Sheet metal bending is a process in which force is applied to a flat sheet of metal to deform it into a specific shape. The metal is bent around a straight axis, changing its shape without affecting its thickness.
This process is fundamental in creating a wide variety of components used in numerous industries, ranging from automotive to aerospace.
The processing plays a crucial role in modern manufacturing due to its versatility and efficiency. It is essential for producing both simple and complex parts with high precision.
This technique allows manufacturers to shape metal parts with minimal material waste, contributing to cost-effectiveness and the ability to produce parts in various shapes and sizes.
The primary purpose of sheet metal bending is to form the metal into specific angles or shapes that meet the design requirements for various applications. This includes creating bends, flanges, lips, and other structural features.
The bending process allows for the fabrication of parts that are both functional and aesthetically suited to their intended use, whether it’s in consumer electronics, automotive parts, or structural components in construction.
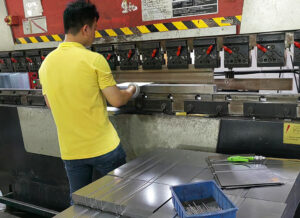
Basic Principles
Sheet metal bending relies on a few key mechanical principles, including tensile and compressive forces. The metal is deformed when the applied force exceeds its yield strength—the point at which the material begins to permanently deform.
During bending, the material undergoes plastic deformation, where the metal flows around the bend axis without returning to its original shape.
The forces involved in bending generate both tensile forces on the outside of the bend and compressive forces on the inside.
The thickness of sheet metal used in bending varies depending on the specific application. Typically, sheet metal thickness can range from very thin gauges, such as 0.1 mm, to thicker sheets up to 50 mm or more.
The material’s thickness will affect the bending method and the equipment used. For thinner materials, less force is required, while thicker materials need more significant bending forces.
The bend radius is a critical factor in sheet metal bending. It refers to the inside radius of the bend, which determines the sharpness of the angle. A common rule of thumb is that the minimum bend radius should equal the sheet metal thickness.
If the bend radius is too small relative to the thickness, the metal may crack or break. Larger bend radii reduce the risk of damage and improve the part’s structural integrity.
Common Sheet Metal Bending Methods
Sheet metal bending techniques vary based on the type of material, the desired bend geometry, and the production requirements. Here are some of the most commonly used sheet metal bending methods:
V-Bending
V-bending is one of the most widely used sheet metal bending methods. In this process, a punch presses the sheet metal into a V-shaped die to form the desired bend.
The depth of the die and the amount of force applied determine the angle and radius of the bend. V-bending is versatile and can be used for a variety of materials and thicknesses.
Subtypes of V-Bending:
- Air Bending: The sheet metal is bent by a punch pressing the material into the die without making contact with the die’s bottom. The bend angle is determined by the amount of force applied. This method is efficient for producing precise bends and allows for some flexibility in bend angles.
- Bottoming: In bottoming, the punch presses the sheet metal all the way into the die, ensuring a more precise and sharper bend. This method is often used for thicker materials where greater accuracy is needed.
- Coining: This method uses a punch to compress the sheet metal completely into the die, resulting in a very precise bend with little springback. Coining is suitable for producing intricate, fine bends and is typically used in high-precision applications.
Roll Bending
Roll bending is ideal for creating large-radius bends, especially for tubular or cylindrical shapes. In this process, the sheet metal passes through three rolls, which progressively bend the material into the desired curve.
Roll bending is particularly effective for manufacturing large parts like pipes, cones, and other curved components. It is also used to create smooth, gradual bends without excessive material stress, which is crucial for maintaining the structural integrity of the part.
U-Bending
U-bending is similar to V-bending, but it utilizes a U-shaped punch and die. This method is used to create U-shaped bends, which are commonly found in structural components and enclosures.
The U-bending process is ideal for parts that need a tight radius with a consistent curve, particularly in applications where the parts need to fit into a specific assembly or system.
Wipe Bending
Wipe bending is a technique that uses a wipe die to apply force to the edges of the sheet metal to form a bend. The wipe die applies minimal force, bending the edges of the material while leaving the center of the sheet relatively flat.
This method is often used for bending thin sheets of metal or when delicate bends are needed without excessive deformation of the material.
Wipe bending is a useful method for producing edges with consistent bends across a large surface area.
Rotary Bending
Rotary bending involves the use of a rotating die or punch to create sharp bends without causing surface scratches or marks.
This method is ideal for applications where the appearance of the material is important, as it minimizes the risk of damage during the bending process.
Rotary bending is also useful when sharp bends are required without the use of large amounts of force, making it a more energy-efficient solution for certain materials.
Step Bending (Bump Bending)
Step bending, also known as bump bending, is a method where multiple V-bends are applied sequentially to create conical shapes. This method allows manufacturers to create parts with gradual changes in thickness or angle.
Step bending is commonly used in applications where precise control over the bend profile is necessary, such as in the production of conical components used in aerospace or automotive industries.
Each of these methods offers unique advantages based on the material, thickness, and geometry of the part being manufactured.
Selecting the appropriate bending method is crucial for optimizing production efficiency, part accuracy, and material integrity.
Factors Influencing Bending
Several factors influence the bending process, determining the final shape, accuracy, and performance of the sheet metal part. Understanding these factors is crucial for achieving optimal results in sheet metal bending operations.
Springback
Springback refers to the material’s tendency to return to its original shape after bending due to its elastic properties.
When a metal is bent, it undergoes plastic deformation, but some of the material will try to revert to its pre-bent state once the bending force is removed.
The extent of springback depends on the material’s properties, such as its yield strength, and the angle and radius of the bend.
To compensate for springback, it is common practice to slightly overbend the material.
This compensates for the amount of springback expected during the bending process, allowing the part to maintain the desired final angle.
The more ductile or flexible the material, the more springback it will likely exhibit, and the greater the need for overbending.
Bend Allowance
Bend allowance is the adjustment made to account for the stretching of the material during the bending process. When a metal sheet is bent, the inner fibers of the bend are compressed, while the outer fibers are stretched.
The amount of material required for a bend depends on the thickness of the sheet and the bend radius. If this adjustment is not made, the final part may not meet dimensional requirements, resulting in poor fit or functionality.
To calculate bend allowance, manufacturers consider the sheet’s thickness, bend radius, and the included bend angle.
Properly accounting for bend allowance ensures that the part fits accurately within a larger assembly and minimizes errors in fabrication.
K-Factor
The K-factor is a critical parameter in determining the bend allowance. It is the ratio of the material’s neutral axis to its thickness and plays a significant role in predicting how the material will behave during bending.
The neutral axis is the point within the material where no stretching or compression occurs during the bending process; it lies between the inside and outside surfaces of the bend.
The K-factor helps to calculate the bend allowance by considering the position of the neutral axis relative to the material’s thickness.
A higher K-factor indicates that the neutral axis is closer to the center of the material, which is common for materials with a high strength-to-weight ratio.
Conversely, a lower K-factor means that the neutral axis is closer to the inside surface, which is typical for more ductile or softer materials.
Selecting the appropriate K-factor is essential for achieving accurate dimensions after bending. Incorrect K-factor values can lead to inaccuracies in the final product, such as incorrect bend angles or lengths.
The K-factor is typically determined through empirical testing or material-specific data, but it can vary based on factors such as material type, thickness, and bend radius.
By understanding and managing these key factors—springback, bend allowance, and the K-factor—manufacturers can produce more precise and functional sheet metal parts, ensuring higher quality and reducing the risk of errors during the bending process.
Materials Commonly Used in Sheet Metal Bending
The choice of material is a critical factor in the sheet metal bending process, as it significantly impacts the ease of bending, final part quality, and performance in application.
Each material has unique properties, including tensile strength, ductility, and formability, which make them suitable for different applications. Below are some of the most commonly used materials in sheet metal bending:
Aluminum
Aluminum is widely used in sheet metal bending due to its lightweight, excellent corrosion resistance, and good formability.
It is relatively soft and easy to bend, making it suitable for a variety of applications in industries like aerospace, automotive, and construction.
Aluminum alloys, such as 5052 and 6061, are commonly used in bending processes because of their combination of strength and ductility.
Additionally, aluminum’s low density makes it a preferred material when weight reduction is crucial. However, its tendency for higher springback can sometimes make precise bending a challenge.
Stainless Steel
It is known for its high strength, durability, and resistance to corrosion, making it an ideal material for applications that require both strength and longevity.
Stainless steel alloys, particularly 304 and 316, are commonly used in industries such as food processing, medical, and chemical engineering, where corrosion resistance is vital.
It’s high tensile strength makes it more challenging to bend compared to aluminum, and it may require more force and specialized tooling.
However, with the right technique and equipment, stainless steel can be bent to achieve precise angles and tight radii.
Mild Steel
Mild steel, or low-carbon steel, is one of the most commonly used materials in sheet metal bending due to its affordability, versatility, and ease of formability.
It offers a good balance of strength and ductility, making it suitable for a wide range of applications, from automotive parts to structural components.
Mild steel is highly weldable and can be bent with relatively low force, though it may require post-bending treatments such as painting or coating to prevent corrosion.
Its lower strength compared to stainless steel or titanium makes it less suitable for heavy-duty applications, but it is ideal for general-purpose manufacturing.
Copper
Copper is widely appreciated for its excellent electrical conductivity, thermal properties, and resistance to corrosion.
It is commonly used in electrical components, plumbing, and heat exchangers. Copper is relatively soft and has good formability, which makes it easy to bend.
However, its tendency to work-harden during bending can create challenges in achieving precise bends, especially in thicker gauges.
Copper’s high cost compared to mild steel and aluminum limits its use in large-scale manufacturing, but it is invaluable for specialized applications requiring superior conductivity and corrosion resistance.
Brass
Brass is an alloy of copper and zinc, known for its attractive appearance, corrosion resistance, and ease of machining.
It is often used in applications requiring low friction, such as fittings, valves, and musical instruments. Brass is highly formable and easy to bend, though it can be prone to cracking or cracking when bent too sharply.
Its good corrosion resistance makes it ideal for use in environments exposed to moisture or corrosive elements. However, the cost of brass is higher than mild steel, limiting its use to premium applications where its properties are necessary.
Titanium
Titanium is a high-performance material known for its exceptional strength-to-weight ratio, corrosion resistance, and ability to withstand extreme temperatures. It is commonly used in aerospace, medical implants, and marine environments.
While titanium’s strength and durability are significant advantages, they also make it more challenging to bend compared to materials like aluminum or mild steel. Titanium requires high-quality tooling, precise bending methods, and, often, higher forces for successful bending.
Additionally, its relatively high cost makes it suitable primarily for specialized, high-performance applications rather than general manufacturing.
Galvanized Steel
Galvanized steel is carbon steel coated with a layer of zinc to improve its resistance to corrosion. This material is commonly used in construction, automotive, and appliance industries, where corrosion resistance is crucial but cost needs to be kept low.
Galvanized steel is relatively easy to bend, similar to mild steel, but care must be taken to avoid damaging the zinc coating during the bending process. If the coating is scratched or removed, the material’s corrosion resistance is significantly reduced.
The material is widely used for outdoor applications, including roofing and automotive parts, due to its long-lasting protection against rust and environmental degradation.
Each material used in sheet metal bending offers distinct advantages and challenges. The selection of the appropriate material depends on factors such as the desired properties of the final part, the specific application, and the bending requirements.
Understanding these materials and their characteristics allows manufacturers to optimize the bending process and achieve high-quality results tailored to the needs of each project.
Sheet Metal Bending Tools and Equipment
The right tools and equipment are essential for achieving precise and accurate bends in sheet metal. Different types of bending processes require specific machines, each designed to meet the needs of various bending applications.
Below are the key tools and equipment commonly used in sheet metal bending:
Press Brake
The press brake is one of the most widely used tools in sheet metal bending, offering versatility and precision. It consists of a punch and die setup, with the punch applying force to bend the material into the desired shape.
The press brake can be used for a variety of bending operations, including V-bending, air bending, and bottoming. Its flexibility allows it to accommodate different bending angles, radii, and material thicknesses.
Press brakes are available in both mechanical and hydraulic versions, with hydraulic press brakes being more common due to their ability to handle larger material sizes and provide greater control over bending forces.
Key Features:
- Versatile tool for different bending processes.
- Precise control over the bending force and angle.
- Suitable for various material types and thicknesses.
- Can be equipped with CNC controls for enhanced accuracy.
Rollers
Rollers, also known as roll benders, are used primarily in roll bending to create cylindrical or curved shapes in sheet metal.
Roll bending is ideal for producing parts like tubes, pipes, and arcs, with the rollers applying gradual, controlled pressure to the material as it passes through them.
This method is particularly useful for creating parts with large radii and is commonly employed in industries such as automotive, aerospace, and HVAC.
Rollers come in different configurations, including three-roll and four-roll machines, with each offering specific advantages based on the complexity of the bend required.
The machine’s rollers gradually bend the material without causing stress or deformation, making it ideal for creating smooth, continuous curves.
Key Features:
- Ideal for creating large-radius bends, tubes, and cylinders.
- Allows for continuous bending of long material lengths.
- Suitable for both thin and thick materials.
- Typically used for non-angular, smooth curves.
Folding Machines
Folding machines are designed specifically for bending sheet metal along a straight line, often producing right-angle folds.
These machines are particularly useful in applications where precise, straight bends are required, such as for creating boxes, trays, or other enclosures.
Folding machines work by clamping the sheet metal between two surfaces and applying force through a folding blade to create the bend.
This equipment is ideal for thinner gauges of sheet metal and offers high precision for angles, especially when consistent bending is required across multiple parts.
Key Features:
- Designed for creating precise right-angle bends.
- Used primarily for thinner sheet metal gauges.
- Provides high accuracy and repeatability.
- Often used in industries such as metalworking and fabrication.
CNC Machines
Computer Numerical Control machines provide automated and highly precise control over the sheet metal bending process. CNC press brakes, in particular, allow for complex bends to be executed with high accuracy and repeatability.
Using computer programming, the machines can perform precise bending operations with minimal human intervention, ensuring consistent quality across production runs.
These machines are especially beneficial when working with parts that require intricate bends, tight tolerances, or high production volumes.
The ability to program complex bending sequences into the machine’s control system allows manufacturers to reduce setup times, improve part consistency, and increase overall production efficiency.
Key Features:
- Automated control for precise, repeatable bends.
- Can handle complex and multi-axis bending operations.
- Reduces the need for manual intervention and minimizes human error.
- Ideal for high-volume production and intricate bending tasks.
The choice of bending tools and equipment plays a crucial role in the overall quality, efficiency, and versatility of the sheet metal bending process.
Press brakes, rollers, folding machines, and CNC machines each serve specific purposes and provide distinct advantages depending on the application.
Understanding the capabilities of these tools helps manufacturers optimize their bending processes, reduce material waste, and achieve high-quality results with greater precision and speed.
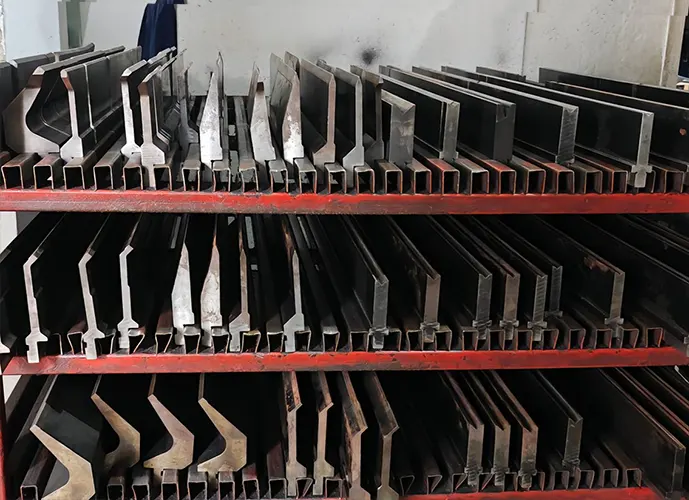
Design Considerations in Sheet Metal Bending
When designing parts for sheet metal bending, several key factors must be considered to ensure the final product meets both functional and aesthetic requirements while maintaining material integrity.
These design considerations impact the ease of manufacturing, the cost of production, and the quality of the finished part. Below are essential design guidelines for effective sheet metal bending:
Bend Radius
The bend radius refers to the inside radius of a bend and is one of the most important factors in the design process. It is crucial to ensure that the bend radius is large enough to avoid material cracking, fatigue, or failure.
A small bend radius can lead to excessive stress on the material, resulting in fractures, cracks, or compromised part strength.
In general, the minimum bend radius should be at least equal to the material thickness, although it may need to be larger depending on the material type, thickness, and the bending process used.
A larger bend radius improves the flow of the material and minimizes the risk of defects.
Design Tip: Always specify the bend radius based on the material properties and the desired part functionality to avoid the risk of material failure or performance issues.
Material Thickness
Material thickness directly influences the amount of force required to achieve the desired bend and the bend radius.
Thicker materials require more bending force and may need larger radii to maintain their structural integrity.
Conversely, thinner materials are more easily bent but may be more prone to deformation if not handled correctly.
Design Tip: Consider the material thickness when designing bends, as thicker materials may require more robust tooling, while thinner materials may need special handling to avoid excessive bending or distortion.
Springback Compensation
Springback is the tendency of a material to return to its original shape after the bending force is removed.
This phenomenon occurs due to the elastic properties of the material and can result in a slight deviation from the intended bend angle.
Springback is particularly significant in materials with higher tensile strength, such as stainless steel or titanium.
To compensate for springback, the bending angle is often over-bent slightly during the initial bending process.
The exact amount of over-bend required depends on the material type, thickness, and the final desired angle.
Design Tip: Account for springback by slightly over-bending the part during the design phase. The degree of over-bend will vary depending on material properties and the bending method.
Hole and Slot Placement
When designing sheet metal parts with holes or slots near bends, it is essential to consider the potential distortion that may occur during the bending process.
Holes or slots that are too close to the bend may become distorted, lose their shape, or even crack.
To prevent this, it is recommended to maintain an adequate distance between holes/slots and the bend area.
Design Tip: Ensure sufficient spacing between holes/slots and bends to avoid distortion. This allows the metal to retain its shape and structural integrity after bending.
Relief Cuts
Relief cuts are strategically placed cuts in the material near bends to prevent excessive material bulging or tearing during the bending process.
These cuts help control the flow of material and reduce the likelihood of defects such as wrinkling or tearing at the bend point. They are particularly useful when working with thicker materials or complex geometries.
Design Tip: Incorporate relief cuts near the bend area to prevent material bulging and ensure smooth bends. Relief cuts can also reduce the required bending force and improve part quality.
Minimum Flange Lengths
Flange lengths play a critical role in the design of sheet metal parts. The flange must be long enough to provide adequate support for the bend but not too long that it leads to excessive material waste or difficult manufacturing.
Minimum flange lengths are essential to ensure that the bending process is smooth and the part remains structurally sound.
Design Tip: Ensure that flanges are long enough to support bending but not excessively long to avoid waste and manufacturing difficulties.
Refer to material thickness and bend radius to determine optimal flange length.
Proper design considerations are key to achieving high-quality, functional sheet metal parts that meet both performance and manufacturing requirements.
By understanding and implementing the right bend radius, material thickness, springback compensation, hole/slot placement, relief cuts, and flange lengths, manufacturers can produce parts that are easier to fabricate, more durable, and more cost-effective.
These design principles help minimize defects, optimize material usage, and ensure that the final product meets its intended function without compromising on quality.
Common Sheet Metal Bending Challenges
Sheet metal bending is a widely used process in manufacturing, but it comes with its own set of challenges that need to be carefully managed.
By understanding and addressing these challenges, manufacturers can improve the quality of the parts, reduce material waste, and optimize the overall production process.
Below are some of the most common challenges faced during sheet metal bending and ways to mitigate them.
Cracking
Cracking is a common issue when bending brittle materials or when forming tight radii. Materials like high-strength steel or certain alloys tend to have lower ductility, making them more prone to cracking during bending, especially if the bend radius is too small.
Cracking occurs as a result of excessive stress being applied to the material during the bending process, causing the material to fracture.
Solution: To prevent cracking, it is essential to ensure that the bend radius is sufficiently large relative to the material thickness.
Additionally, selecting materials with better ductility and performing the bending process at the proper temperature can help reduce the risk of cracking. Using proper tooling and applying lubrication may also help minimize stress on the material.
Springback
Springback is the tendency of the material to return to its original shape after the bending force is released. This effect is most noticeable in materials such as aluminum, stainless steel, and other high-tensile materials.
The amount of springback depends on factors such as the material’s yield strength, thickness, and the angle of the bend. If springback is not compensated for, it can result in inaccurate bend angles and shape distortion.
Solution: To account for springback, it is common practice to slightly over-bend the material during the bending process. The degree of over-bend depends on the material properties, thickness, and bending angle.
Using a material-specific springback formula or trial-and-error methods can help in fine-tuning the bending process to achieve the correct final angle.
Material Thickness Variations
Material thickness variations can occur due to inconsistencies in the manufacturing process or variations in the raw material.
These thickness fluctuations can lead to inaccuracies in the bending process, affecting the consistency of bend angles, radii, and overall part quality.
Thicker areas may require more force to bend, while thinner areas may not bend as effectively.
Solution: To mitigate the impact of material thickness variations, it is essential to inspect the raw material before the bending process. Consistent material quality should be verified, and where possible, parts should be designed to minimize the impact of thickness variations.
Automated CNC machines with advanced controls can also help account for thickness discrepancies during the bending process, ensuring better consistency in the final product.
Surface Damage
Surface damage, such as scratches, gouges, and marks, is a common challenge when bending sheet metal.
This is especially problematic when working with delicate or polished materials, such as stainless steel or aluminum, where the visual appearance of the final part is important.
Surface damage can occur if the tooling is not properly aligned, if the material is not properly supported, or if excessive force is used during the bending process.
Solution: To prevent surface damage, it is important to use clean and properly maintained tooling.
Additionally, proper lubrication can help reduce friction and minimize the risk of scratches. For materials prone to surface damage, a protective film or coating can be applied to protect the surface during bending.
Furthermore, using a bending process that provides adequate support, such as air bending or rotary bending, can help reduce the risk of surface imperfections.
While sheet metal bending is a widely used process in various industries, it presents several challenges that need to be addressed for optimal results.
By understanding and managing issues like cracking, springback, material thickness variations, and surface damage, manufacturers can ensure that the bending process is efficient, accurate, and results in high-quality parts.
Proper planning, material selection, and tooling maintenance are essential to overcoming these challenges and achieving consistent, reliable results.
Applications of Sheet Metal Bending
Sheet metal bending plays a crucial role in a variety of industries due to its versatility, cost-effectiveness, and ability to produce complex shapes and structures.
The process is employed across numerous sectors, from automotive manufacturing to consumer electronics, offering flexibility and precision for a wide range of applications. Below are some key industries where sheet metal bending is widely used.
Automotive Industry
In the automotive sector, sheet metal bending is fundamental for producing various components, including body panels, structural parts, and chassis components.
These parts must meet strict requirements for strength, durability, and weight reduction while maintaining design flexibility.
Sheet metal bending allows manufacturers to create components with intricate shapes and precise angles, essential for meeting both functional and aesthetic demands in automotive design.
Applications:
- Body panels: Creating car body parts, such as doors, hoods, and fenders, that need to be lightweight yet strong.
- Structural components: Parts like brackets, reinforcements, and frames that contribute to vehicle safety and structural integrity.
- Interior components: Such as console parts and dashboard supports.
Aerospace Industry
The aerospace industry relies on sheet metal bending to manufacture complex and lightweight components used in aircraft construction.
Components such as body panels, wing sections, and fuselage frames must be strong yet lightweight to ensure safety and performance.
Sheet metal bending provides the precision needed to fabricate these parts with minimal weight while maintaining structural strength.
Applications:
- Aircraft body panels: For both internal and external surfaces of airplanes, ensuring aerodynamic performance.
- Structural parts: Including frames, bulkheads, and brackets that form the internal skeleton of aircraft.
- Landing gear and support components: Manufactured with high precision to handle the stresses of takeoff, flight, and landing.
Consumer Electronics
In consumer electronics, sheet metal bending is used to create housings and enclosures for various electronic products.
These housings need to provide structural protection while also being lightweight, cost-effective, and aesthetically pleasing.
Sheet metal bending is ideal for producing these components due to its ability to handle both functional and aesthetic design challenges.
Applications:
- Smartphone and tablet enclosures: Thin metal housings for mobile devices that offer both protection and a sleek design.
- Laptop casings: Robust yet lightweight cases for computers and laptops.
- Television and appliance covers: Durable and aesthetically pleasing covers for consumer electronic devices.
Industrial Machinery
Sheet metal bending plays a vital role in the production of parts for industrial machinery, offering the ability to create durable and functional components with complex shapes.
From machine tool housings to frames and structural elements, sheet metal bending ensures that the components meet rigorous standards for strength and reliability.
Applications:
- Machine tool parts: Creating structural components such as frames, housings, and brackets.
- Conveyor systems: Components for industrial conveyors, such as support rails, frames, and guides.
- Pressure vessels and tanks: Durable containers used in various industrial processes, including the chemical and oil industries.
Infrastructure and Construction
Sheet metal bending is integral to the infrastructure and construction industries, where it is used to fabricate components for buildings, bridges, and other structures.
Components like metal roofing, wall panels, and support beams are all produced through sheet metal bending. These parts must meet stringent standards for strength, durability, and safety, especially in construction applications.
Applications:
- Building panels: Metal panels for both the exterior and interior of buildings, offering aesthetic and functional benefits.
- Roofing materials: Corrugated and flat metal roofing that is lightweight yet capable of withstanding weather conditions.
- Structural support: Beams, columns, and other structural components that provide support and stability to buildings and bridges.
Sheet metal bending is a versatile and essential process across multiple industries, from automotive and aerospace to consumer electronics, industrial machinery, and infrastructure.
By offering precise control over material shaping, this process enables the creation of strong, lightweight, and complex components, making it an indispensable tool in modern manufacturing.
With its broad range of applications, sheet metal bending continues to contribute to innovation and efficiency in various sectors, ensuring that products meet both functional and aesthetic requirements.
Advantages of Sheet Metal Bending
Sheet metal bending offers numerous advantages that make it a preferred method in manufacturing across various industries.
From speed and efficiency to cost-effectiveness and precision, this process has proven itself to be invaluable in producing complex components that meet high-quality standards. Below are the key advantages of sheet metal bending.
Speed and Efficiency
One of the primary benefits of sheet metal bending is the speed and efficiency it offers, particularly when using advanced technologies such as CNC (Computer Numerical Control) machines.
CNC machines enable quick, automated bending processes that can be replicated with high consistency and accuracy.
This results in faster production times and the ability to produce large volumes of parts in a short period, making it ideal for high-demand manufacturing environments.
- Rapid prototyping: The ability to quickly create prototypes, allowing for faster design iterations and testing.
- High-volume production: Automation in CNC machines allows for the continuous production of parts, significantly reducing lead times and increasing throughput.
High Precision
Sheet metal bending is capable of achieving very tight tolerances, which is critical in industries such as aerospace, automotive, and electronics, where precise measurements and quality control are essential.
Advanced equipment, such as CNC-controlled press brakes, can achieve accuracy levels down to ±0.05 mm, ensuring that parts fit together perfectly and meet strict specifications.
- Consistent results: Repetitive bends can be made with consistent accuracy across large batches.
- Tight tolerances: This ensures parts meet functional and dimensional specifications, reducing the need for rework or corrections.
Cost-Effectiveness
Sheet metal bending is a cost-effective manufacturing process due to its minimal need for post-processing and the absence of welding or other complex joining methods.
Unlike other processes, such as casting or forging, sheet metal bending requires fewer steps and less material waste, lowering production costs.
Additionally, with automated systems like CNC machines, labor costs are reduced, further enhancing the process’s affordability.
- Minimal post-processing: After bending, the part typically requires little to no additional work, reducing time and cost.
- No welding required: Eliminating the need for welding helps avoid additional costs associated with joining, such as labor, equipment, and inspection.
Lightweight
Sheet metal bending enables the production of strong, durable components with minimal material.
This makes it an excellent choice for industries that require lightweight parts without sacrificing strength, such as the automotive and aerospace industries.
The process allows for the optimization of material use, resulting in reduced overall weight and material costs while maintaining structural integrity.
- Material efficiency: Bending utilizes a thin sheet of metal, which helps reduce waste and material costs.
- Strength-to-weight ratio: Components are often lighter than alternatives made from solid or cast materials, providing high strength with reduced weight.
The advantages of sheet metal bending—speed, precision, cost-effectiveness, and lightweight construction—make it an essential technique in manufacturing.
With the ability to produce high-quality parts quickly and efficiently, it remains a top choice for industries ranging from automotive and aerospace to electronics and industrial machinery.
As technology continues to advance, the benefits of sheet metal bending will likely expand, further cementing its place in modern manufacturing practices.
Limitations of Sheet Metal Bending
While sheet metal bending offers numerous advantages, it also presents certain limitations that need to be considered during the design and manufacturing process.
Understanding these limitations is essential for achieving the desired quality and functionality in the final product. Below are the key limitations of sheet metal bending.
Thickness Limits
One of the primary limitations in sheet metal bending is the material thickness. As the thickness of the metal increases, the bending process becomes more challenging. Thicker materials generally require larger radii to avoid cracking or damage during bending.
This can limit the types of bends that can be achieved and may necessitate more powerful machinery or special dies to handle the increased thickness.
- Large radii required for thicker materials: As the thickness increases, the radius of the bend must be adjusted to accommodate the material’s increased resistance to deformation.
- Bending force increases with thickness: The force required to bend thicker materials is significantly higher, which can lead to limitations on the type of machinery that can be used or the bending angles achievable.
Material Limitations
Certain materials are more challenging to bend than others, particularly brittle materials such as certain alloys or cold-worked metals. Brittle materials have a higher risk of cracking, especially when subjected to tight bends or sharp radii.
This limits the scope of materials that can be used for sheet metal bending and requires careful selection to avoid damage.
- Risk of cracking: Materials with low ductility or higher hardness tend to crack or break when bent too tightly, making them unsuitable for applications requiring sharp bends.
- Brittle materials: Metals such as cast iron or certain high-carbon steels may not be ideal for bending without preheating or post-treatment to improve their ductility.
Design Constraints
Sheet metal bending is constrained by certain design factors, particularly when considering the bend radius and material thickness.
The bend radius is a critical factor in ensuring that the material does not experience cracking, fatigue, or other failures.
Designs with tight bend radii or intricate features may not be feasible unless they are optimized for the material’s specific bending capabilities.
- Minimum bend radius: Every material has a minimum bend radius, which is determined by its thickness and ductility. Trying to achieve a bend smaller than this radius can lead to poor results, such as cracking or distortion.
- Thickness and geometry limitations: The complexity of the bend and the thickness of the material often dictate the feasibility of achieving a specific design. For example, highly complex or tight geometry in thicker materials may not be achievable without special processes or tooling.
The limitations of sheet metal bending, such as thickness constraints, material limitations, and design restrictions, must be carefully managed to ensure successful manufacturing.
By understanding these challenges, engineers and designers can make informed decisions about material selection, bend radius, and process optimization to achieve high-quality results while minimizing risks such as cracking or excessive material waste.
Addressing these limitations during the design phase is crucial for ensuring the final product meets the required specifications and performs effectively in its intended application.
Future Trends and Advances in Sheet Metal Bending
As technology continues to evolve, the field of sheet metal bending is experiencing significant advancements that are shaping the future of manufacturing.
These innovations aim to improve efficiency, precision, and cost-effectiveness while addressing the challenges traditionally faced in bending operations.
Below are the key trends and advances in sheet metal bending that are transforming the industry.
CNC Automation
The increased use of CNC (Computer Numerical Control) automation is one of the most impactful developments in sheet metal bending.
CNC machines provide a high level of precision and repeatability, making them essential for producing complex parts with tight tolerances.
Automation in the bending process allows for faster production times, reduced human error, and the ability to perform highly intricate bends that would be challenging with manual methods.
- Precision and repeatability: CNC machines can execute the same bending operation with consistent accuracy, ensuring that each part meets the required specifications.
- Faster production cycles: Automation reduces setup time, enabling faster turnaround for both small and large production runs.
- Increased flexibility: CNC machines can be easily reprogrammed to handle different parts, allowing manufacturers to adapt quickly to changes in design or production requirements.
Simulation Software
Simulation software has become an invaluable tool in the sheet metal bending process, offering the ability to optimize bend designs and predict material behavior before physical production begins.
This technology uses computer modeling to simulate the bending process, providing insights into potential issues such as springback, material deformation, and strain distribution.
By leveraging simulation, manufacturers can optimize their designs for better performance and reduced material waste.
- Optimized bend design: Simulation allows engineers to visualize how a part will behave during bending, enabling them to adjust parameters like bend angles, radii, and material choice for optimal results.
- Predicting material behavior: The software helps predict how different materials will respond to bending forces, allowing for more accurate planning and fewer costly mistakes.
- Cost savings: By identifying potential issues early in the design phase, manufacturers can reduce scrap rates and avoid expensive rework during production.
Smart Manufacturing
The integration of smart manufacturing technologies, including artificial intelligence (AI) and robotics, is revolutionizing sheet metal bending operations.
Smart manufacturing systems allow for real-time monitoring, data collection, and decision-making, enabling faster and more efficient bending processes.
AI can optimize bending parameters dynamically based on real-time feedback, while robotics can handle repetitive tasks with high speed and precision.
- AI and machine learning: AI algorithms can analyze data from the bending process, continuously optimizing machine settings for better results and increased efficiency.
- Robotics and automation: Robotic systems are increasingly being used in bending operations to handle material loading and unloading, perform secondary operations like trimming, and even manage bending tasks with high precision.
- Real-time process optimization: Smart manufacturing systems enable manufacturers to monitor every aspect of the bending process, adjusting operations in real time to ensure maximum efficiency and accuracy.
Conclusion
Advancements in automation, simulation, and smart manufacturing technologies are shaping the future of sheet metal bending.
As CNC machines become more automated, simulation software becomes more sophisticated, and AI and robotics are integrated into manufacturing systems, the industry is poised to see significant improvements in speed, precision, and cost-effectiveness.
These innovations will continue to drive the development of more complex parts and products, meeting the demands of increasingly intricate and high-performance applications across a wide range of industries.
FAQ
What is sheet metal bending and why is it important in manufacturing?
Sheet metal bending is a forming process where force is applied to a flat sheet of metal, deforming it around a straight axis without altering its thickness. It is vital in modern manufacturing because it enables the creation of both simple and complex components with high precision, minimal material waste, and cost efficiency for industries such as automotive, aerospace, electronics, and construction.
What are the most common sheet metal bending methods?
The most widely used sheet metal bending methods include V-bending (air bending, bottoming, coining), roll bending, U-bending, wipe bending, rotary bending, and step bending. Each method offers specific advantages depending on the required bend angle, radius, material type, and production needs.
How does bend radius affect sheet metal bending quality?
The bend radius—the inside radius of a bend—directly impacts material flow, structural integrity, and the risk of cracking. A general rule is that the minimum bend radius should be equal to the sheet’s thickness. Smaller radii can cause fractures, while larger radii help maintain part strength and durability.
What factors influence the accuracy of sheet metal bending?
Key factors include springback, bend allowance, and the K-factor. Springback is the tendency of metal to partially return to its original shape after bending, bend allowance accounts for material stretching, and the K-factor defines the position of the neutral axis. Properly managing these factors ensures accurate dimensions and angles.
Which materials are best suited for sheet metal bending?
Common materials include aluminum, stainless steel, mild steel, copper, brass, titanium, and galvanized steel. The choice depends on application needs, such as strength, corrosion resistance, weight, and formability. For example, aluminum is lightweight and easy to bend, while stainless steel offers high strength but requires more force.
What tools and machines are used for sheet metal bending?
The most common equipment includes press brakes, rollers, folding machines, and CNC bending machines. Press brakes are versatile for different bend types, rollers are ideal for large-radius curves, folding machines excel at straight folds, and CNC machines deliver automated precision for complex and high-volume production.
How do manufacturers prevent cracking during sheet metal bending?
To reduce cracking, manufacturers ensure the bend radius is sufficient for the material thickness, choose ductile materials when possible, apply proper lubrication, and sometimes preheat the metal. Using suitable tooling and avoiding overly tight bends also helps maintain material integrity.
How is springback compensated in sheet metal bending?
Springback is usually countered by slightly over-bending the sheet beyond the intended angle. The exact over-bend value depends on the material’s yield strength, thickness, and bend angle. CNC machines can automatically adjust for springback to ensure consistent accuracy.
What are the main applications of sheet metal bending across industries?
Sheet metal bending is used in automotive body panels and structural components, aerospace fuselage frames and wing parts, consumer electronics housings, industrial machinery frames, and construction materials like roofing panels and structural beams. Its versatility makes it critical in both functional and aesthetic applications.
What are the key advantages of sheet metal bending over other forming methods?
Advantages include high precision, speed, cost-effectiveness, lightweight component production, and minimal material waste. With advanced CNC technology, manufacturers can achieve tight tolerances, rapid prototyping, and consistent high-volume production while keeping costs low and quality high.