Modern tool coatings have significantly contributed to the high efficiency of the CNC machining industry.
Cutting tools have a significant impact on machining quality and machining efficiency. In the previous mode of metal cutting machining, higher cutting forces and temperatures subjected the tools to greater stress.
However, working at high temperatures accelerates tool wear and tear, making it necessary to change the traditional approach of coating tools.
Engineers and manufacturers typically apply tool coatings through three treatments: physical vapor deposition, chemical vapor deposition, and conventional metal coating materials.
Different coatings have different applications. For example, physical vapor deposition treatment can make the tool sharper, but it also reduces the cutting force of the tool.
As material structures continue to evolve, manufacturers should continually improve tool performance. They can achieve this by applying advanced coating technology.
This approach extends the service life of the tool, improves processing efficiency, and shortens production time.
Machine Tool Wear Mechanism Analysis.
Classification of Machine Tool Cutting Materials
In the past period, the market share of tungsten carbide-coated tools and metal-ceramic tools has continued to increase, while the market share of high-hardness alloy tools and ceramic tools has remained largely unchanged.
In terms of processing materials, high-speed steel is primarily used, as it is suitable for cutting and has essential applications in milling and drilling.
Additionally, there are more cemented carbide materials, such as TiN coating, metal ceramics, TiC coating, CBN, and so on, among which the hardness of CBN is second only to diamond.
Tool Wear Mechanisms and Causes
When a tool has a wear problem, it is necessary to measure the wear area, analyze the cause of wear, and determine the location of wear.
Tool wear is a common phenomenon in the metal cutting process, significantly impacting machining accuracy, efficiency, and tool life.
Engineers usually analyze the tool wear mechanism by examining complex physical and chemical processes, including mechanical wear, thermochemical wear, and fatigue wear.
First, mechanical wear
It refers to the contact between the tool and the workpiece during relative motion.
Due to high stress, the tiny raised parts on the tool surface and the workpiece surface rub, strip, or compress each other. This interaction causes the gradual loss of the tool’s material..
Especially at high cutting speeds, the wear resistance of the tool material becomes a key factor affecting tool life.
Second, thermochemical wear
High temperature and chemical reactions generated during the cutting process cause this type of tool wear.
During the cutting process, the contact between the tool and the workpiece generates a large amount of heat. Especially in cases of high cutting speeds and deep cutting, the tool surface temperature rises sharply.
At this stage, high temperatures soften, oxidize, and dissolve the tool material, causing the tool surface to degrade and wear away.
For example, the reaction between the tool surface and the cutting fluid, or the high-temperature reaction with the workpiece material, tends to accelerate wear, especially when cutting higher-hardness materials.
Finally, fatigue wears
During the cutting process, the tool undergoes continuous mechanical loading, particularly alternating stress, resulting in microcracks on its surface.
With the increase in the number of cuts, these micro-cracks gradually expand, eventually leading to tool breakage.
Fatigue wear mainly occurs on the tool contact surface and cutting edge, particularly when the cutting time is longer or when processing hard materials.
In short, the mechanism and cause of tool wear are complex; tool wear results from a variety of factors.
Understanding the mechanism and causes of tool wear is crucial for selecting suitable tool materials, optimizing cutting parameters, and extending tool life.
Advanced Coating Technology
Hard Coating
Engineers primarily characterize hard coatings by their strong wear resistance, high hardness, and resistance to high-temperature oxidation. Standard hard coatings include TiC, TiN, TiCN, TiAlN, and AlTiN, among others.
TiC Coating
Engineers developed and began applying TiC coating a long time ago. This coating has high hardness, good wear resistance, and can resist blade wear.
The use of the C element improves the lubricity of the coating and reduces the friction between the tool and the workpiece.
However, TiC coatings also present certain disadvantages, such as increased brittleness, poor bending resistance, and low toughness, which make them unsuitable for interrupted cutting operations.
Engineers use magnetron sputtering to deposit TiN and TiC coatings on tool steel and compare the wear resistance between coated and uncoated workpieces.
They find that TiC coatings provide extremely high surface hardness, and coated workpieces demonstrate significantly improved wear resistance, while uncoated ones show poor performance under the same conditions.
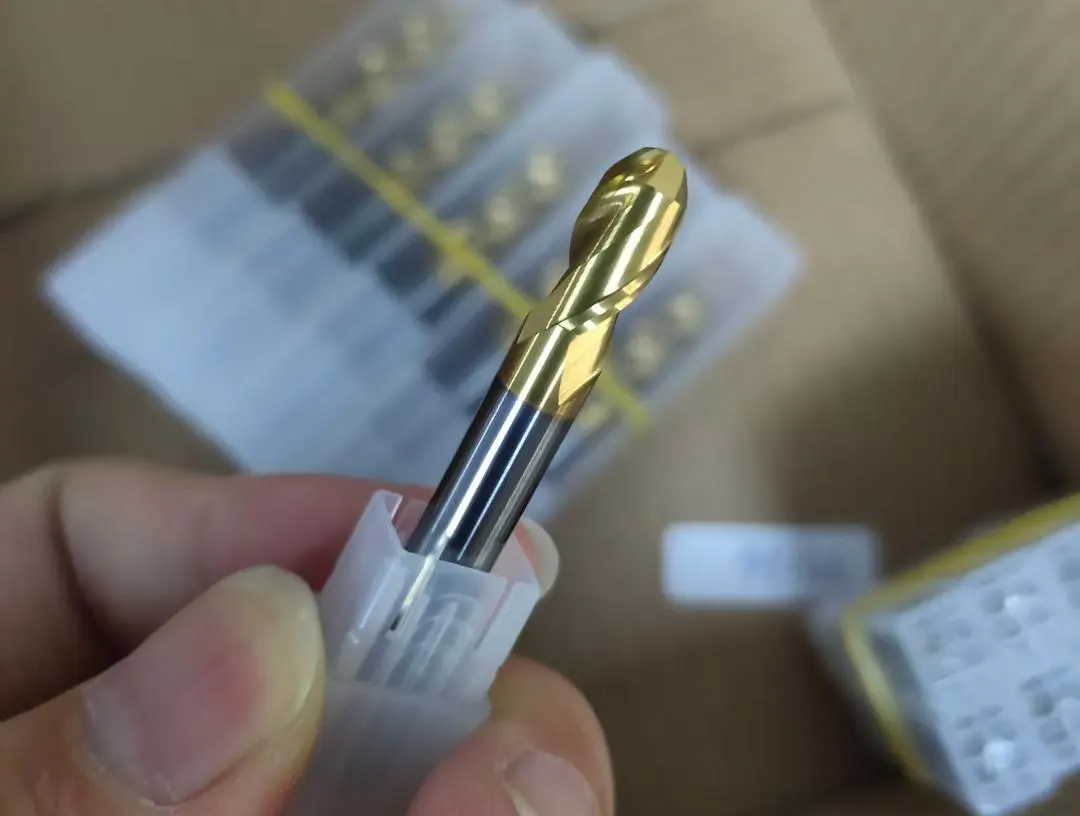
TiN Coatings
Engineers mainly use TiN coatings for coating tool steels.
They have a lower hardness than TiC coatings, but they are chemically inert and exhibit good lubricating properties, as well as a lower affinity for metals.
TiN coatings display a golden color and engineers apply them to the outer surface of tools.
In tool cutting applications, TiN coatings are subject to oxidative wear at temperatures above 500 °C, which affects tool life.
Compared to uncoated ceramic tools, TiN-coated ceramic tools increase cutting life by 2 to 3 times at higher feed rates and maintain good tool surface roughness.
TiN coatings exhibit varying deposition rates and microstructures in different materials, which can lead to differences in physical properties.
Researchers found that depositing TiN coatings on HSS substrates occurred fastest, with the coatings exhibiting a clear columnar structure and high residual stresses of up to -1.83 GPa, which caused a low base bond.
The TiN coating on the TiCN substrate grows more slowly and has a fine columnar structure, which has better abrasion resistance.

TiCN Coatings
TiCN coatings are based on TiN with the addition of C elements to improve the hardness and lubricity of the layer.
Studies have shown that the hardness of TiCN coatings increases as the C element content increases, and the highest wear resistance is achieved at C element ratios between 0.3 and 0.5.
This coating is blue-gray and is often used in ordinary HSS tools at low cutting temperatures.
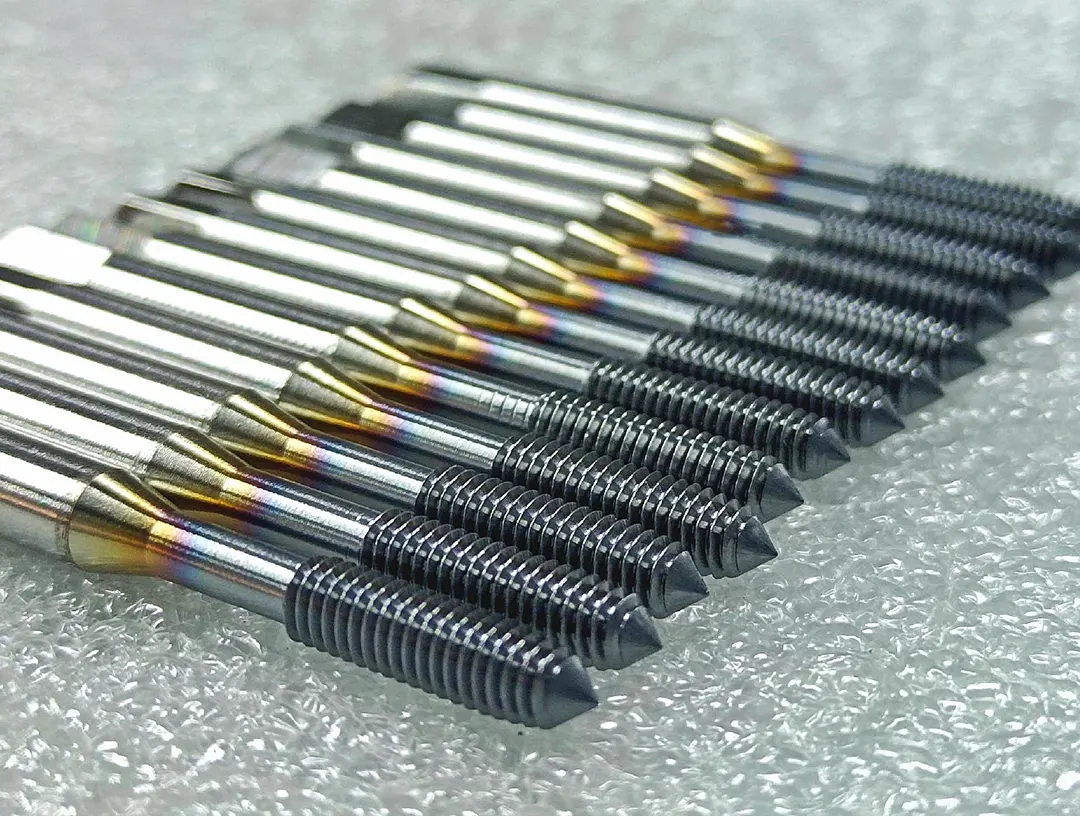
(TiAl)N Coatings
The (TiAl)N coating is formed by adding the element Al to the TiN coating, and the atomic radius of Al is smaller than that of Ti.
By replacing Ti atoms in the TiN coating with Al, researchers can refine the grain size.
This substitution achieves both solid solution strengthening and fine-grain strengthening. As a result, the coating’s wear resistance and hardness improve.
During high-temperature cutting, the oxidation of the Al element produces Al2O3, which enhances the wear and oxidation resistance of the coating and also contributes to heat insulation.
Therefore, (TiAl)N exhibits superior wear resistance, high-temperature resistance, and oxidation resistance, making it suitable for use in aluminum alloy machining and titanium alloy machining.
The content of Al has a significant influence on the coating, and (TiAl)N coatings can be divided into TiAlN coatings and AlTiN coatings based on the Al content.
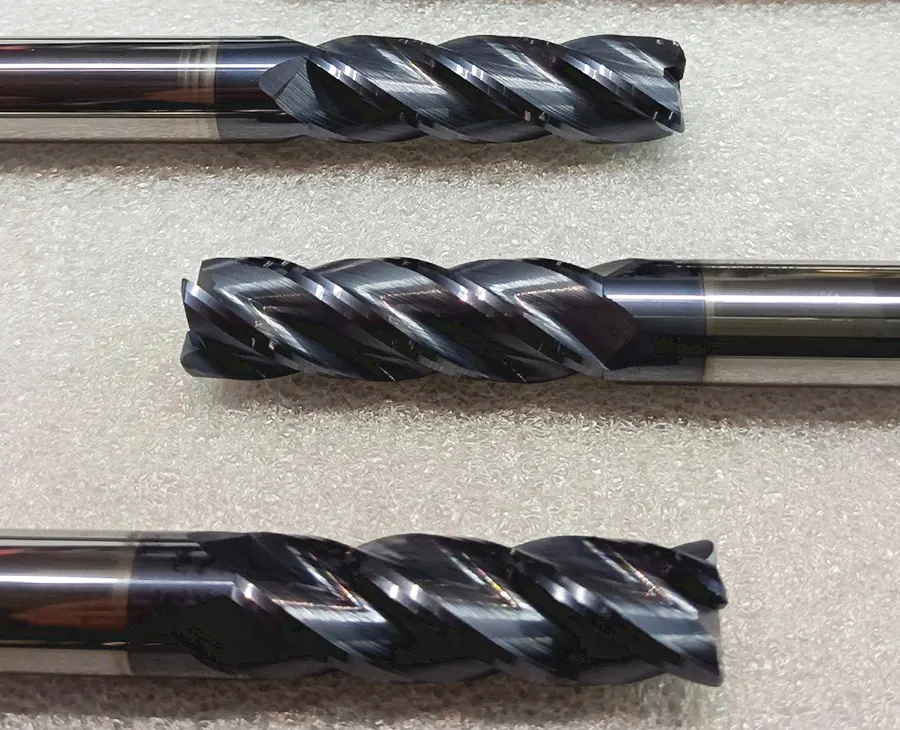
Soft Coatings
Soft coatings have a lower coefficient of friction and better lubrication than hard coatings. Common soft coating materials include WS2, MoS2, CaS2, and TaS2, among others.
During high-speed cutting, the soft coating forms a lubrication film on the tool surface under high temperature and high pressure.
This film effectively reduces the cutting temperature and cutting force.
It also decreases friction during the cutting process, which helps maintain the processing quality of the workpiece.
Additionally, the lubrication film reduces tool wear and tear, thereby extending the tool’s service life.
The WS2/Zr composite soft coatings were deposited on Al2O3/TiN hot-pressed ceramic nanosubstrates by multi-arc ion plating and magnetron sputtering processes.
In the cutting experiments of WS2/Zr composite soft-coated ceramic tools and uncoated ceramic tools, the coefficient of friction, as well as the cutting temperature, of the WS2/Zr composite soft-coated tools was lower.
By the magnetron sputtering method, MoS2 coatings were deposited on Si3N4, TiCN, and WC ceramic substrates, and the life of Si3N4, TiCN, and MoS2-coated tools was extended compared to uncoated tools.
Compared to hard coatings, soft coatings are not sufficiently wear-resistant and are prone to failure under high stress.
To improve the performance of coatings, researchers use femtosecond laser technology to create a nano-structured surface on WC/Co-coated tools.
Then, they deposit WS₂ coatings on this nano-structured surface using intermediate-frequency magnetron sputtering technology.
The interface between the WS₂ and TiAlN coatings remains strongly bonded without delamination.
As a result, WS₂/TiAlN coated tools experience lower cutting forces than TiAlN-coated tools during high-speed cutting, and they exhibit better surface lubrication.
Its surface lubrication is better, and it also shows better wear resistance.
The primary reason is the combination of hard and soft coatings, allowing the advantages of both to be leveraged, thereby enhancing the cutting performance of the coating.
Machine Tool Coating Structure
Single-layer Coatings
A single-layer coating is primarily composed of a composition, where a layer of units is deposited on the surface of the substrate.
The preparation process of single-layer coating is relatively simple, and its mechanical properties can meet the requirements of the general cutting process, making it more widely used in the market.
Single-layer coatings typically deposit a transition layer between the substrate and the coating, with a thickness of tens to hundreds of nanometers, thereby increasing the bonding between the substrate and the coating.
At the same time, other elements can be added to the coating to improve its properties.
Effects of Elemental Additions on Coating Properties
During the preparation of TiAlN and TiAlSiN coatings using magnetron sputtering deposition technology, researchers found that adding Si increases the hardness of the coatings.
The Si element also contributes to fine crystal strengthening and solid solution strengthening effects.
During the preparation of TiN and TiVN coatings by multi-arc ion plating deposition, researchers found that adding the V element reduces the lattice constant of the solid solution.
This reduction makes the coating structure denser. As a result, the coating’s hardness increases, and the bonding strength between the coating and the substrate improves.
Influence of Al and Ti Elements in Cr-Based Coatings
In the process of preparing CrN, CrTiN, CrAlN, and CrTiAlN coatings by non-equilibrium magnetron sputtering, it is found that the addition of the Al element can increase the strength of the coatings.
In contrast, the addition of the Ti element decreases the strength of the coatings.
The addition of Al and Ti elements to form CrTiAlN coatings results in higher hardness and fracture toughness; however, it also introduces larger residual stresses, which contribute to the increased hardness of the CrTiAlN coatings.
The addition of Al and Ti elements to form CrTiAlN coatings exhibits high hardness and fracture toughness, but also results in high residual stress, which leads to a low bonding degree of the CrTiAlN coatings.
Multilayer Coatings
Multi-layer coatings are a combination of two or more coatings applied to the same substrate in a well-designed and sequential manner.
These coatings are made after the deposition of single-layer coatings.
Multi-layer coatings offer the combined advantages of multiple single-layer coatings.
By applying rational design, engineers can reduce stress within the coating. This stress reduction improves the bonding between the coating and the substrate.
Using magnetron sputtering technology, researchers deposited single-layer TiAlN coatings and multilayer TiN/TiAlN coatings on alloy substrates.
The experiments show that TiAlN single-layer coatings tend to peel off easily.
In contrast, TiN/TiAlN multilayer coatings exhibit only slight peeling and demonstrate improved ductility. This improved ductility can extend the service life of the tool.
Nano-multilayer Coatings
Nanostructured coatings are also a common type of multilayer coating, where the thickness of each layer can be compressed down to the nanometer scale as the number of layers increases, resulting in changes to the coating’s properties.
It has been demonstrated that decreasing the modulation period of the coating leads to an increase in the number of layers and interfaces within the coating, resulting in the formation of a superlattice structure.
This, in turn, causes a rapid rise in the surface hardness of the coating.
The toughness of CrN and the hardness and oxidation resistance of TiAlN were utilized to prepare TiAlN/CrN nanomultilayer coatings with different modulation periods using DC magnetron sputtering.
Researchers have demonstrated that at low modulation cycles, TiAlN/CrN nanomultilayer coatings exhibit a superlattice structure and a sharp increase in hardness.
These coatings also show better thermal stability compared to monolayer coatings.
Nanocomposite Coatings
The nanocomposite coating system is to control the growth direction of the nanocrystalline phase of the coating material through specific processing technology, so as to improve the physical and chemical properties of the coating.
Nanocomposite coatings mainly include two phases of nanocrystalline and amorphous phases, and the nanocomposite coatings have higher hardness compared to the mixture rule hardness.
Nanocomposite coatings are more widely used and require two or more parent materials that can be dispersed adequately on the nanoscale.
The most common type of nanocomposite contains one or more hard nanocrystalline phases dispersed in an amorphous rigid matrix at the nanoscale.
This structure limits the mobility of the nanocrystals and strengthens the grain boundaries. As a result, it enhances both the strength and toughness of the coating.
Currently, two types of nanocomposite coatings enhance the hardness of the layer:
Hard phase/challenging phase nanocomposites and hard phase/soft phase nanocomposites.
Hard-phase/soft-phase nanocomposites exhibit unique physical and chemical properties.
A typical example of a nanocomposite coating is the nc-TiN/a-Si3N4 two-phase composite, which offers the advantage of high hardness.
Researchers deposited nanomultilayer TiAlCN/VCN coatings using high-functionality magnetron sputtering combined with unbalanced magnetron sputtering.
They designed the process to construct a low shear strength interface by forming a transverse phase structure, which was induced by carbon elements at the layer level.
This approach aimed to elucidate the layer-by-layer wear mechanism at the nanoscale.
By preparing two X-ray object-shaped hard coatings, one is an nc-TMN/a-Si3N4 composite coating with high Si content, and the other is a covalently bonded Si-B-C-N coating.
It is found that the two coatings have good thermal stability and oxidation resistance at high temperatures.
Functional Gradient Coating
Functional gradient coatings utilize materials with varying properties to achieve enhanced performance.
By designing the coating sequence and controlling the distribution of coating layers, engineers can eliminate sharp interfaces between the coating and the substrate, as well as between different coating layers.
This approach reduces performance mismatches across the coating structure.
As a result, the elemental composition, physicochemical properties, and microstructure of the coating can transition smoothly and continuously.
This continuous transition lowers the interfacial stress, enhances the bonding between the coating and the substrate, and ultimately improves the overall mechanical properties of the coating.
Combined with the composition, material, and properties of the coating, the coating can be distributed in a gradient manner.
Engineers classify coatings based on their different properties and compositions.
These classifications include composition gradient distribution coatings, thermal expansion coefficient gradient distribution coatings, and bonding force–hardness gradient distribution coatings.
Prospect of Tool Coating
Tool coatings can improve cutting efficiency and extend the service life of the tool.
Therefore, engineers need to consider the strength, hardness, high-temperature oxidation resistance, toughness, and adhesion of the coatings comprehensively during the top-level design process.
Therefore, the performance of the tool coating should be improved in the following three aspects.
(1) Substrate Pretreatment.
Before applying the coating, the substrate must be cleaned first, which can enhance the film’s base bonding force and prevent the problem of coating shedding.
Standard substrate cleaning methods can be achieved by using ethanol and acetone solution, through ultrasonic cleaning, and also require the use of argon ion etching.
When cleaning the cemented carbide substrate, grinding and polishing methods can be utilized, followed by sandblasting.
2) Add Other Elements to the Coating.
By adding new elements, coatings can be composed, thereby improving their performance.
For example, adding Al to the (TiAl)N coating leads to the formation of Al₂O₃ under high temperature and high pressure.
This oxide layer blocks the diffusion of oxygen into the coating. At the same time, it prevents the outward diffusion of Ti elements. Together, these effects enhance the coating’s overall resistance to high-temperature oxidation.
The addition of Cr to the (TiAl)N coating promotes the formation of a dense (Al, Cr) oxide layer at high temperatures. This oxide layer inhibits the diffusion of oxygen into the coating.
It also delays the transformation of metastable anatase TiO₂ into the stable rutile phase. As a result, the coating’s oxidation resistance improves significantly.
Based on TiAlN coatings, adding Si elements through deposition can improve the structural compactness of the coatings and enhance their thermal stability and oxidation resistance by forming TiAlSiN coatings.
(3) Optimizing Arc Ion Plating Parameters
Optimize the coating process parameters to improve the internal structure of the coating and enhance its overall performance.
For example, for TiAlN coatings deposited by arc ion plating, optimizing the N2 flow rate can result in a denser coating structure, thereby improving the wear resistance and hardness of the layer.
In the case of AlCrN coatings deposited by arc ion plating, researchers found that reducing the substrate bias could enhance the hardness of the coatings.
However, this adjustment also led to an increase in surface defects caused by large particles.
Therefore, the mechanical properties of the coating should be considered when optimizing the coating parameters.
Conclusion
In conclusion, tool coating can improve the hardness, oxidation resistance, physical and chemical properties, and reduce tool wear during machining.
FAQ
What role do tool coatings play in CNC machining?
Tool coatings significantly improve machining quality and efficiency by enhancing tool hardness, reducing wear, and lowering cutting forces, which extend tool life and improve processing speed.
What methods do engineers commonly use to apply coatings to cutting tools?
Coatings are commonly applied using physical vapor deposition (PVD), chemical vapor deposition (CVD), and conventional metal coating techniques.
How do hard coatings improve tool performance?
Hard coatings such as TiC, TiN, TiCN, and TiAlN offer high hardness, excellent wear resistance, and high-temperature oxidation resistance, which protect the tool under demanding cutting conditions.
What is the difference between hard and soft coatings?
Hard coatings provide durability and wear resistance, while soft coatings reduce friction by forming a lubricating film during cutting, lowering cutting temperature and forces but generally have lower wear resistance.
How does tool wear occur during metal cutting?
Tool wear occurs due to mechanical wear (abrasion and rubbing), thermochemical wear (high-temperature chemical reactions), and fatigue wear (microcracks from cyclic stresses), all of which degrade tool performance over time.
What materials do manufacturers typically select for coated cutting tools?
Materials include tungsten carbide-coated tools, metal-ceramic tools, high-speed steel (HSS), and cemented carbides with coatings like TiN, TiC, and cubic boron nitride (CBN).
How do multilayer and nanomultilayer coatings enhance tool properties?
Multilayer coatings combine advantages of different layers to reduce stress and improve bonding, while nanomultilayer coatings create superlattice structures that increase hardness and thermal stability.
How do elemental additions affect coating properties?
Elements like Si, V, Al, and Ti modify coating hardness, toughness, and oxidation resistance by refining grain size, strengthening the structure, or forming protective oxide layers.
What are functional gradient coatings and their benefits?
Functional gradient coatings gradually change composition and properties through the thickness, reducing interfacial stress and improving bonding and overall mechanical performance.
How can engineers optimize coating process parameters to achieve better tool coatings?
Optimizing parameters such as gas flow rates and substrate bias during deposition can improve coating density, hardness, and bonding, but must balance hardness with surface defect control to ensure performance.