from 400 mm to 500 mm.
Additionally, the design of the five-axis CNC machine tool provides a larger machining range due to the need for a wide range of motion for the double pendulum head.
These machines are generally gantry-type or movable beam gantry-type, with the gantry width typically ranging from 2,000 mm to 3,000 mm.
Currently, the more advanced double pendulum head type five-axis linkage machine tools generally use the “zero transmission” technology in the pendulum head structure.
The application of “zero transmission” technology in the rotary axis is a key solution to address the issues of rigidity and accuracy in the transmission chain.
Five-axis linkage CNC machine tool research status quo
Currently, developed countries in Europe, the United States, and Japan lead the research of five-axis linked CNC machine tools. These countries represent the highest level of development in five-axis linked CNC machine tools today.
With technological progress and the growing social demand for high-grade CNC machine tools, the CNC technology of renowned five-axis machine tool manufacturers is evolving.
The focus is on high-speed, high-precision, intelligent, composite, high-reliability, and environmentally-friendly developments.
Germany
SycoTec applies the 4015 DC-R-HSK63 high-speed precision spindle to five-axis CNC machine tool machining centers.
This upgrade expands the machine’s machining range from the original 0–24,000 r/min to 0–100,000 r/min, enabling five-axis ultra-high-speed precision machining.
The machine equips standard HSK-63 shanks, allowing for quick, frictionless tool changes.
This feature reduces machine stopping times, increases productivity and efficiency, and broadens the machining range of the machine.
Zimmermann designed the five-axis CNC machine and equipped it with a high-end three-axis milling head of M3 ABC with a curved guideway, adding one extra B coordinate, i.e., three different rotating coordinate heads of A, B, and C.
This five-axis CNC machine features excellent rigidity and a relatively compact structure. It also includes three different coordinate heads—A, B, and C—built-in.
This design increases the deflection range and ensures that the C-axis rotation process remains unaffected by the rotation of the other axes.
As a result, the design does not restrict the rotation process of the C-axis, which improves the accuracy of 5-axis linked CNC machine tools during machining operations.
France
The France-based SOMAB (SOMAB) company manufactured the DIAM five-axis machining center, which is highly versatile.
With just one clamping, it can perform turning, milling, boring, drilling, gear machining, crankshaft machining, on-line testing, and other composite operations.
This greatly enhances both the efficiency of machine tool processing and the machining accuracy.
USA
The United States’ Hurco (Hurco) company manufactured the offset spindle type i series five-axis machining centers. These machines use an integral electric spindle and are equipped with high-precision ceramic bearings.
The machining table can continuously rotate without any angle restrictions, which reduces beat time. This design allows for maximum tool feed and delivers superb performance when contouring complex parts.
The VF-6TR multifunctional 5-axis CNC machining center from Haas provides fully synchronized 5-axis motion and can position the workpiece at virtually any angle for increased machining flexibility.
Japan
The YASDA YBM Vi40 ultra-precision 5-axis CNC machine, made by YASDA Corporation (YASDA), features a rigid body.
It has an integrated bridge structure that ensures high-precision machining and excellent surface quality. This machine is specifically designed for mold and die manufacturing.
The VARIAXIS i series of multifunctional 5-axis CNC machining centers developed by Yamazaki Mazak Corporation (Mazak) is capable of machining the complex curved surfaces of large and heavy parts in a single setup.
The series applies the Done-in-One concept, which enables all machining, from raw materials to final products, to be completed on a single machine. This greatly reduces machining time and improves machining accuracy.
South Kore
South Korea’s Hyundai WIA (HYUNDAI WIA) exhibited the high-speed, high-precision five-axis vertical machining center XF6300.
The manufacturer designed this machine with advanced mold products and high-precision machining capabilities. It features a high-performance built-in spindle that reaches 15,000 r/min.
By using high-precision, diversified spindles, the system minimizes the transmission of vibration to the axis. This enables the machine to achieve micron-level high-precision machining.
Italy
Italy’s FIDIA launched a five-axis high-speed milling vertical machining center. The high-speed spindle can reach up to 24,000 r/min, and it features an AC five-axis oscillating head.
Manufacturers mainly use this machine for high-speed five-axis milling of automotive bumpers, lamps, interior molds, plastic molds, and other similar components.
Five-axis linkage CNC machine tools in China research status quo
Although China has rapidly developed its CNC technology in recent years and has made significant progress in some advanced areas, challenges remain.
Due to China’s relatively weak industrial base and the short period of time since CNC machine tools began industrialization, there is still a noticeable gap in both technology and industry compared with developed countries.
This gap is especially pronounced in the field of high-end five-axis CNC machine tools, where the distance from the international advanced level is even greater.
This gap is specifically reflected in the high-grade CNC systems of five-axis CNC machine tools. The key functional components cannot yet be independently developed.
Compared with advanced foreign five-axis linkage CNC machine tools, there are noticeable differences in reliability, efficiency, precision retention, and level of intelligence.
However, with strong policy support and the joint efforts of enterprises, universities, and research institutions—especially under the “Made in China 2025” strategy, which identifies high-end CNC machine tools and basic manufacturing equipment as key strategic sectors—China’s development of high-grade CNC machine tools has entered a major phase of opportunity.
Significant progress has been made in advancing five-axis linkage CNC machine tools from R&D and trial stages to finalized technologies ready for mass production. As a result, China has gradually developed its own mature CNC machine tool products.
Wuhan Huazhong CNC
Ltd. has mastered many key technologies of five-axis linkage and developed five-axis CNC systems with independent intellectual property rights.
Among them, Huazhong CNC has developed the 8-type five-axis CNC system, which features an open, fully digital, and bus-type hardware and software architecture.
In this system, the bus topology—either ring or linear—connects servo drives, I/O units, or data acquisition modules through standard bus interfaces.
This allows the five-axis system to be flexibly integrated with different rotary table CNC machine tools, greatly enhancing machining efficiency.
At present, Huazhong 8 type 5-axis CNC system has been applied to AC pendulum head 5-axis gantry machining center, BC pendulum head 5-axis vertical machining center, moving beam gantry type 5-axis machining center and other 5-axis high-grade CNC machine tools.
KD CNC
The company places great importance on technological research and development, adhering to a core, independent, and controllable development strategy.
It actively undertakes China’s major special project on “high-grade CNC machine tools and basic manufacturing equipment” R&D. Its KMC800SU five-axis linkage vertical machining center has been recognized and selected for use in the military field.
Its KMC800SU five-axis vertical machining center was selected as one of the “supply catalogs of domestic high-grade CNC machine tools for military industry”.
The machine bed is made of mineral cast stone material with excellent vibration suppression and thermal deformation resistance.
It adopts the spindle movement mode with a performance index of up to 48 m/min and 0.7 g. Compared with the traditional model, it has higher material removal rate, smaller interference, stronger cutting rigidity, higher speed and accuracy.
In addition, the newly developed DMC50 dual five-axis vertical machining center by KD CNC adopts an advanced modular design concept.
Based on its core functions of milling, drilling, and tapping, it can also integrate additional composite functions such as turning, ultrasonic machining, and grinding modules.
One clamping can complete multi-process, multi-task machining, to ensure high machining accuracy and machining efficiency of precision parts.
The machine tool can be equipped with robots and silos to realize single-machine automation. At the same time, due to the compact structure of the machine tool and small width size, it is conducive to multi-group lines, which can effectively save the space occupied.
The machine is especially suitable for high efficiency and high precision machining of parts in aerospace, tooling, precision molds, medical equipment, new energy vehicles and semiconductor industries.
Shenyang Machine Tools
Shenyang Machine Tool, as a long-established backbone enterprise in China’s machine tool manufacturing industry, has rich experience and strong R&D capabilities.
As early as 2010, the company exhibited the VMC25100u vertical five-axis linked machining center, designed for machining titanium alloy aerospace structural parts.
It also introduced the GMC1230u high-speed gantry five-axis machining center with an automatically exchangeable milling head.
These developments marked a major breakthrough in China’s five-axis CNC machine tool industry at that time.
In 2020, Shenyang Machine Tool further leveraged its strengths and successfully launched China’s first high-speed five-axis machining center specifically developed for the high-speed rail industry.
This machine tool, targeting typical machining needs in the high-speed rail sector, overcame several key technological challenges. These included lightweighting of the entire machine, ultra-long stroke bed precision assurance, ultra-high-speed X-axis movement, whole-machine high-precision machining, and deformation-compensated machining.
These advancements significantly boosted the performance of high-end CNC machine tools in China and enhanced the nation’s independent innovation capabilities in this field.
Jinan No.2 Machine Tool
Jinan No.2 Machine Tool showcased the independently developed XHSV2525A×40 high-frame 5-axis high-speed boring and milling machining center.
The core functional components of this machining center utilize JIER’s proprietary AC-axis double pendulum CNC milling head.
This technology offers high precision, high efficiency, and high reliability.
It is capable of meeting the complex machining requirements of large thin-walled structural parts in China’s aerospace industry, as well as large, complex curved surfaces in the automotive mold and die industry.
Beijing Machine Tool Research Institute
At the 17th China International Machine Tool Fair, the Beijing Machine Tool Research Institute exhibited the μ1000/5ST-400V Precision Vertical 5-axis Machining Center.
This machining center is capable of processing a wide range of materials and performing multiple operations—including milling, boring, reaming, tapping, and contouring—in a single clamping.
It enables 5-face machining with high efficiency, high precision, and high reliability.
It is well-suited for machining complex precision structural components and achieving efficient, high-quality production of precision parts in key application fields across China.
Shanghai Jiao Tong University
Shanghai Jiao Tong University, in collaboration with the Shanghai Institute of Electrical Engineering, developed a large gantry-type five-axis linkage machining center.
The system features independently developed five-axis CNC control and key components for the swing axis.
This machining center is primarily used for precision machining of complex surfaces—such as marine propellers—and enables efficient path planning and process optimization.
It represents a significant advancement in large-scale five-axis CNC equipment for propeller machining and similar applications.
Shanghai Jiao Tong University also partnered with Topu CNC and other organizations to develop the first dual five-axis mirror milling technology and equipment for large aerospace surface skins and case bottoms.
This solution addresses the need for high-precision, wide-range, and multi-axis coordination in large-scale, high-end machine tools.
Key breakthroughs were achieved in dual five-axis linkage synchronization, closed-loop control of machining quality, and precision machining of ultra-thin, flexible surfaces used in aircraft and rockets.
This technology supports the R&D and mass production of China’s large aircraft and launch vehicle programs.
Tsinghua University
The Department of Mechanical Engineering at Tsinghua University and KD CNC Technology jointly established a research and development center.
Together, they lead the project titled “Domestic 5-axis High-Efficiency Precision Machining Processes and Manufacturing System for Aerospace Complex Components.”
This initiative focuses on calibration technologies for five-axis machining centers and online measurement systems aimed at enhancing machining accuracy and maintainability of domestically produced CNC machines.
To address the information loss in traditional CNC machining caused by the “continuous-discrete-continuous” process, the team also conducted research on CAM tool path planning, NURBS curve direct interpolation, and global time-optimal speed control for five-axis linkage.
These efforts have significantly improved machining accuracy and efficiency.
Other Universities
Nanjing University of Aeronautics and Astronautics, the University of Electronic Science and Technology, and other institutions have been involved in collaborative R&D on five-axis CNC machine tools for over a decade.
Supported by major national science and technology programs, they developed S-shaped test piece evaluation methods for five-axis machines.
They achieved breakthroughs in optimizing the machining accuracy of complex curved surfaces based on these test pieces.
This work has supported the batch production of key aircraft models in China and promoted the independent and controllable development of domestic five-axis CNC technology.
Importantly, it led to China’s first breakthrough in establishing international standards for machine tool precision testing.
Development trend and future outlook
Trend
From the above research status of five-axis linkage CNC machine tools, it is obvious to see that the development trend of five-axis linkage CNC machine tools today is:
(1) High-speed.
With the continuous development of machine tool technology, five-axis linkage high-speed CNC machine tools have made breakthroughs in their internal high-speed feed mechanisms and high-speed electric spindles.
As a result, the spindle speed of CNC machine tools and the range of feed volumes have significantly increased.
Among them, the linear motor-driven spindle speed has now reached 100,000 r/min.
The feed operation parts of the machine can achieve a rapid movement speed of 120 m/min. Additionally, the machine tool system’s cutting feed speed has reached 60 m/min.
These advancements effectively reduce processing time and auxiliary time, resulting in improved productivity.
2) Precision.
Five-axis linkage CNC machine tool machining accuracy is very high, with the development of computer-aided manufacturing (CAM) system, precision has reached the micron level.
In the processing of high-precision parts, the dimensional accuracy and shape accuracy of the parts can be guaranteed, avoiding machining errors.
3) Composite.
The five-axis linkage CNC machine tool was developed to adapt to the processing of polyhedral and curved surface parts.
With the advancement of machine tool composite technology, various composite machining centers have emerged.
These include five-axis milling and turning composite machining centers, boring, milling, and drilling composite machining centers, as well as milling, boring, drilling, and turning composite machining centers.
These machines can perform multiple machining operations simultaneously, significantly enhancing machining efficiency.
For example, when processing complex parts, milling, drilling, tapping and other operations can be carried out at the same time, thus shortening the parts processing cycle.
4) Intelligent.
With the development of artificial intelligence, big data, and the Internet of Things, CNC machine tools are rapidly advancing toward greater intelligence.
At present, the CNC machining process has achieved intelligent optimization and selection of machining parameters.
It also features adaptive control of the machining process, along with intelligent self-diagnosis and self-repair of faults. Additionally, it enables intelligent fault playback, fault simulation, and smart AC servo drives.
5) Flexibility.
Five-axis linkage CNC machine tools have strong adaptability when processing complex surfaces and other variable objects.
After a single clamping, multiple surfaces and angular processing can be realized on the workpiece.
This eliminates the need for repeated work type changes required by ordinary CNC machine tools.
It also avoids the transfer of parts between processes and the scribing of lines, ensuring a more streamlined and efficient workflow.
At present, CNC machine tools are moving towards the direction of unit and system flexibility.
Conclusion
Five-axis CNC machine tools are vital in modern manufacturing, excelling in precision and handling complex geometries across industries like aerospace and healthcare.
They surpass traditional three-axis machines by reducing clamping times and enhancing efficiency and accuracy.
Various designs, such as double rotary tables and swivel heads, offer versatility for different machining needs.
Innovations by industry leaders continue to drive advancements in speed, precision, and intelligent automation.
As demand for high-precision components grows, five-axis CNC machines will remain essential, pushing the boundaries of modern manufacturing technology.