Machinery mold is an indispensable and important part of modern industrial production, and its accuracy and quality directly affects the product performance and production efficiency.
CNC machining technology is a key technology in the modern manufacturing industry, which utilizes computers, CNC machine tools and other high-tech equipment to achieve precise processing of various shapes of materials.
This technology operates through a pre-written machining program. The computer processes the input instructions to automatically control the machining process.
It manages the movement of the coordinate axes and calculates precise positions. This, in turn, controls the machine tool’s machining operations.
The process offers high precision, high efficiency, and a high degree of automation. These advantages effectively address issues found in traditional mold manufacturing, such as long production cycles, high costs, and low precision.
Therefore, to explore the application of CNC machining technology in machinery mold manufacturing is the current hot topic.
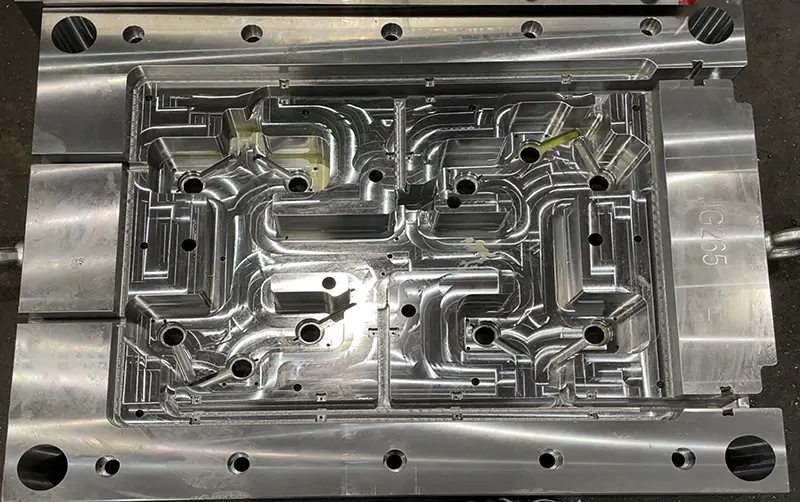
Influencing factors
Programming factors
The core of CNC machining technology lies in accurate programming. The accuracy of the programming data directly affects the accuracy and quality of the processed parts.
When processing data in the CNC machine, if inaccuracies occur, it will further lead to errors in the entire CNC machine operation process, and will also have an impact on the machining accuracy of the contour trajectory of the CNC machine.
Therefore, programmers need to have a high degree of professionalism and rich practical experience to ensure the accuracy of programming data.
In addition, programmers also need to consider the CNC margins to avoid errors that could lead to scrapping parts.
Operation factors
We should not ignore the influence of operating factors on CNC machining technology.
First of all, the skill level of the operator directly affects the processing quality.
An experienced and skilled operator can understand the programming intention more accurately and make fine adjustments according to the actual situation in order to achieve the best machining results.
Secondly, the standardization of the operation process is also crucial.
Operators need to strictly follow the operating procedures to ensure that every step of the operation is accurate.
Finally, the stability and cleanliness of the operating environment will also have an impact on processing quality.
A stable and clean operating environment can reduce external interference and improve machining accuracy.
Hardware factors
Hardware factors are another important aspect that affects CNC machining technology.
First of all, the selection and maintenance of machine tools have a direct impact on machining quality.
Different types of machine tools have different machining accuracy and efficiency, so you need to choose the machine according to the processing needs of reasonable.
At the same time, the maintenance of the machine tool is also crucial, regular inspection and repair can ensure that the machine tool is in the best working condition, improve machining accuracy and efficiency.
In addition to machine tools, the selection of tools and fixtures is also a key factor affecting the quality of machining. Tool material, hardness and wear resistance directly affect the cutting effect and machining accuracy.
Therefore, it is necessary to choose the tool according to the machining material and machining requirements.
The stability and clamping force of the fixture will also affect the machining accuracy, so you need to choose the appropriate fixture and install it correctly.
In addition, the performance and stability of the CNC system is also an important factor affecting the quality of machining.
The CNC system needs to have high-speed, high-precision control capabilities to ensure that the machine tool axes can move accurately according to the programmed instructions.
At the same time, the stability of the CNC is critical to avoid unplanned interruptions or error buildup during the machining process.
In the mechanical mold manufacturing applications
CNC programming technology
The technology is the core of CNC machining technology, which involves the design of the mold shape and data into the machine tool can recognize the instructions.
The application of this technology plays a key role in mold manufacturing.
First, programming software and language.
CNC programming usually use professional CAM (Computer Aided Manufacturing) software, such as MasterCAM, VectorCAM and so on.
These software convert CAD (computer-aided design) models into G code or M code that CNC machine tools can understand.
Second, programming steps.
The steps of CNC programming include analyzing part drawings, determining the machining process, selecting tools and cutting parameters, writing programs, and performing simulation verification.
Each step requires precise calculations and careful planning to ensure that the final machining results meet expectations.
Third, precision and efficiency.
Accurate CNC programming enables high-precision machining of mold parts.
At the same time, the optimized programming strategy can also improve processing efficiency, reduce unnecessary machine idle and tool change time.
CNC EDM technology
CNC EDM technology is an important method of CNC machining technology, especially suitable for processing hard alloys and hardened steel and other difficult-to-machine materials.
Its working principle relies on using the pulse discharge generated between the electrode and the workpiece to etch the material.
By controlling the discharge parameters and the electrode’s trajectory, it achieves precise machining of complex workpiece shapes, as shown in Fig. 1.
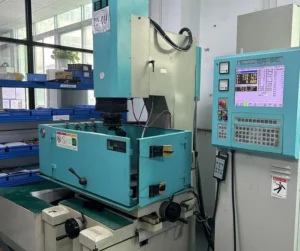
This technology offers high precision, high surface quality, and low stress.
At the same time, since the machining process requires no mechanical contact, it effectively avoids problems such as tool wear and workpiece deformation.
It is widely used in cavity machining for mold manufacturing, electrode manufacturing, fine engraving, and other fields.
It solves the problem of handling hard materials and complex shapes that are difficult to process with traditional machining.
When using CNC EDM technology for mold processing, you should follow the steps below to ensure processing quality and efficiency:
First, select the appropriate electrode material to meet the machining requirements.
Second, ensure the safety of the electrode and the workpiece to prevent machining errors through accurate and stable positioning and clamping.
You can fix the electrode with the help of tools such as jigs or magnetic suction cups.
Third, set reasonable machining parameters, including current, voltage, pulse width, pulse interval, machining speed, etc., as well as consider the effect of electrode wear.
Fourth, start the CNC machine tool and begin the machining process. Monitor the feeding speed and machining depth of the electrode to ensure the machining quality and efficiency.
Also, control the temperature and pressure during machining to prevent problems such as overheating and deformation.
In addition, pay attention to the quality of the machined surface, as it directly affects the life and precision of the mold.
Ensure that the finish and precision of the machined surface meet the requirements.
CNC milling processing technology
It relying on the basic principles of milling, the use of computer programming on the movement path of the tool for accurate control, so as to carry out fine milling of mold parts, to ensure that the processing to meet the design requirements of the shape and size, the device is shown in Figure 2.
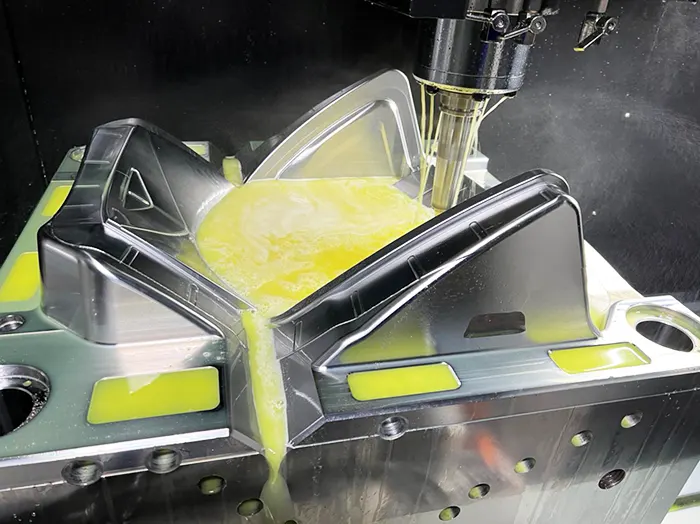
This technology has the advantages of high machining accuracy, good surface quality, high machining efficiency, applicable to a variety of complex shapes of mold parts processing, such as planar, curved surfaces, holes and threads, etc., is one of the most commonly used CNC machining methods.
Before the implementation of CNC milling, the key steps include selecting the appropriate tool to adapt to the mold material and processing needs, in order to ensure the quality and reliability of machining.
Next, the mold is properly mounted in the fixture to ensure a stable position.
After completing the necessary parameter settings and programming, start the equipment, follow the established procedures to control the tool to mill according to the predetermined path, while adjusting the rotational speed of the milling cutter and the milling speed to ensure the accuracy of the mold surface machining.
In the actual operation of CNC milling, continuous monitoring is necessary to identify and respond to any deviation or abnormality in order to maintain the quality of the process and the safety of the staff.
At the same time, the optimal milling path is planned according to the specifications of the mold to prevent any interference or collision.
Strict adherence to CNC milling machine safety practices is also essential to ensure a safe operation.
CNC turning processing technology
CNC turning processing technology is an important part of CNC machining technology, mainly used in the processing of rotary body parts.
In the mechanical mold manufacturing, CNC turning processing technology is widely used in the following three types of parts processing:
First, the processing of shaft parts.
Shaft parts are an important part of the mold, such as guide pillar, ejector rod, etc..
CNC turning machining technology can accurately process a variety of shapes of shaft parts to ensure their dimensional accuracy and shape accuracy.
Second, the processing of sleeve parts.
Sleeve parts such as bushings, guide bushings, etc., play the role of positioning and guidance in the mold.
CNC turning technology can efficiently process high-quality bushing parts, improve the precision and service life of the mold.
Third, the processing of complex rotary parts.
For some complex rotary parts, such as threads, curved surfaces, etc., CNC turning machining technology can also realize high-precision machining.
Through accurate programming and machine operation, various complex shapes of parts can be processed to meet the diverse needs of molds.
Before implementing CNC turning, the key steps include selecting the right tool to suit the material and machining requirements to improve machining efficiency and quality.
Next, ensure that the workpiece is firmly positioned during the installation process to prevent vibration and displacement during machining.
Then, set the machining parameters, such as cutting speed, feed and depth of cut, to ensure machining quality.
After initiating machining, monitor the correctness and suitability of the program to ensure the accuracy of the machining path and parameters.
At the same time, check tool wear regularly and replace them in time to maintain machining quality. Finally, adopt effective machining process and inspection methods to control the machining accuracy and ensure the precision and quality of the mold.
CNC wire cutting processing technology
CNC wire cutting processing technology relies on the principle of electric spark discharge, using a thin metal wire as the electrode, applying pulse current between the wire and the workpiece, and carrying out cutting processing through the electric spark effect.
This technology is mainly used to process holes and contours of various shapes.
In the manufacturing of mechanical molds, CNC wire cutting technology is widely used in the processing of blanking dies, extrusion dies and other molds.
Punching dies are molds used for stamping, which need to accurately process various shapes of holes and contours.
CNC wire cutting technology can precisely cut out the required shapes and sizes to ensure the precision and quality of punching dies;
Extrusion die is used for metal extrusion molding die, need to withstand greater pressure and temperature.
CNC wire cutting processing technology can process high strength, high precision extrusion die, improve its service life and molding quality.
In the implementation of CNC wire cutting, the first step is to select a suitable electrode wire to meet the processing requirements. Then, correctly assemble the workpiece and electrode wire.
Then, adjust the processing parameters such as pulse width, pulse interval and current.
Controlling the tension and travel speed of the electrode wire is crucial to machining accuracy, and the appropriate electrode wire and machining parameters should be selected according to the characteristics of the workpiece material such as hardness, thickness and shape.
During the machining process, ensure that the working fluid is clean and sufficient to prevent arcing and short-circuiting.
At the same time, timely removal of waste chips generated by machining to protect the machining accuracy and surface quality.
Conclusion
In summary, in today’s industrial manufacturing field, CNC machining technology has become an indispensable part, especially in the manufacture of machinery and mold, its application is wide and deep.
The precision and flexibility of CNC technology makes the processing of complex molds possible, and at the same time, it also greatly improves the quality and performance of molds.
Therefore, the relevant industries should continue to explore and innovate, and further enhance the intelligence and automation level of CNC machining technology to meet the development needs of the manufacturing industry and promote the continuous progress of the whole industry.